Best Formulations Improves Packaging Efficiency by Standardizing on Enercon Cap Sealers
Contract packagers are often faced with more challenges than a traditional packager. Each day there are new orders coming in for diverse customers. Some rely completely on the contract packager for raw materials and packaging elements. Others supply one or the other. To be successful at contract packaging a company needs to be flexible and at the same time master the packaging technologies that they offer.
Best Formulations (City of Industry, CA) is one of the largest contract packagers with responsibility for packaging thousands of branded nutritional supplements, pro biotics, pharmaceuticals, food and teas. These products are manufactured in a wide variety of configurations including vegetarian soft gel capsules, hard shell capsules, tablets, powders, liquids and more.
Benefits of Standardizing on Equipment Brands
When Dwayne Chrest took over as Production Manager for Best Formulations five years ago he made it a priority to focus on selecting key suppliers for packaging equipment so that he could rely on what he calls “the trifecta of a good supplier; knowledgeable people, reliable equipment and support for products and applications.”
One of the areas that he wanted to standardize on was induction cap sealers. Induction sealing produces a hermetic seal on containers which can be used to provide tamper evidence, preserve freshness and prevent leaks. The electromagnetic field produced by an induction cap sealer heats the foil part of the innerseal which in turn melts a polymer coating causing the innerseal to bond to the lip of the container.
At the time Best Formulations had several different brands on various lines throughout their plant. The lack of consistency between lines created challenges for keeping his staff trained on how to operate each of the systems.
It was at that time the Best Formulations team procured quotes from a number of induction cap sealer suppliers. They choose Enercon Industries (Menomonee Falls, WI) because of their induction sealing technology and the responsiveness of their team, including local representative Todd Kasik (Packaging Sales Equipment Corp).
The Super Seal™ Cap Sealer that they purchased offered them more sealing power and a unique sealing head that allowed them to seal anything from 28mm to 120mm diameter caps. This made the Enercon sealer the most versatile sealer in their facility, a particularly important benefit for a contract packager.
Chrest attended Enercon’s free educational webinars on line and began gathering training materials for his team from the company. ‘The information Enercon provides its customers, from both an equipment and application standpoint, is fantastic. We looked for this type of information from other suppliers and it either wasn’t available or wasn’t very good.”
The Best Formulations team studied the Enercon educational materials and soon recognized the importance of quality control and the induction sealing process. Chrest says, “We know what to look for. Poor seals are often the result of poor torque or material issues.” As a contract packager sometimes Best Formulations relies on their customers to supply the packaging materials such as induction lined caps. “We added an Enercon foil detector and container rejection device as part of our quality control. We tabulate which suppliers have the least amount of defective products and use that information not only for our purchasing decisions, but also to alert our customers if their suppliers should be doing a better job.”
Today Best Formulations has four Enercon cap sealers and are standardizing with Enercon. The consistency of equipment between packaging lines enables their operators to become experts and be capable of working on different lines in the facility.
The relationship developed with Enercon proved beneficial on another packaging project as well. This time it was for improving ink jet adhesion for lot codes on their bottles. Read how Enercon’s atmospheric plasma treaters improved inkjet adhesion.
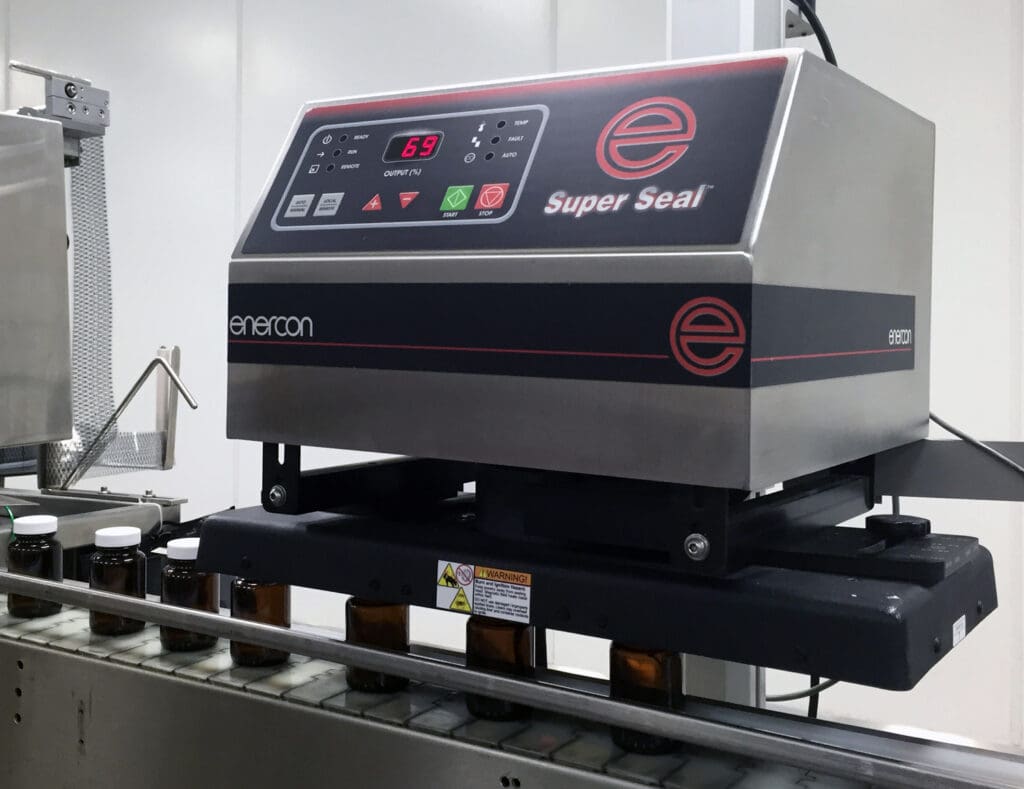