Why Plasma Surface Treatment Is Critical for High-Quality Inkjet & Pad Printing
When it comes to achieving reliable ink adhesion with direct-to-product printing, the secret is on the surface. The printing on your products tells a story, and achieving flawless results requires more than just the right printing equipment and high-quality ink. Surface preparation plays a starring role in bringing those vibrant visions to life.
Plasma surface treatment is a game-changer for many direct-to-product printing processes. By optimizing the bond between the surface materials and inks, this treatment helps achieve sharper and longer-lasting results. Without the right attention to surface treatment, even the best designs can fall short of expectations.
The following are types of direct-to-product printing applications plasma treatment can help with:
- Date and lot codes printed on caps, containers, bottles, and packages
- Product identification printed on wires, cables and pipes
- Printed product markings, such as CE and UL
- Direct printed labeling for packaging applications
- Full color printing on gift cards, golf balls, and promotional items
Whether you’re exploring solutions to improve adhesion or seeking insights into what can enhance your final products, you’re in the right place. Learn why plasma surface treatment is critical for high-quality inkjet and pad printing.
Improving Ink Adhesion for Lasting Printing Results
The foundation of a high-quality print depends on how well the ink adheres to the surface. A poor bond can result in smudging, peeling, or fading, which compromises not just the product’s appearance but its usability as well.
Options like plasma surface treatment play a pivotal role in preparing materials to accept ink. It increases the surface energy, essentially creating a friendlier environment for the ink to stick. Think of it like prepping a wall before painting—you wouldn’t paint over grease or grime and expect smooth, lasting results. Proper treatment means your ink adheres securely, even on challenging surfaces like plastics, glass, and metals.
Strengthening Product Durability for Real-World Use
Imagine receiving a product with a print that starts to fade or scratch off within days. It’s disappointing and it reflects poorly on the brand. And for some industries, like wire and cable, the product can even be rejected if the printing does not pass durability tests. Surface treatment solves this problem by creating an effective bond between the material and the ink. Without this critical step, even the best designs are at risk of deterioration during packaging, transit, storage, or everyday use.
Plasma treated surfaces materials hold up to friction, moisture, temperature shifts, and more. Ultimately, this extends the life of your products and maintains that professional look. A high-quality print speaks volumes about a company’s focus on quality and attention to detail.
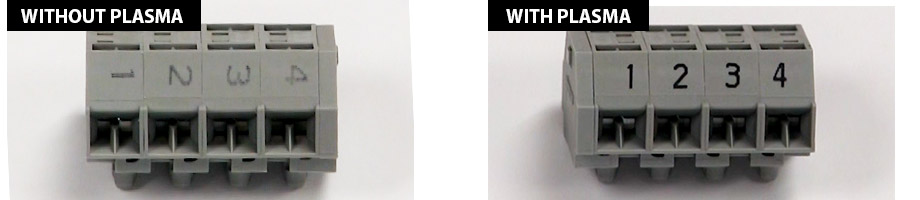
Bringing Flexibility to Material Options
Every printing project comes with its own set of challenges, especially when working with surfaces like plastics, glass, or aluminum. Plastics have low surface energy, which makes it harder for ink to adhere properly without robust surface pretreatment. Glass and metal have higher surface energy but are often compromised with surface contamination and oils that interfere with ink bonding. Plasma surface treatment adjusts their surface properties so they can successfully bond with the ink, expanding the range of materials you can print on.
This opens the door to a world of creative possibilities, from unique packaging designs to distinctive product branding. For example, creating eye-catching direct-to-product printing, durable markings on metal panels, or branded images on plastic containers becomes not only possible but seamless.
Delivering Clear Indelible Printing and Marking
A great design deserves ink adhesion that looks great when printed and stands the test of time. When printing ends up uneven or muted, it’s usually a sign that the surface wasn’t ready to accommodate the ink. Surface treatment plays a key role in leveling the playing field. It prepares and balances the material so that every millimeter absorbs ink in the same way, which results in consistent, vivid printing across the entire piece.
Without proper preparation, some areas of the product can repel ink or absorb it unevenly, leaving behind blotches, streaks, or lighter patches. For packaging, branding, and marketing materials, crisp printing communicates value and attention to quality.
Reducing Waste and Improving Production Efficiency
Skipping surface treatment can lead to ink smudging, uneven ink adhesion, or printing that does not pass your or your customer’s quality control process. This could lead to products that must be thrown away, hours of rework, or lost customers due to product quality concerns. This problem compounds when working on large runs, as even a small issue can mean discarding hundreds or thousands of units. Surface preparation mitigates these risks by creating optimal conditions for the ink to adhere correctly the first time.
Plasma surface treatment reduces errors during production and keeps production timelines on track. Efficient workflows mean more consistent quality and fewer rejects, which improves not only your bottom line but also the satisfaction of your team and customers.

Making Specialty Projects Possible
Printing isn’t always as straightforward as working on a flat sheet of paper. Unique projects like printing on bottles, curved surfaces, or highly textured materials introduce a whole new challenge. Many of these specialty surfaces don’t naturally work well with traditional inks, but plasma surface treatment enables consistent and vibrant results.
Plasma treatment adjusts the material properties and preps them for demanding applications without sacrificing quality. This means you’re able to tackle high-performance projects that require extreme durability.
Taking Advantage of Plasma Treatment Solutions
Plasma surface treatment is a secret weapon that brings an edge to your printing capabilities. Imagine being able to explore printing on creative materials or tackling unconventional surfaces, all while maintaining the same high standards your customers expect.
Every project has a story to tell, and quality products show your audience that you value their trust. Investing in plasma surface treatment for high-quality inkjet and pad printing represents a commitment to delivering excellence in every piece that represents your brand. The details matter, and taking that extra step by working with Enercon Industries speaks volumes about your company’s care and professionalism.
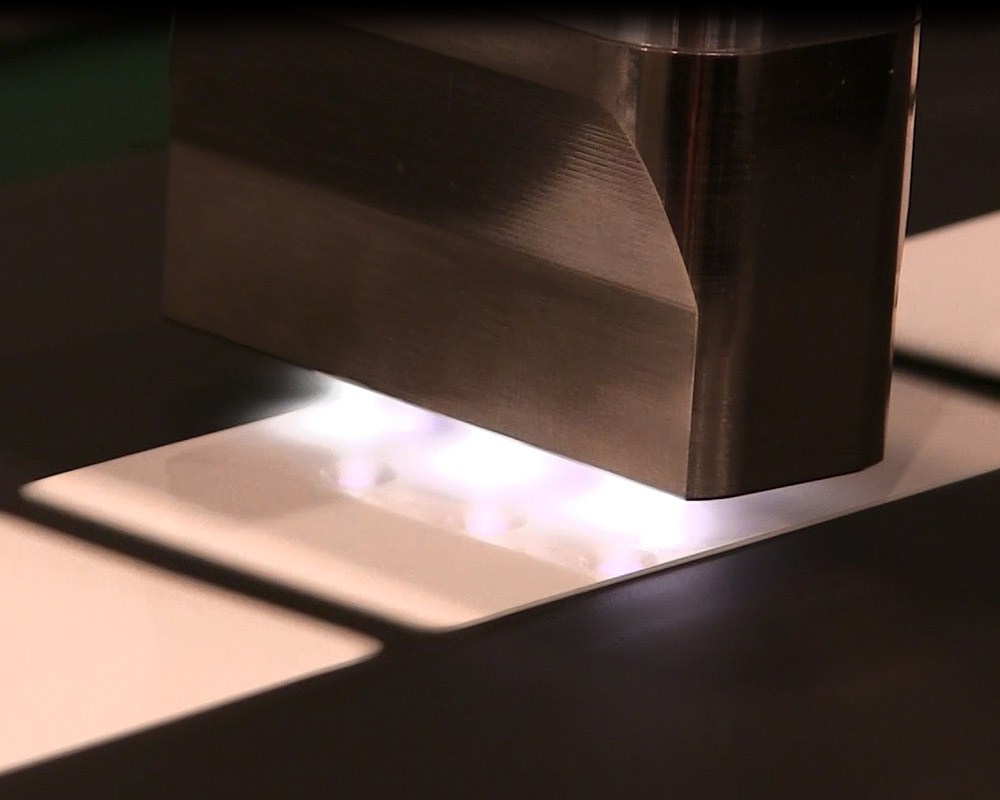