Automation Improves Plasma & Flame Surface Treatment Productivity
The manufacturing of virtually everything from toothbrushes to auto parts can benefit from the use of atmospheric plasma treatment and flame treatment during assembly and decorating operations. These technologies increase material surface energy to promote bonding with inks, adhesives, paints and other coatings. Companies in the medical, automotive, packaging, consumer products, wire & cable, sporting goods, furniture, and others markets find that surface treatment improves bond strength, increases throughput, and can also reduce costs.
In many cases, material handling and automation of the surface treatment process is required to achieve productivity goals. Enercon partners with specialty equipment integrators for their automation expertise. One company Enercon has partnered with on several applications is Midwest Engineered Systems Group (Pewaukee, Wis.).
Their Senior Applications Engineer Jerry Schmit says, “Each customer’s requirements are unique to their operation and space available. We’ve had projects where we’ve integrated an Enercon flame treater with a conveyor, and we’ve also constructed entire rooms where parts are transported in, treated and then exit the room for additional processing. Surface treating solutions can be used in virtually any application or industry requiring improved adhesion.”
Discover the variety of applications integrators are using plasma & flame treaters for by accessing these videos and applications articles:
- Video: Flame Treater for Automotive Dashboard
- Video: Air Plasma with Robot
- Video: Flame Treater for Mechatronic Process
- Article: Robotic Plasma Treatment for Headlamp Adhesion
- Article: Air Plasma Pad Printing
Read the full article in Automation World
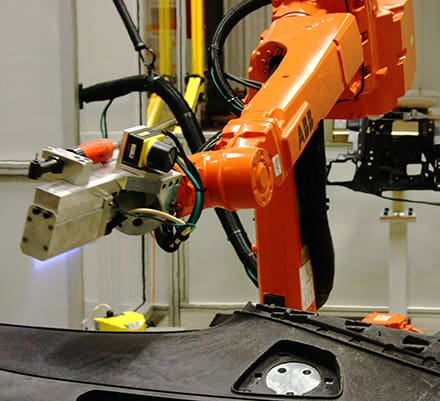