New Blown-ion™ 500 Plasma Surface Treating Technology Enables Rockwell Automation’s Switch from Print-and-Apply Labels to In-Line Digital Printing
When Rockwell Automation moved its contactor and relay production back to Milwaukee, Wisconsin, it had to develop an entirely new process for the changing volumes and available space. The new highly automated assembly line would also be a showcase of Rockwell’s automation capabilities, featuring Rockwell drives, motors, Independent Cart Technology (ICT), PLC’s, HMI’s, sensors, and software, just about everything Rockwell produces.
Rockwell also wanted to make improvements on the product decorating as part of the new process. The components are marked on the top and side requiring multiple colors, many variations, and variable data. Rockwell had used multiple technologies to do this prior; print-and-apply labels, continuous inkjet, and pad printing. “We believed we could further improve line efficiencies and flexibility by switching to in-line direct printing,” says Troy Gueller, Senior Project Engineer, Rockwell Automation. Troy served as the project’s lead for technology and equipment.

The company worked with Engineered Printing Solutions (EPS) of East Dorset, Vermont for a solution to print on the parts made from PA66 plastic. Samples were printed using EPS’ single-pass digital ink jet technology; however, the ink did not adhere well enough. The reason for this is because PA66 has an inherently low surface energy. EPS recommended an in-line surface treating technology be employed to raise the surface energy to the needed levels for proper ink adhesion. Flame and blown-ion plasma technologies were considered for the application. At first, flame had an advantage over blown-ion plasma because the areas that required treatment would require several Blown-ion™ 125 treatment heads and space on the line was at a premium.
Implementing New Plasma Technology
During this investigation process, Rockwell engineers met with Enercon Industries Corporation (Menomonee Falls, Wisconsin) at a trade show and learned of a new technology the company had just developed which combined the capabilities of six Blown-ion™ 125 treatment heads into a single enclosure controlled by a single power supply.
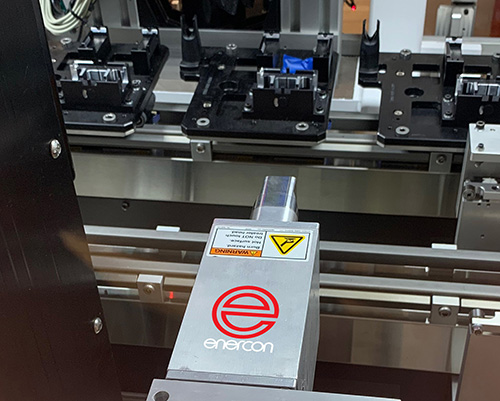
Enercon’s new Blown-ion™ 500 plasma treater utilizes a MultiPort™ design that bombards surfaces with an intense, high-speed discharge of ions to clean, etch and functionalize surfaces. Treatment removes contaminants, increases bonding sites, and improves the wettability of plastics, composites and metal surfaces for improved adhesion. It is ideal for high-speed applications requiring up to two inches of treatment coverage in a single pass.
Lab trials were conducted, and the treated surface enabled indelible bonding with the ink. After UV curing, the parts passed testing meeting all industry marking standards. Bret Kohler, Senior Regional Manufacturing Engineer, Rockwell Automation, who is responsible for continuous improvement projects, says, “Enercon’s design that integrates six plasma treating nozzles into a single head was a huge benefit for us. The system was also easy to integrate through the system’s network communication capabilities.”
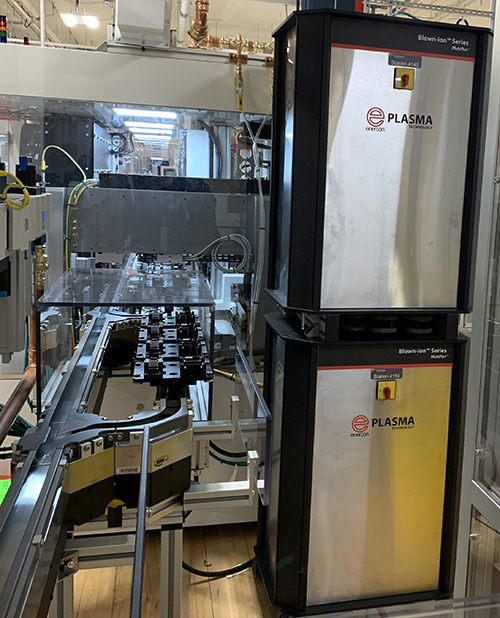
The treater offers network communication through Modbus TCP, with the ability for remote control and monitoring of stop/start, priming, and on-and-off air flow, all with closed‑loop feedback. The system also uses artificial intelligence for troubleshooting and includes a USB available for downloading data and updating software.
The marking process ultimately developed by Rockwell, EPS, and Enercon, utilized an Enercon Blown-ion™ 500 plasma treatment system, for the top prior to printing. Further assembly is completed. Finally, the side is presented to a second Blown-ion™ 500 for treatment prior to the remaining printing. The entire process is completed in under four seconds.
Optimizing Line Performance
Integrating new technologies and processes can be challenging, and the two companies worked very closely together to identify areas for improvement. For example, initially the installation was completed without an exhaust system. However, it was determined that byproducts from the plasma treatment had an adverse effect on nearby communication cables and tubing, causing them to become brittle and require replacement. Likewise, the buildup of ambient heat from the process stressed the components of the treater head. An exhaust system was subsequently added to vent the nitrogen dioxide and other byproducts from the assembly line.
The Blown-ion™ 500 technology is truly a barrier breaker as the first of its kind to enable blown-ion plasma to cover such wide areas in a single pass. As such, the companies worked extensively together in running samples in the Enercon lab and then implementing design changes on the assembly line. The improvements made during this live development process led to modifications of the Blown-ion™ 500 treatment head design. “With feedback from Rockwell we were able to make additional improvements in materials and design of the treatment head which led to a larger operating window and durability which will benefit all future users of this new technology,” says Enercon’s Engineering Lab Manager Dave Hebel.
Bret concludes, “Enercon really went out of their way to resolve any concerns we had and ensured we always had spares. It’s all been worth it. The continued improvements have resulted in a robust and capable piece of equipment that operates reliably for us every day.”