処理の基礎知識
なぜ必要なのか
ポリマーフィルムやその他のポリマー基材は化学的に不活性で非透過性の表面を持ち、表面張力も低く、印刷、インク、コーティング、ラミネートに対する接着受容力が極めて低い性質を持っています。
処理済みのフィルム(製造段階で表面処理が行われているフィルム)は強い表面エネルギーを持つため、印刷、コーティング、またはラミネート製品には欠かせません。
製造段階で表面処理が行われていないフィルムは、印刷、コーティング、またはラミネートを効果的に受容せず、以後の段階で印刷、コーティング、またはラミネートが容易に達成できる保証はありません。
それぞれのフィルムには表面エネルギー(ダインレベル)の特性があり、これは製造段階におけるコロナ処理で上昇させることができます。この処理のレベルは時間が経つにつれ失われていきます。製造直後では印刷やコーティングが容易であっても、数日後あるいは数週間後には表面エネルギーを失い、印刷やコーティングが不可能となってしまうのです。
フィルムを常に限られた時間内に加工するのは極めて困難なので、多くの場合インラインでの再処理が必要となります。ここで注意が必要なのは、インラインでの処理は製造段階での初期処理そのものの代わりにはならないということです。ポリオレフィン系樹脂(ポリエチレンとポリプロプレンなど)を筆頭とした多くのフィルムは、製造直後以外は処理が不可能に近いといえます。
製造段階で処理されたフィルムを使用し、インラインで再処理を加えることで、均等な品質を保つことができます。加工業者そして消費者に満足のいく品質を維持するためには、コロナ処理を二度行うことが推奨されます。
- 製造段階での処理
- 加工前の処理
表面処理の仕組み
コロナ処理システムは、プラズマフィルム、フォイル、または紙の表面エネルギーを上昇させ、インク、コーティング、または接着剤の濡れ性と接着性を向上させる働きをします。この結果、処理された物体は優れた印刷またはコーティング性能、そしてより強いラミネート力を持つことになります。
コロナ処理システムは、パワーサプライと処理ステーションという二つの重要なコンポーネントで構成されています。
パワーサプライは、標準的な50/60 Hzの電源を高周波電源(通常10~30 kHz)に変換し、処理ステーションに送り出します。
処理ステーションはこの電力を、二つの高電位電極、そして基材を固定するグラウンド電位のロールから、エアーギャップを通して基材の表面に送ります。基材の表面張力は、高電位の電極に面した側のみ上昇します。(基材の裏側に行われる処理はバックサイド処理と呼ばれます)
コロナ処理システムの仕組みは、簡単にいうとコンデンサーに例えることができます。コロナ処理システムの場合、トッププレートの代わりに電極に電圧が送られることになります。同様に、コンデンサーでいう誘電体の部分が、コロナ処理システムのロールカバー、エアー、または基材となるわけです。
ボトムプレートは、コロナシステムでは電気的にグラウンドされたロールとして存在します。コロナ処理システムの場合、電圧の上昇がエアーギャップにあるエアーを電離しイオン化することでコロナ放電が発生し、グラウンドロール上を通過する基材の表面張力が上昇します。
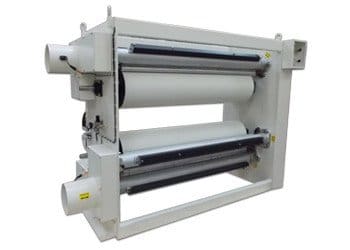