Automotive Manufacturer Reduces Warranty Claims with Plasma Treating (Video Included)
A major automotive manufacturer is reaping the benefits of reduced warranty claims by implementing plasma treating into their adhesive bonding operations. This specific application is for creating a Formed-in-Place Gasket (FIPG). FIPG is a process that creates a seal between two surfaces by applying a liquid sealant between them.
The quality of the adhesive bond is dependent on the optimization of the surface. Low surface energy, surface oils and surface contamination will prevent a perfect bond. The traditional method of surface preparation is wiping with a parts cleaner such as alcohol or acetone, however this technique has known limitations.
- Difficult to be sustained in all types of work cells.
- Repetitive human actions are rarely a reliable process.
- Slow
- Error Prone
- Some organic contaminates do not improve even after cleaning with parts cleaner.
With a goal of zero leakage, FIPG gasketing is a mission critical operation. This is where Blown-ion™ plasma treatment comes into play. Plasma technology cleans, etches and functionalizes surfaces to remove contamination and oils while increasing surface energy. The results are impressive. Adhesion with plasma treated surfaces is greatly improved with evidence of cohesive fracture rather than interfacial peeling.
Most importantly, the warranty rate for oil leaks when using this technology has been dramatically reduced as shown in the chart below.

Implementing Plasma Treating in the Work Cell
For these applications, Blown-ion™ plasma treaters are most often implemented within the same work cell that the adhesive is applied. The treatment heads use the same robotics as the adhesive dispensing unit, following a precise path to optimize throughput and efficiency.
As previously mentioned, cleaning practices can be difficult to sustain over a variety of applications, due to part size and geometry, as well as speed and work cell design. This is why Enercon has developed multiple plasma discharge technologies to meet the needs of demanding applications. The original Blown-ion™ 125 provides a concentrated plasma treatment up to a half inch in a single pass. A variation of this system provides an angled treatment head to apply treatment to more difficult to reach surfaces. And for wider applications, an Enercon Blown-ion™ 500 Plasma Treater can treat a width of 2 inches in a single pass. Watch all three in action in this video.
To determine if plasma treating may be a solution for your bonding application, Enercon offers free lab testing of all of our plasma and flame treating technologies, as well as in-field trials. Contact our experts today to see what surface treating can do for you.
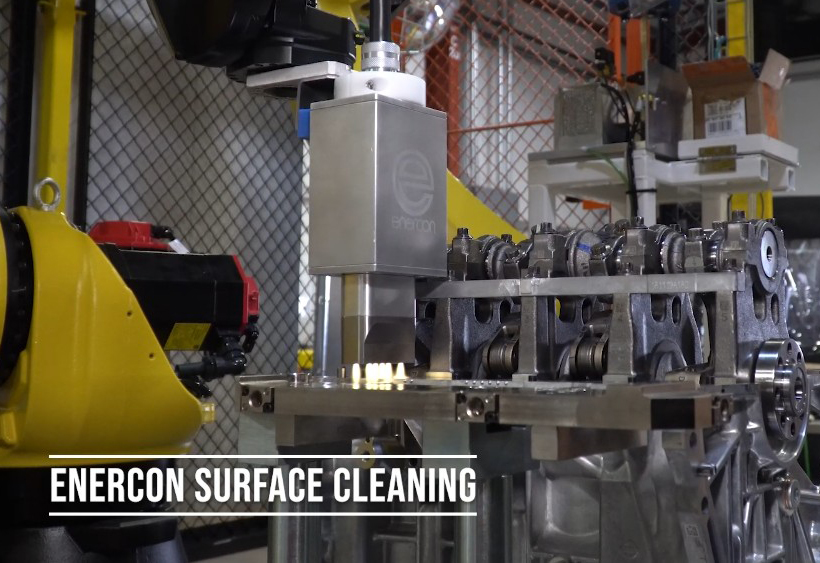