Plasma and Flame Surface Treating Enable Automotive Adhesive Bonds
TA Systems of Rochester Hills, Michigan, specializes in engineering custom automation solutions for the automotive industry. Their customers rely on them to integrate multiple technologies and processes into efficient manufacturing cells. Recently, there has been an increase in requirements for integrated in-line surface treating to improve adhesive bonding on a variety of plastics. While at the NPE trade exhibition, TA Systems forged a partnership with Enercon Industries Corporation. Together, the companies have worked on numerous projects with flame and plasma surface treatment systems integrated along with robotics and adhesive dispensing equipment.
The first of many projects the companies have worked on together involved adhesive bonding of instrument panels. That application required flame treatment and VP of Sales, Bob McQueen, said TA Systems is impressed with Enercon’s mass airflow technology. “We were in the market for a new flame treatment partner and what we found with Enercon’s combustion control technology made a huge difference,” says McQueen.
Enercon’s mass flow control systems measure both the air and gas volume being fed to the burner and compensates for changes in temperature and atmospheric pressure for the most accurate and repeatable flame chemistry. It is a closed-loop system that automatically adjusts both air and gas flow based on values input by the user of air flow rate and air/gas ratio.
McQueen adds, “The Enercon flame treater design provided more consistency, was very safe, and more precise than any other system we had used before.”
Spoiler Alert: Plasma Treater Ensures Epoxy Bond
TA Systems earned an integration project for Magna in South Carolina for an Automotive OEM in Germany. The project required surface treatment, but in this case, in-line atmospheric plasma was desirable. Since Enercon offers both flame and plasma surface treating technologies, TA Systems chose Enercon as the surface treating supplier for the assembly process of a two-piece spoiler plate.
Steve Daugherty, VP Program Management for TA Systems says, “Our projects with Enercon have gone very smoothly. The technology is great, they deliver on time and the support is there when we need it.”
“As automotive manufacturers continue to look at ways to improve performance, surface treating will be an important technology to enable economical structural bonding that might otherwise be impossible.”
Bob McQueen, VP of Sales, TA Systems
This particular application required material handling, robotic integration of plasma treatment and adhesive dispensing, infrared heating and mechanical pressure to secure the parts in place as the adhesive cures. Required cycle time for the process is three minutes and thirty seconds.
Each piece of the spoiler is approximately 42” wide by 9” deep and ½” thick. The materials are Poly Carbonate (PC) plus Acrylonitrile Butadiene Styrene (ABS) and PC plus Acrylonitrile Styrene Acrylate (ASA). These materials provide dimensional stability, low moisture absorption, heat resistance, creep resistance and toughness in cold temperatures.
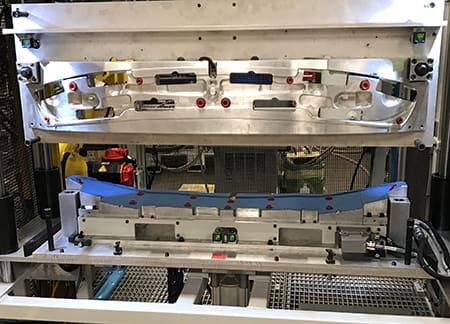
A two-part structural epoxy from Sika is used for bonding, but the low surface energy of the plastic prevents sufficient bonding without surface treatment. Enercon’s Blown Ion Plasma Technology is used to clean, etch and functionalize the surface to enable adhesion.
Blown Ion plasma treaters push pressurized air past an electrode that discharges inside the treatment head chamber. Inside the chamber, energized electrons create positively-charged ions. Air pressure forces the ions to accelerate and stream out of the tip of the head at high velocity towards the plastic surface. These ions positively charge the object’s surface, increasing its surface energy and making it more receptive to the adhesive.
A Fanuc M20 robot is programmed to have the treatment head of the Treater follow a precise path around the inside perimeter of both parts of the spoiler. The Enercon Treater’s operation is controlled by a PLC programmed by TA Systems. Next, a Grayco adhesive dispensing head is pneumatically actuated into position and follows the same path as the plasma treater via the Fanuc M20 robot.
The parts are brought together and held firmly in place while the bond is created. The pressure is required as the plastics are subject to some warping and cannot be allowed to relax back to their natural state. To achieve green strength, the adhesive requires time to cure. At ambient temperatures this can take 10-12 minutes. With a cycle time goal of less than four minutes, it was important to accelerate this process.
TA Systems incorporated an infrared heating system to raise the temperature to 200-220 degrees Fahrenheit. This reduced the cure time to three minutes. To save additional time, the work cell has an area where the operator can load the next pieces while the process is being completed.
McQueen says, “As automotive manufacturers continue to look at ways to improve performance, surface treating will be an important technology to enable economical structural bonding that might otherwise be impossible.”
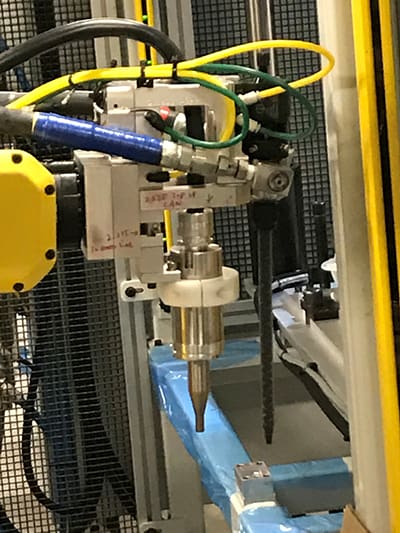