Better Adhesive Bonding Begins with Ensuring Material Surface Energy
Adhesive bonding plays a pivotal role in industrial applications by securing materials efficiently and reliably without the weight of fasteners. However, achieving strong and durable bonds requires more than just choosing the right adhesive—it demands an understanding of surface energy. This critical factor determines how well an adhesive interacts with a material, directly impacting bond strength and performance.
What Is Surface Energy?
Surface energy represents the energy required to increase a material’s wettability, providing an indicator of how easily a surface can interact with adhesives. Most plastics such as polyethylene (PE) and polypropylene (PP) have chemically inert surfaces and low surface energy. And in many cases, plastics have additives that can rise to the surface, further undermining potential adhesion. Materials such as aluminum, steel and glass may have higher surface energy, but surface contamination, including oils, dust and debris, can undermine successful bonding with these surfaces despite their inherent higher surface energy.
The most common method of measuring surface energy on non-porous surfaces is in a unit of measurement called dynes. A dyne is a centimeter-gram-second (CGS) unit of force.1 dyne = 1 gcm/ s2. Surface energy can be measured with dyne pens & dyne solutions. Higher dyne levels indicate higher surface energy. See the chart of common materials and their typical inherent dyne levels.
Alternatively, the Contact Angle (ca) method can be used which measures the angle between a liquid and the surface it comes in contact with. A lower contact angle indicates higher wettability and surface energy.
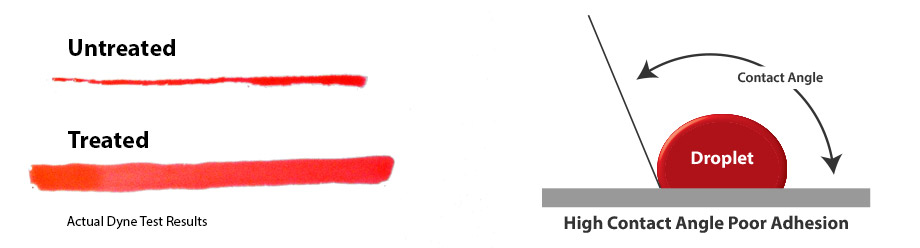
Dyne | Ca | |
PP | >30 | 94.35 |
PE | >30 | 114.9 |
PS | 31 | 91.5 |
PA6 | 34 | 74.21 |
PA66 | 36 | 67.63 |
PET | >30 | 114.9 |
For proper adhesive bonding, industrial adhesive manufacturers will specify a target surface energy for each of their adhesive formulations.
It’s important to understand the role of a material’s surface energy as the foundation for creating reliable bonds in a wide variety of industrial applications found in the automotive, aerospace, assembly, decorating, and packaging markets.
Why Surface Energy Matters in Adhesive Bonding
If you do not provide an adhesive with a surface that conforms to the required surface energy, you will not be able to achieve a robust adhesive bond. When surface energy fails to create a strong bond, the result is not only poor adhesion, but the source of significant problems including short- and long-term quality issues, potential safety hazards, production line downtime, & costly customer returns.
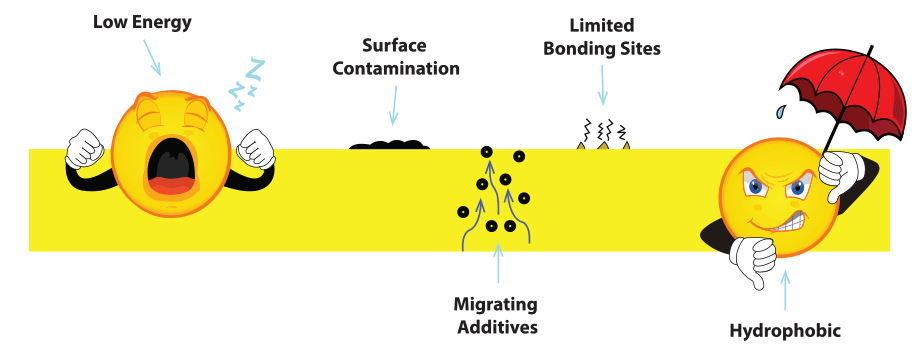
By addressing surface energy issues prior to adhesive bonding, you can prevent these problems and ensure reliable bonding.
Optimizing Adhesive Bonding: Surface Preparation Techniques to Ensure Adequate Surface Energy
Once you’ve identified your surface does not meet the dyne or contact angle specification for the selected adhesive, there are several techniques you can employ to increase your materials’ surface energy.
Chemical Solvent, Alcohol Primers & Etching
Chemical solutions, such as the use of solvents & alcohol-based primers, are surface preparation techniques effective at increasing surface energy and have been used in the industry for many decades. However, there are certain considerations to keep in mind when using these liquid adhesion enablers.
In most cases, these solvents and primers are applied or wiped on by a person. Whenever your goal is to create a repeatable process to ensure quality, and with adhesive bonding that is certainly the case, you want to avoid the potential for human error. First, not all employees will perform the task exactly the same way. Workers also become tired & distracted over time creating inconsistent results when applying solvents and primers. This directly results in inconsistent surface energy, undermining successful adhesive bonding.
Additional concerns with solvents and primers used to promote adhesive bonding are consumable costs and safety. They can be hazardous to humans and the environment. Special care needs to be taken to ensure workers have proper personal protection equipment, and that cleanup and disposal of spilled or residual solvents and primers is satisfactorily completed.
Chemical etching is another process which can be used to prepare surfaces for bonding with adhesives. This process is more expensive than liquid primers and solvents. And it also requires significant resources to ensure proper cleanup and disposal of chemicals used in the process.
Mechanical Surface Preparation
Mechanical surface preparation methods include sandblasting and laser ablation. These techniques are designed to create more surface area for the adhesive to bond with. However, these methods remove a portion of the surface, which may be undesirable.
These methods effectively increase surface energy and wettability for adhesive bonding but have additional considerations. Initial cost of equipment, wear part replacement, speed of treatment and cleanup are significant factors. It should be noted that in most cases prior to attempting bonding with an adhesive, these mechanically prepped surfaces also require a secondary cleaning step, such as a wipe or primer to clean the surface of any debris left by the process.
Vacuum Plasmas
Vacuum plasmas treat surfaces inside a low-pressure chamber. A process gas fills the chamber, and an electrode is used to ionize the gas in the chamber. Parts are treated in batches and are limited to the size of the chamber, which is most typically the size of a microwave oven or smaller. Treatment times vary and may take between 15 minutes and one hour in the chamber to achieve desired results.
These systems are highly effective at increasing surface energy and covering the complete surface of a part. However, dead spaces in the chamber need to be accounted for. To prevent contamination of the parts after treatment, surfaces must be handled carefully until the adhesive is applied to ensure a strong adhesive bond.
Additional considerations for using vacuum plasma equipment to improve surface energy include the relatively high initial investment in capital equipment and the ongoing consumable cost for the process gas.
Atmospheric Plasma, Corona and Flame
Atmospheric plasma cleans, etches and functionalizes surfaces to increase surface energy and improve wettability of surfaces with adhesives. They remove organic contaminants and some inorganic contaminants to prepare surfaces for successful adhesive bonding. Treatment is conducted in atmosphere, so in most cases there are no consumable process gas costs.
In-line air plasma treaters can be part of a production line or a dedicated work cell. Surfaces to be treated can be presented to a fixed plasma treatment head or the treatment head can be integrated with a robot or other means to enable the treatment head to follow a precise treatment pattern on the part. Because they are integrated into a production process, plasma offers reliability and consistency that is not possible with human-dependent priming or surface preparation methods.

Atmospheric plasmas are available as Blown-arc™ plasma, sometimes referred to as corona treatment, Blown-ion™ plasma, or Flame Plasma Treatment. The chart below shares lab data on the effectiveness of Blown-ion™ and Flame Plasma technologies improving the surface energy of a variety of plastic surfaces.
Untreated | Blown-ion | Flame | ||||||||||
Dyne | Ca | Polarity | Sfe | Dyne | Ca | Polarity | Sfe | Dyne | Ca | Polarity | Sfe | |
PP | >30 | 94.35 | 1.55 | 29.62 | 58 | 47.83 | 20.6 | 57.6 | 70 | 38.59 | 9.5 | 44.64 |
PE | >30 | 114.9 | 0.28 | 28.69 | 60 | 45.28 | 21.41 | 59.9 | 56 | 52.22 | 16.94 | 56.34 |
PS | 31 | 91.5 | 0.62 | 41.37 | 70 | 24.75 | 32.37 | 70.48 | 48 | 69.08 | 7.69 | 47.87 |
PA6 | 34 | 74.21 | 6.92 | 41.66 | 66 | 41.81 | 21.89 | 63.5 | 54 | 55.45 | 15.75 | 54.54 |
PA66 | 36 | 67.63 | 8.08 | 49.24 | 70 | 35.79 | 27.67 | 64.57 | 70 | 31.7 | 17.78 | 55.95 |
PET | >30 | 114.9 | 0.28 | 28.69 | 70 | 38.17 | 27.65 | 62.26 | 44 | 80.99 | 5.15 | 35.91 |
When Surface Treatment Becomes Essential
When materials fail to bond well with adhesives, product quality and throughput suffer. Surface preparation methods can be employed to increase surface energy and achieve adhesive bonding success. Low cost in-line surface treatment technologies, such as Enercon’s plasma, corona, and flame treatment, offer efficient and repeatable results to ensure surfaces are optimized for bonding with adhesives for industrial assembly & decorating applications. These pretreatment technologies also streamline processes, reduce waste, and eliminate the need for harsh chemicals.
Enercon application engineers can help you determine if one of these technologies will work for your application. To ensure proper adhesive bonding for your products, they can test and compare corona, flame, and plasma treatments for plastics and other surfaces in their new state-of-the-art lab.
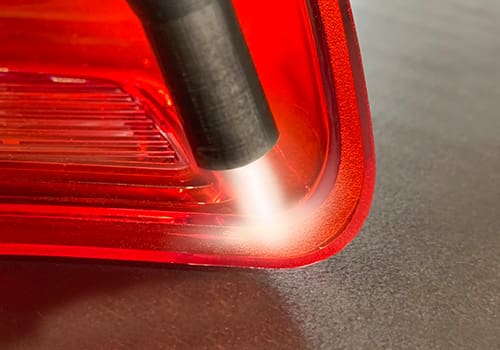