Sauder Manufacturing Ensures Adhesion Consistency with Corona, Plasma & Flame Surface Treating
As Sr Research Scientist at Sauder Manufacturing in Archbold, OH John Beck has seen his share of production challenges. His first experience with surface treating took place in the 1980s when he was part of a team that needed to improve lamination adhesion.
They invested in a 66” wide Enercon corona treater to increase the surface energy of their substrates to improve their lamination success. As a scientist, Beck became a fast student of surface energy, adhesion and good equipment. “We began using Enercon corona treaters in the 1980s. We visited their plant and we were impressed. Now some thirty years later, we’re using their plasma and flame treater technology as well to enhance our production,” says Beck.
One of their current challenges involves working with lightweight decorated papers produced from eucalyptus. Beck has learned over the years that the paper making process has tremendous variability. And, while paper manufacturers do their best to produce consistent product, it is nearly impossible to eliminate variations in hydrophobic properties. To eliminate this variable from affecting their production processes, Beck and his team employ various pre-surface treatment technologies to ensure consistent adhesion results.
Sauder Manufacturing Ensures Adhesion
Surface treaters are implemented in line with existing processes. They are designed to clean, micro-etch and functionalize surfaces to promote adhesion. Over the years, Sauder has learned a great deal about surface treating and in their facility today you will find Enercon corona, plasma and flame technologies.
Ideally, surface treating should take place immediately prior to printing, coating and laminating. This provides a freshly treated surface and maximizes the activation of the surface. Sauder relies on a new 27” Enercon CoronaFlex™ narrow web corona treater to handle treatment of PP films on their profile wrapping lines.
While having the right technology installed is crucial, so is employee training. “When you observe a surface treater in action, your naked eye will not see any change to the surface after treatment,” notes Beck. “This means your operators may not understand the importance of getting the treatment right.” Sauder invests in training its employees in the science of surface treatment to ensure consistency in production.
Anyone who watched the trial could instantly see the effectiveness of the plasma treatment; it was night and day.
John Beck, Senior Research Scientist of Sauder Manufacturing
Seeing is believing
For some applications, surface treating is an added insurance that eliminates a process variable. In other cases, adhesion is simply not possible without it. Over the years, Beck has become an advocate of surface treating, but for some, seeing is believing. They recently brought in an Enercon Blown-ion plasma treater to see if it would help improve adhesion on a low energy polyolefin requiring hot melt chemistry for 360 degree overwrap.
The end product is a drawer and the overlap covers the bottom of the drawer. During the test, the Sauder team gathered around to see if the technology would work. With the plasma treater turned off, delamination was almost instantaneous. With the plasma treater turned on, the wrap bonded securely. For Beck this was one of the easiest equipment justifications he has ever made. “Anyone who watched the trial could instantly see the effectiveness of the plasma treatment; it was night and day,” recalls Beck.
Of course, corona and plasma are not the only technologies used by Sauder. The company also employs flame treaters from Enercon for some specialized applications involving wider width products. Enercon’s high velocity power flame burners provide advanced combustion control for the reliability and consistency required by Sauder’s operations.
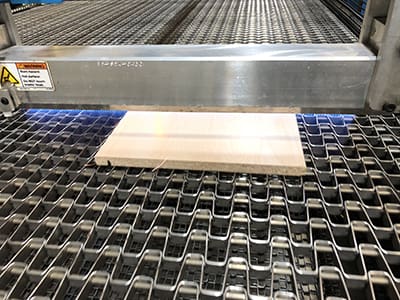
Sauder’s reliance on Enercon has grown over the years. “Enercon has always offered us tremendous support and reliable technology. They have a great lab, knowledgeable people, and the equipment is built right here in the USA. It’s really been a great partnership for over 30 years,” notes Beck.
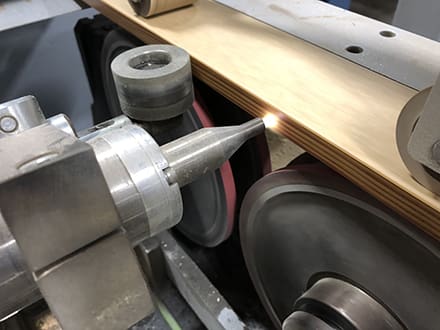