Flame Treater Improves Automotive Leather Adhesion
Robotic flame-treating cells at Eissmann Automotive enhance interior leather components of popular premium vehicles.
While sports cars and high performance vehicles turn heads as they breeze down the street, the real thrill is to be behind the wheel, in the cockpit, feeling the car respond to a subtle turn or touch of the accelerator. For some of the best designed cars, it is a privilege just to sit in the driver’s seat, whether they are moving or not, just to take in the sleek interior features, ergonomically placed controls, and exquisite leather trim.
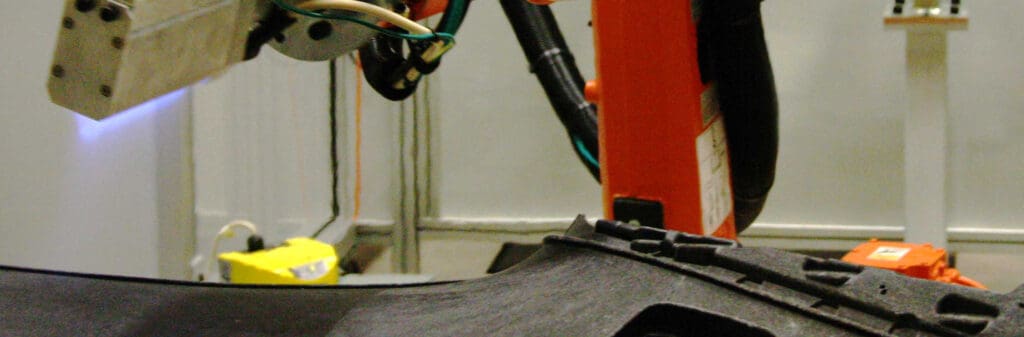
For nearly 50 years, Eissmann Group Automotive has specialized in supplying high-end leather trim and automotive interior components for virtually all the well-known manufacturers in the automotive industry. Through a passion for innovation and a keen eye for detail, their work has made major contributions to the driver and passenger experience in some of the most celebrated vehicles across the globe.
The recent design and installation of a robotic flame-treating cell in Eissmann’s Pell City, Alabama facility is representative of this attention to detail, and the drive to continually improve manufacturing processes.
Eissmann’s core business is to finish any interior components of passenger vehicles that are wrapped in leather, with the exception of seats. This includes glove boxes, door panels, gear shift modules and complete instrument panels (i.e. dashboards). The components vary in size, shape and complexity, many wrapped with padding in addition to leather with other “hard cladding” parts featuring leather attached directly to the substrate frame, often made of polypropylene plastic.
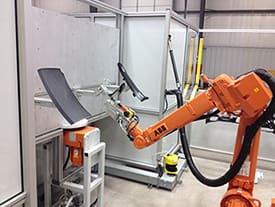
While the polypropylene substrate frames provide the perfect balance of strength and low weight that car manufacturers demand, polypropylene and other plastics can be difficult materials to adhere things to without some sort of surface preparation.
Surface Treatment increases surface energy for better adhesion
Treating plastics with either atmospheric plasma or flame treatment is known as an effective means of cleaning and functionalizing a surface to enhance its ability to form strong bonds with an adhesive. Treatment oxidizes the surface, creates a high surface energy and increases potential bonding sites. Applying the adhesive soon after treatment is a best practice, as treatment will decay over time. In this application, the treatment easily lasts longer than the one production shift required before the padding or leather needs to be adhered.
Eissmann had been applying the heat manually with a propane torch, or by passing the parts under a stationary flame-treating unit. The process worked well for the basic components, but became cumbersome and time consuming as the components got to be larger and more complex.
“We began to get more full instrument panels, which are larger and more intricate than some of the other interior parts we were handling,” said Barrett White, the Eissmann manufacturing engineer in Pell City with responsibility for the interior trim finishing lines. “The manual flame-treating process became difficult because the large parts are harder to maneuver and they typically have a lot of undulations and openings that need to be treated.”
Collaborative Design
Early in 2012, White and the Eissmann production team, looking for a better way, consulted with two partners with whom they had worked in the past: Fitz-Thors Engineering in Bessemer, Alabama, a designer of manufacturing automation systems and a certified ABB Robotics value provider; and Enercon Industries of Menomonee Falls, Wisconsin, a manufacturer of surface treatment systems.
Early in the specification and design process, as a range of concepts were reviewed, the one constant that emerged was that the core component of the new system would be a 6-axis robot with a flame burner attached to the end of the arm. The robot would be able to provide the motion needed for the burner to access all areas on the component substrates, flexibility to handle different parts with a push of a button, and speed to keep up with the growing production demands.
“With the variety of interior components that Eissmann produces, and their increasing size and complexity, I was convinced that an industrial robot was the right solution,” said Arnar Thors, Fitz-Thors co-founder and partner. “The most challenging design work came in identifying and refining the most efficient configuration for the robotic cell.”
While robotic flame treating cells are fairly common, most feature a closed-cell design, where the robot treats one or more parts in a batch; and the robot is dormant while the cell is opened, and finished parts are removed and new parts are staged. Since the actual flame treating of a part takes approximately 10 seconds, with a closed cell, the robot may be inactive far more than it is active. Eissmann needed a cell that kept the robot continually working.
The four-station, open-cell concept
Through ABB’s RobotStudio simulation software, Fitz-Thors and Eissmann experimented with variations on the closed-cell design, none of which resulted in significant throughput improvements. Frustrations rose and the innovative talent took over. The slate was wiped clean, and after several additional design iterations, a unique, four-quadrant station, open-cell concept was developed that met the necessary criteria.
Rather than bringing the parts to the robot, the robot goes to the parts, from a central, fixed base inside the cell. One of the stations has a turntable that is able to hold three different fixtures on each side, allowing the station to process six different interior components. The turntable allows a part to be loaded, while the fixture on the other side is holding a part in queue for the robot to approach for treatment. The other three stations each have a rigid fixture that holds one, especially large instrument panel component.
Depending on the part volume, one to three operators load and unload parts at each station. Once a part is loaded, the operator pushes a button to signify the part is ready. The robot arm moves to the various stations in the order in which the parts are loaded, staying in constant motion. When an operator is loading a part on a fixture, he is considered to be in the cell. The robot can be working on a part in another quadrant at this time.
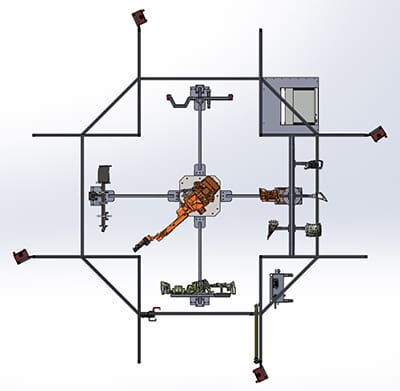
Once the polypropylene substrates are flame treated, they are hung on a rack and routed to the adjacent glue spray booth, and then on to be wrapped with either padding or leather. Though the access to the robot has been greatly increased from the closed cell design, the open cell is just as safe. Once the operator hits the start button, he cannot go back in that quadrant of the cell.
ABB SafeMove technology, a software and electronics based safety system integrated in the robot controller, provides three integrated levels of robot motion safety in the cell. While the operator is able to work within a safe proximity to the robot, safety light curtains restrict the motion of the robot in a loading area while occupied by an operator, and two safety scanners stop the robot completely if an operator enters the interior area of the cell itself.
“The Eissmann concept came together quickly, once we broke away from the limitations of the closed cell design,” said Thors. “The four-station configuration maximizes the utilization of the robot, leveraging its reach and agility to move from one cell to the next throughout the day, rarely sitting idle.”
An agile 6-axis robot with Integrated Dressing
The robot is an ABB IRB 2600ID, featuring a unique combination of high payload, large working range and Integrated Dressing (ID), which routes the compressed air, electrical and natural gas hoses that run the flame burner inside the robot’s upper arm and wrist. With the internally routed dress pack, the movement of the hoses and cables is completely predictable, allowing the robot to operate at maximum speeds and simplifying off-line programming.
The ABB robot controller also features ABB’s MultiMove™ software, which independently coordinates the motion of the robot and turntable in cell one, allowing the turntable to move while the robot is working at another station, monitoring the movements of both to avoid a collision.
“Fitz-Thors made the recommendation to go with the ABB, not just because of the robot itself, but also for the ease of programming and the superior technical support,” said White. “We now have another ABB robot that handles an air bag scoring function, and recently took delivery of a second flame-treating cell, which also has an IRB 2600ID.”
High velocity flame burner
The Enercon 226 Series Burner is especially designed for robotic use, with robotic-rated hoses and a specialty head that produces a high-velocity flame curtain that does not curl with quick movements. A curled flame typically misses some of the intended coverage areas, diminishing the effectiveness of the treatment process. The Enercon system also allows the flame to be applied “atmospherically,” meaning the cell can be placed within the standard production line rather than off in a remote corner.
“The flame needs to treat line of sight, so when working with automotive parts that are very complex, and not just on an X-Y flat area, the flame needs to be turned to get into its various nooks and crannies,” said Sarah Bauer, the Enercon sales specialist who worked with Eissmann and Fitz-Thors in developing the cell. “The movement of the 6-axis robot to get to the hard-to-reach areas, and the integrity of the flame to maintain its shape is so important to the success of the parts that Eissmann makes.”
Popular premium vehicles, vision and improved performance
The first cell has been in use since August 2012 and has been treating instrument panel substrates and other dashboard components for the Chevrolet Corvette and the Tesla Model S vehicles, and substrates for the Lincoln Navigator passenger airbags. New components can be added to the cell at any point by simply developing the custom fixture to hold the part, and programming the robot and the fixture to perform the required movements.
The second cell was up and running in Spring 2014 and is used for Mercedes M Class and Ford program instrument panels, and overflow from the initial cell. Eissmann is currently running two shifts, five days a week.
Both cells also feature a Cognex vision system attached to the robot arm to enhance the cell’s current and future capabilities. The camera is currently used to identify if a tab is still on the Corvette instrument panel is still in place, which, if it is, means the airbag compartment on the part has not been properly processed by the manufacturer, and the part is discarded. This critical double check was requested by the Corvette team, and with the vision system in place, Eissmann was able to comply. A secondary use of the camera is to verify that the substrates are secured properly to the fixture.
“The cell has worked very well for us. It took two minutes on average to treat each part manually, and now it takes about 10 seconds with the robot,” said White. “The tolerance with the robot is 0.02mm, which results in incredibly consistent coverage and far better adhesion. We put a lot of thought into developing this system and it has certainly paid off.”
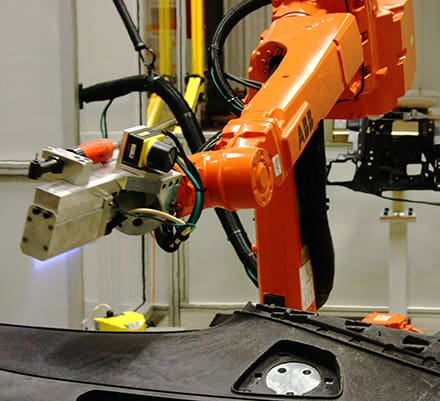