UV Flexo Ink Composition And Surface Treatment Effects On Adhesion To Flexible Packaging
Read the abstract below and download your copy of this informative technical paper which was presented at the TAPPI PLACE 2010 conference “UV Flexo Ink Composition and Surface Treatment effects on adhesion to Flexible Packaging”.
Abstract
UV flexo inks are becoming increasingly popular in flexible packaging and shrink sleeve applications, traditional markets for flexographic inks. The ever-increasing improvements in UV flexo inks such as print quality, low ink maintenance requirements, no solvents, high press stability, and in-line finishing have all contributed to converters’ decisions to switch to UV flexo system. Recently, new UV flexo ink systems have improved efficiency and production speeds to greater than 250 meters/minute. However, variables such as resin selection, amount of ink applied, substrate absorbency, UV curing conditions and print speed can all propagate episodes of erratic adhesion on difficult substrates. Hence, many substrates are coated with a primer to perform as adhesion promoter. Nevertheless, this additional coating are not always successful, increase cost to the convertor and typically do not mitigate the migrating effect of lubricating additives found within certain flexible packaging films. This paper will detail, in the absence of adhesion promoters, the effects of corona, flame or atmospheric plasma surface treatments on the adhesion of UV flexo inks to flexible packaging films.
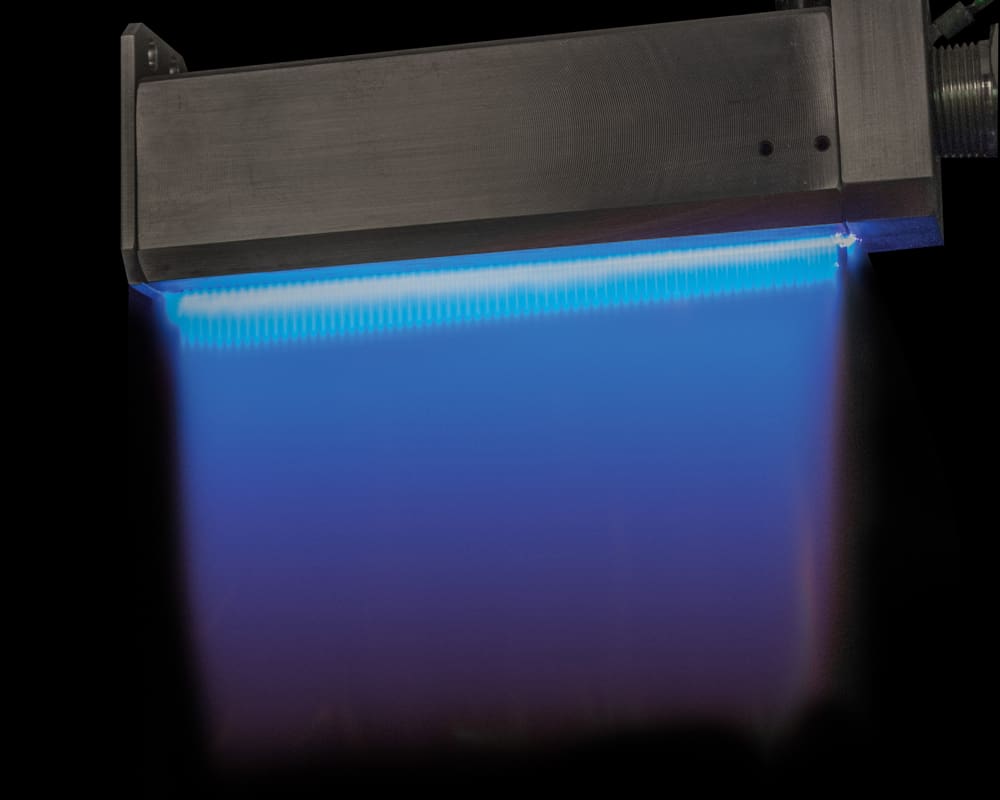