Preguntas Frecuentes
Un sellado inductivo consistente, es el resultado de un proceso consistente. Aquellas funciones indirectas o que aparentemente no tiene relación con el sellado en sí, resultan fundamentales a la hora de obtener un buen sellado. Para lograr un sellado apropiado, todo el borde del sello debe estar en contacto con la boca del envase con una torsión adecuada, además el material del sello y el material del envase deben ser compatibles entre sí, y, por último debe haber suficiente exposición al campo magnético para que se caliente el aluminio (sello) y de esta forma lograr el sellado del envase. Una falla en cualquier punto de este procedimiento puede dar como resultado un sello de mala calidad o inconsistente. Casi siempre, lo primero que se hace es culpar erróneamente a la selladora inductiva.
La causa más común por la que se obtienen sellos inconsistentes es la falta de fuerza (torsión) para asegurar que todo el borde del sello se encuentre en contacto con la boca del envase, otra causa muy común es una exposición insuficiente del sello de aluminio al campo magnético. Por último se puede sospechar de la imcompatibilidad entre los materiales o se puede suponer que el lote de sellos o de envases utilizados sea otro del que se estuvo utilizando hasta ese momento.
Muchas veces se hace referencia al sistema de sellado por inducción como “selladora por calor”. El proceso actual de sellado por inducción es el resultado de la conversión de energía inducida dentro del sello. De esta manera, transformando energía de eléctrica a magnética, de magnética a eléctrica, y finalmente de eléctrica a térmica o energía caliente, es que se completa el procedimiento y se logra el sellado. La fuente de potencia de la selladora convierte la energía que provee la compañía proveedora de electricidad a una corriente alterna regulada de alta frecuencia. El cabezal de sellado transforma la energía eléctrica en un campo magnético. El sello de aluminio se expone a dicho campo magnético. La resistencia del disco de aluminio del sello interactúa con la energía eléctrica llamada corriente circulante, la cual resulta en el calentamiento del aluminio (sello). El disco de aluminio deberá calentarse lo suficiente como para derretir la capa de polímero que se encuentra sobre el mismo. Una vez que se enfría el polímero se adherirá tanto al sello como a la boca del envase, creando de esta manera un sellado hermético.
El sello está compuesto por una lámina de aluminio con una capa de polímero aplicada del lado que entrará en contacto con la boca del envase. La cera se utiliza como adhesivo a fin de mantener el sello en su lugar dentro de la tapa. Cuando se calienta el disco de aluminio, se desarrollan dos funciones: el derretimiento del polímero logra que se produzca el sellado, y la capa de cera al derretirse, libera al foil del respaldo de cartón. La cera es absorbida por el cartón y el sello se adhiere a la boca del envase. El espacio que queda vacante al derretirse la capa de cera, por más delgada que ésta sea, hace que se afloje la tapa.
Muchas aplicaciones de llenado de envases utilizan un retorsionador de tapas en la línea de llenado, ya que un envase con la tapa floja da la sensación de que el producto no es seguro. Dado que el disco de aluminio retiene el calor, deberá disiparse la energía eléctrica antes de romper el polímero, ya que, si al mismo no se le permite “curar” puede ocasionar fallas en el sellado. Es por todo esto que el mejor lugar para ubicar un retorsionador de tapas será tan lejos o tan al final de la línea de producción como sea posible.
El diseño del cabezal de sellado está basado en el punto en el que el sello se encuentra ubicado en relación a la parte superior de la tapa. Tal y como se ha mencionado previamente, el campo magnético desarrollado por la corriente alterna aplicado al espiral del cabezal de sellado interactúa con el disco de aluminio. La distancia a la cual el campo magnético se puede propagar a través del aire es muy limitada. Lo ideal sería que el disco de aluminio estuviera a una distancia entre 1/8” a ¼” de la parte inferior del cabezal de sellado. Este área proporciona el máximo de fuerza del campo magnético. Cuando el sello se encuentra más lejos, como ser en el caso de las tapas con pico o los envases CRC, el campo magnético debe ser aplicado desde el costado de la tapa (de lado). Este tipo de cabezales de sellado se conocen como cabezales tipo túnel o canal. La ubicación de los componentes que desarrollan el campo magnético se encuentran debajo de la parte superior del envase, adyacentes a la posición del sello de la tapa.
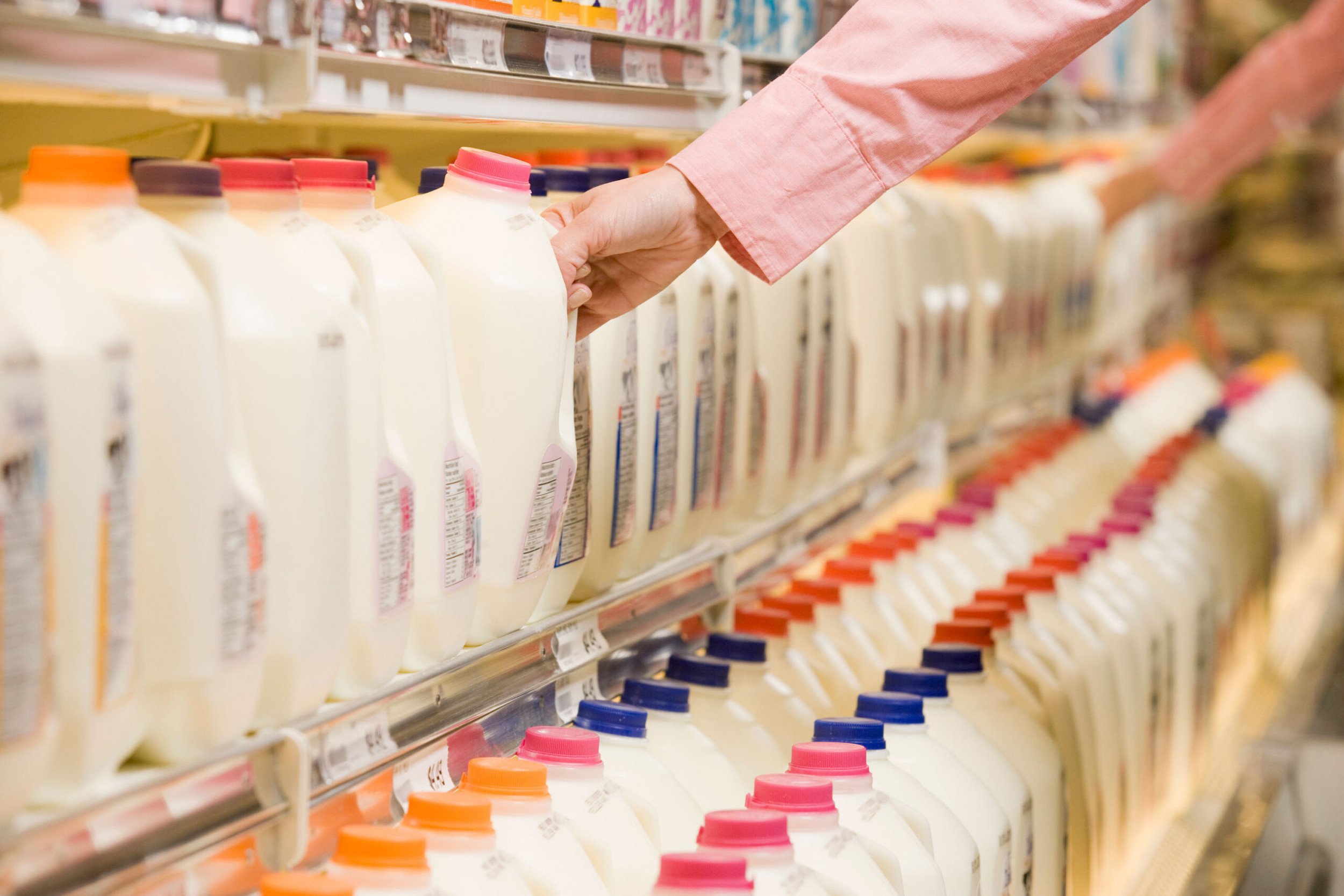