Desmear & Descum Circuit Boards with Plasma Treatment
Complex printed circuit board constructions with ever-increasing layers and circuit densities benefit from Plasma3™ plasma treatment for descum, desmear, removal of carbon-based organics, PTFE activation, and surface preparation.
Plasma processing of various board types historically have used vacuum plasma technologies. However, there is a need for increased processing capacities as the printed circuit board construction continue to increase in intricacy. As a result, vacuum plasma is no longer as cost-effective. Vacuum plasma chambers have also traditionally been labor-intensive resulting in a slower production speed.
Enercon’s Plasma3 offers a roll-to-roll, inline solution at faster processing speeds than vacuum processing. Atmospheric plasma technology is being used to remove the contaminates on the surface of copper and stainless steel layer components of printed circut boards at the molecular level enabling adhesion between the electronic components.
Atmospheric plasma systems remove the residues of contaminants from sensitive surfaces without damaging them to increase yields. Activation of Plasma3™ gas chemistries create a chemical reaction with the surface contaminants, resulting in their volatilization and removal. Plasma3 reduces hazardous material use, waste, air emissions and increases production speed.
By integrating surface treatment into printed circuit board production lines, manufacturers are given an inline continuous solution to cleaning the surface of copper and stainless steel. Atmospheric plasma surface treatment cleans the layer components of printed circuit boards at the molecular level allowing electronic components to attach at the contact between the board and the component.
Pretreatment removes rolling oils and other surface contaminations from aluminum and steel foils that result from slitting and rewinding. This prepares the surface for soldering and brazing, while eliminating the uses of batch chemical process.
In addition to being an in-line, or continuous process, surface treatment also reduces manpower or labor time traditionally involved with cleaning by batch processes and can guarantee the quality of the clean on the first application.
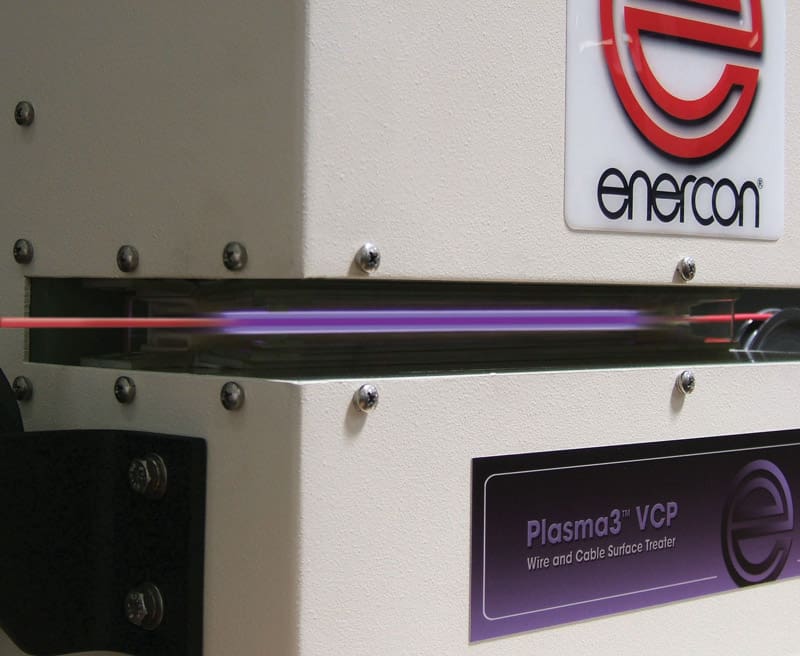