필요한 이유
폴리머 필름과 물체는 화학적으로 비활성이며 표면 장력이 낮은 비다공성 표면을 가지므로 기판, 인쇄 잉크, 코팅 및 접착제와의 접합을 잘 수용하지 못하게 만듭니다.
사전 처리된 필름, 즉 생산 당시 표면 처리된 필름은 고품질 인쇄, 코팅 또는 라이네이션 제품을 생산하는 데 중요한 요소인 높은 표면 에너지를 갖습니다.
생산 시점에 처리되지 않은 필름은 인쇄, 코팅 또는 라미네이션 웰을 허용하지 않습니다. 단, 그 반대의 경우도 동일하게 적용되지는 않습니다. 필름이 생산 시점에 처리된 경우에도 향후에 항상 쉽게 인쇄, 코팅 또는 라미네이팅된다고 보증할 수는 없습니다.
각 필름 유형은 생산 시점에 코로나 처리를 통해 늘릴 수 있는 고유의 표면 에너지(다인 레벨)를 가집니다. 이 처리 레벨은 시간에 따라 감소합니다. 따라서 생산 후 즉시 또는 며칠 혹은 몇 주 이내에 쉽게 인쇄 및 코팅할 수 있는 필름은 인쇄 및 코팅이 불가능해질 정도로 에너지를 잃을 수 있습니다.
수령하는 필름이 필요한 시간 내에 변환된다는 보증은 거의 할 수가 없으므로 종종 인라인 재처리가 필요합니다. 인라인 처리가 생산 시점의 기본 처리를 대체할 수는 없다는 사실에 유의하십시오. 실제, 많은 필름, 특히 폴리오레핀(폴리에틸렌 및 폴리프로필렌)은 생산 후 세팅 시 거의 처리가 불가능합니다.
일관된 품질을 보증하기 위해, 생산 시점에 처리된 필름을 사용하고 인라인 재처리를 하는 것이 좋습니다. 항상 제품 품질을 우수한 상태로 유지하려면 다음과 같이 기판을 두 번 코로나 처리해야 합니다.
- 생산 시.
- 컨버팅 전.
표면 처리의 작동 원리
코로나 처리 시스템은 향상된 잉크, 코팅 및 접착제의 습식성과 부착성을 제공하도록 플라스틱 필름, 포일 및 종이의 표면 에너지를 증가시키도록 설계되었습니다. 따라서 처리된 재료가 입증된 인쇄 및 코팅 품질과 강력한 라미네이션 세기를 제공합니다.
코로나 처리 시스템은 크게 전력 공급 장치와 처리기 스테이션의 두 요소로 구성됩니다.
전력 공급 장치는 표준 50/60 Hz 유틸리티 전기 전력을 받아서 단상 고주파(보통 10 - 30 kHz) 전력으로 변환하며, 이 전력이 처리기 스테이션에 공급됩니다.
처리기 스테이션은 높은 전위차의 전자 쌍과 재료를 지원하는 접지 전위차의 롤을 통해 이 전력을 에어 갭을 통과하여 재료 표면에 공급합니다. 높은 전위차의 전자에 면하는 재료의 면만 표면 장력이 증가합니다. (재료의 다른 면이 처리되는 경우 이를 백사이드 처리라고 합니다.)
가장 단순한 형태의 코로나 처리 시스템은 커패시터를 들 수 있습니다. 코로나 처리 시스템의 경우 상단 플레이트에 전압이 가해집니다. 커패시터의 유전체 부분은 몇몇 유형의 롤 컨버팅, 공기 및 코로나 처리기의 기판으로 구성됩니다.
최종 구성 요소 또는 하단 플레이트는 전기적으로 접지된 롤 형태를 가집니다. 코로나 처리 시스템에서 전압 축적으로 에어 갭의 공기가 이온화되어 기판의 표면 장력을 늘려 전기적으로 접지된 롤을 통과하는 코로나를 형성합니다.
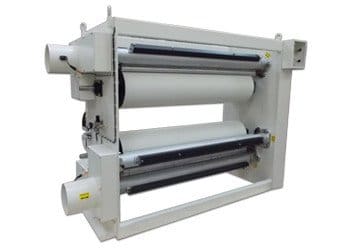