Champion Plastics Adds Enercon Plasma Surface Treater & Helps GM Increase Fuel Efficiency
This remarkable project enabled Champion Plastics to improve operational efficiency and quality, optimize employee utilization and safety and significantly reduce operational costs.
When Champion Plastics earned a high-volume program from GM, the company was ecstatic. At the time, they didn’t realize the project would lead them down a path of innovation culminating with a prestigious award from Manufacturers Association of Plastics Processors. In the end, the plasma project was a win for GM, a win for their employees and a win for their bottom line.
THE PROJECT:
Deliver Parts to GM to Increase MPG Rates
Champion Plastics produces injection-molded products in its manufacturing facility in Auburn Hills, MI. The new project involved producing a TPV (thermoplastic vulcanisate) seal for a gap in the spoiler of a GM vehicle to improve performance in the wind tunnel and ultimately save fuel economy.
In addition to producing the parts, Champion Plastics needed to provide the value added services of applying a pressure sensitive adhesive tape to the TPV surface. However, because TPV has an inherently low surface energy, a surface adhesion promoter was required to enable bonding with the tape. This process required multiple operators to apply the liquid adhesive promoter and an additional operator to apply the tape.
Jeff Ignatowski, President of Champion Plastics, immersed himself in the process and soon recognized how laborious & inefficient the process was for his coworkers. He was determined to find a better way with an ultimate goal of completing the process within the injection molding cycle.
“I was very pleased with my experience, process and results of the Enercon lab trial. The lab gave me the option of doing a preliminary proof of concept to see if my idea would even work before jumping in too far.”
Jeff Ignatowski, Champion Plastics
Listen to Jeff Ignatowski talk about his experience with this award winning plasma project.
THE SOLUTION:
Automation with Plasma Eliminates Adhesion Promoter
The first step was to get rid of the manual and hazardous process of applying the adhesive promoter that required masking and proper ventilation for the operators. Earlier in his career, Ignatowski had heard of atmospheric plasma surface treating for improving surface adhesion. He reached out to Enercon Industries and confirmed that plasma treaters clean, etch and functionalize surfaces to improve adhesive bonding. Enercon offered a free lab trial to prove out the concept. “I was very pleased with my experience, process and results of the Enercon lab trial,” says Ignatowski. “The lab gave me the option of doing a preliminary proof of concept to see if my idea would even work before jumping in too far.”
With promising lab results, Champion Plastics consigned an Enercon Blown-ion™ Plasma system. The surface treater generates a plasma that bombards surfaces with an intense, high-speed discharge of ions. Positive ion bombardment facilitates a micro-etching or scrubbing (ablation) effect that can remove (desorb) contaminants from the surface of an object.
The team had one more obstacle to overcome. The side of the part that required treatment was facing the cavity side of the tool. They developed an end-of-arm tool that flipped the part, discarded the runner, presented the parts to the plasma treater and then separated the parts from the cavity. The consignment unit gave them the opportunity to test the plasma in their new manufacturing processes. The process worked flawlessly and Champion Plastics purchased and installed an Enercon Blown-ion™ Plasma Treater directly into the injection molding cycle.
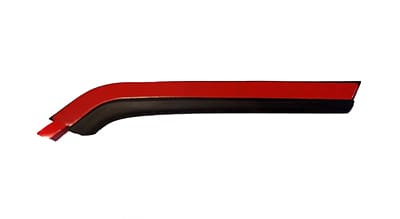
Since implementation, Ignatowski reports that the treater has performed reliably without a single issue. “Overall, I was very pleased with Enercon – ranging from my initial contact, the lab, the sales rep, technical support and ultimately the end product,” says Ignatowski.
The Dramatic Results
Improved Employee Safety:
Eliminated employees handling of hazardous chemicals.
Improved Utilization of Employees:
With a national labor shortage, being able to reallocate three employees to more value adding processes improved company throughput.
Improved Quality:
Eliminating human error from the adhesion promoter application process improved process consistency and quality.
Increased Output:
Automation eliminated a process and unnecessary WIP (work in progress) while reducing lead times.
Industry Recognition:
2022 Innovation Award from Manufactures Association of Plastic Processors (MAPP).
Bottom Line Savings:
Adding the plasma treater and additional automation with tools required a $45,000 CAPEX investment. Reducing labor, adhesion promoter costs, and other operational costs will save Champion Plastics $850,000 over the duration of the six-year program.
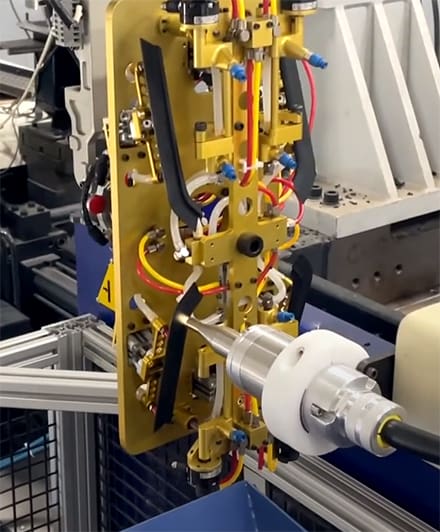