Plasma Treater Improves Inkjet Printing Throughput
For over sixty years, WAGO has been at the forefront of streamlining electrical connections with innovative products like CAGE CLAMP® and in turn providing their customers with the highest standards of usability, safety and efficiency. The international company’s Germantown, Wisconsin operation recently streamlined their custom printing operations by adding an in-line atmospheric plasma surface treating system.
WAGO Manufacturing Manager Jerry Jordan says the company was looking for ways to improve the efficiencies and ink adhesion for printing on their Nylon66 terminal blocks. “Prior to having the atmospheric plasma system our operators had to hand wipe every terminal block prior to printing. Not only was this inefficient, but when you are printing thousands of parts it is very easy to miss a few pieces with the manual wiping process.”
Jordan’s team was able to test the feasibility of plasma by running a complimentary lab trial at Enercon Industries Corporation, (Menomonee Falls, Wisconsin). WAGO uses a Markem-Imaje inkjet printer and the printing results with pretreatment were flawless.
Clean, Etch and Functionalize Surfaces
WAGO relies on Enercon’s Blown Ion Series plasma treater to prepare the plastic surfaces for printing. By their nature, most plastic surfaces are non-porous, inert and hydrophobic with few available bonding sites due to low levels of charged ions. Additionally, surface contaminants and release agents migrating to the surface of the plastic negatively affect the chances for adhesion success.
The blown ion treater bombards the plastic surface with a high velocity stream of charged ions which cleans, etches and functionalizes the plastic surface. Contaminants are removed, bonding sites are increased and the surface energy of the plastic is raised, which all contribute to increased ink adhesion.
How plasma is created
Blown ion air plasma systems push pressurized air past a single electrode which discharges inside the treater head. The electrode creates positively charged ions in the surrounding air particles. The air pressure forces the air particles to accelerate of the tip of the head as a high velocity stream of charged ions directed toward the substrate surface. Through direct contact, these particles positively charge the object’s surface increasing its surface energy and making it more receptive to inks.
More Production Throughput in Less Time
Jordan says WAGO has increased efficiency and virtually eliminated poor ink adhesion with the addition of the atmospheric plasma treater. “With the plasma treater we know that each and every part is receiving the same treatment. We’re eliminating surface energy as a production variable and that in turn leads to greater efficiencies and consistent adhesion results. We’ve increased throughput by two and half times. This eliminated the need for us to add an additional printing line.”
WAGO now has three surface treating systems for different applications throughout their facility. “Enercon has provided us with some great tools to help us improve our operations. They are very dedicated to ensuring our success and supporting the quality equipment they produce,” says Jordan.
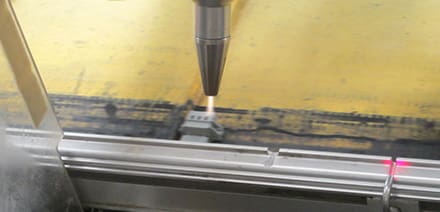