Arla Foods integrates process to packaging concept in England with induction sealers
The Arla Foods plant, near Leeds in England, houses four identical packaging lines. They draw freshly blown HDPE polyethylene bottles from silos and freshly processed milk from processing tanks with minimal operator involvement. Production is monitored and managed by a newly developed automated order system from Syskron called Line Management System. No longer does a shift manager deploy a team of operators to stop and start machines according to a production plan. The stopping and starting are done automatically, leaving operators responsible for changing label reels and replenishing the cap hopper.
“We transmit production orders from the ERP down to processing and packaging machinery and collect data from those machines so that it can be sent back up to the ERP,” says head of engineering Soeren Vonsild. “It makes our business one single unit.”
Vonsild also emphasizes that Arla’s chief goal behind implementing this “new way of doing things” was not merely flexibility for flexibility’s sake. It’s really about quality. It would appear that goal has been met.
“The industry average in the UK for customer complaints per million units is 50 times higher than complaints we’re getting on these new lines,” says Vonsild.
Enercon is pleased to support Arla Foods commitment to quality with multiple Super Seal™ induction sealers on the lines. Vonslid believes that the benefits gained from the automated order system can be extended.
“With the detailed information you get on every single bottle, there’s no limit to what you can do next,” says Vonsild.
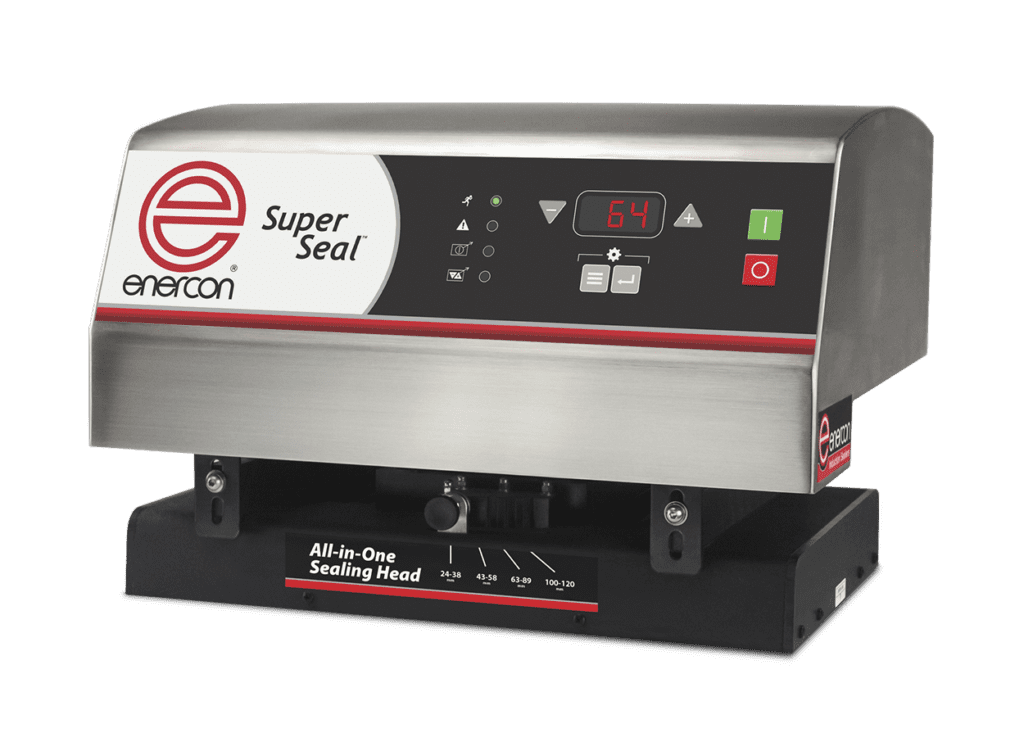