Les Essentiels du processus de scellage
Le système standard consiste de deux composants principaux; l'alimentation électrique et la tête de scellage. L'électricité est un générateur électrique qui opère sur medium et hautes fréquences. La tête de scellage est un étui en plastique oû se trouve un conducteur façonné en bobine. Une fois activée par l'alimentation électrique, la tête de scellage produit un courant électromagnétique (le courant de Foucault). Une fois encapsulées, les bouteilles passent à travers ce courant et c’est à ce moment que la membrane de feuille d’aluminium de l’opercule produit de la résistance électrique qui chauffe la membrane qui à son tour fait fondre l’enduit de polymère de l’opercule. La chaleur conjointement avec la pression émise par le bouchon, fait lier l’opercule à la lèvre du récipient. Un joint hermétique est ainsi crée.
La force de l'alimentation électrique dépend de la taille de la fermeture et de la vitesse de la chaîne de production. Le modèle de la tête de scellage dépend de l'application. Les formes les plus utilisées sont les modèles « tête plate » et modèle « tête tunnel ». Modèle tête plate disperse le champ magnétique à travers une superficie plus large, permettant de sceller un secteur plus avantageux. Modèle tête de tunnel fait concentrer le champ magnétique autour des côtés et au-dessus de la zone du bouchon. Les joints produits sont beaucoup plus hermétiques car ces modèles fournissent un champ électromagnétique plus uniforme.
L'opercule choisi dépend également de l'application. De plus, il existe plusieurs combinaisons de matériaux disponibles pour la fabrication des opercules y compris les membranes de feuille d’aluminium avec doublure intérieure de caoutchouc mousse ou de papier. Les opercules peuvent également inclure des logos choisis par le client, marques déposées, ou d'autres messages, tels que "scellé pour la fraîcheur." Aux circonstances où la membrane de l’opercule se compose de deux couches, la membrane de feuille d’aluminium chauffée, fait fondre également la couche de cire. La cire est absorbée par la membrane en carton de pâte de l’opercule de ce fait libérant la membrane de feuille d’aluminium du panneau de pulpe.
En certains cas, les opercules sont très forts et il faut qu’ils soient brisés afin d’avoir accès au contenu du récipient. Dans d’autres cas les opercules sont facilement décollés. L’opercule qui convient mieux à votre produit dépend de plusieurs variables. Pour trouver le bon opercule, nous vous recommandons de consulter votre fournisseur de bouchons ou les fabricants mêmes des opercules.
Il est plus facile de sceller les récipients en plastique aux capsules en plastique à vis, que de sceller les autres genres d’application ou il faut - par fois - plus de temps afin de réussir. Il est également possible de sceller les récipients en verre et de les faire sceller avec des capsules en métal. De toute façon, ces deux applications posent des défis. Il se pourrait que les récipients en verre devraient être traités afin que la lèvre du récipient puisse être scellée. Bien qu’il soit possible au point de vue technique, le thermoscellage par induction utilisant des capsules en métal exige certaines considérations. Le thermoscelleur chauffera la membrane de feuille d’aluminium de l’opercule et la capsule en métal. Ceci présentera un problème de sûreté possible car la capsule prendra du temps à refroidir. En effet, la chaleur des capsules métals chaufées pourra également fondre les fils en plastique d'un récipient.
Les Nouvelles Téchnologies
Les thermoscelleurs produisent de la chaleur, et les fabricants les ont traditionnellement refroidis à l'eau. Dans les 5 dernières années, le refroidissement à l’air est devenue la solution préférée grâce aux améliorations dans le domaine de la technologie de l’alimentation électrique. Actuellement, les générateurs électriques refroidis à l'air sont en mesure de fonctionner aux vitesses qui, autre fois, n’étaient possibles qu’avec les générateurs électriques refroidis à l'eau. En outre, les générateurs électriques refroidis à l'air sont moins onéreux que ses équivalents refroidis à l'eau et ils ne présentent pas la difficulté de maintenir un système de recyclage d'eau. La gamme d’application à la quelle les systèmes refroidis à l'air peuvent répondre est plus étendue que celle des systèmes refroidis à l'eau.
Le thermoscellage sans aide de capsule, est une innovation assez récente. Normalement, il faut de la chaleur ainsi que la pression exerçée par les capsules pour dérouler le processus de scellage afin de souder l’opercule à la lèvre du récipient. S’il n y a pas de capsule, il faut trouver un autre moyen de créer de la pression. Certains systèmes utilisent une ceinture aérienne pour appliquer la pression et certains utilisent des méthodes pneumatiques.
Pour conclure, il existe des kits de conversion pour changer des systèmes de scellage de conduction en systèmes de thermoscellage. Ayant la capacité de se mettre en marche de manière spontanée, de fonctionner à des vitesses plus élevées, économique et d’exiger moins d'entretien; les systèmes de thermoscellage sont plus efficaces que leurs équivalents de conduction.
Choisir le meilleur scelleur
La taille et le style de la capsule ainsi que la vitesse de la chaîne de production représentent les trois facteurs principaux à considérer au moment de choisir un thermoscelleur. Il est également important de prendre en considération le style et la composition du récipient, la composition de l’opercule et les propriétés du produit lui-même. Comme mentionné précédemment, l’encapsulage des bouteilles en plastique aux capsules en plastique est le processus le plus facile.
En général il est conçu qu’il un rapport entre le niveau de l’alimentation électrique en terme de kilowatt et sa possibilité de sceller, ceci n’est pas correcte. Bien qu'il soit généralement accepté que la puissance du système dépend du taux de kilowatt, un niveau élevé de kilowatts ne mène pas nécessairement à un taux plus élevé de scellage. Le taux de kilowatt fait partie d’une équation plus compliquée. Le transfert d’énergie du générateur électrique à la tête de scellage représente la secret du succès pour créer un system de scellage rapide, efficace et constant.
Les têtes de scellage sont toutes différentes; concevoir une bobine d’induction pour chaque tête de scellage est un art ainsi qu’une science. Si le modèle de la bobine lui-même n’est pas correct, l’augmentation de l'alimentation électrique ne résultera qu’en pertes d’énergie et cela n’améliorera ni la qualité, ni le taux de scellage à un niveau exceptionel.
Les fournisseurs réputés est bien connus, souligneront l’importance de la performance du processus de scellage et de l'efficacité du système plutôt que les taux de kilowatt du système. Nous avons vu beaucoup de thermoscelleurs doués à 1 ou à 2 kilowatts qui ont surpassés des systèmes avec des taux de kilowatt plus élevés. Ne vous fiez pas aux fournisseurs qui proclament que l’efficacité du processus de thermoscellage dépend du niveau de kilowatt disponible ; ce n'est simplement pas le cas.
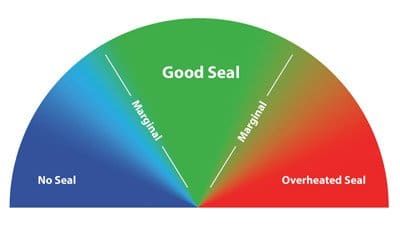