Enercon Cap Sealers & Support Keep Liquid Cleaning Co-Packer Operating Efficiently
For decades RGA Enterprises (Charlotte, NC) has co-packed liquid cleaning products such as bleach, degreasers, and other chemicals. As a co-packer, they face the challenge of dealing with different products and containers on a daily basis. So, when they need assistance with induction cap sealing, they look for a seasoned partner to provide them with reliable technology and support. According to RGA Maintenance Manager Doug Beckham, Enercon Industries (who are celebrating their 50th year in business) provides RGA Enterprises exactly what they need.
Beckham is responsible for ensuring RGA’s packaging lines are optimized for production. One of his major challenges is finding equipment that will hold up to the caustic and corrosive nature of the bleaches and other chemicals RGA packages. Damage can occur from chemicals including oxidation of parts and equipment. The Enercon cap sealers have lived up to the challenge. RGA’s large production facility houses three very old Super Seal™ sealers, an ancient, water-cooled sealer, and they recently added a new Enercon Super Seal™ cap sealer. The latest Super Seal™ sealer features a new microprocessor-based control board that supports an assortment of new features.
The older sealers have stood up to the harsh environments, but Beckham concedes that as with all equipment reliant on electronics, components do become obsolete and unserviceable over time. “We plan to replace the older sealers as we can. I love the simplicity & reliability of how the Enercon sealers operate,” says Beckham. In the meantime, the older Enercon systems continue to be reliable workhorses.
Application Support Ensures Sealing Success
Enercon’s support extends beyond the sealing equipment they provide, beginning with the company’s cap sealing lab. Jessica Toellner, Enercon’s Senior Regional Sales Manager and cap sealing expert says, “Our cap sealing lab is stocked with our complete line of induction cap sealers. We have a wide array of sealing heads, including custom designs, to make sure our customers always have the best sealer and sealing head configuration for their specific products and operating conditions.” Jessica ran several sample trials for RGA to troubleshoot and find solutions when they run into application issues.
“Sending in our samples to Enercon is a great process and the support is outstanding. We spent a day and a half trying to solve an issue sealing some caps, but once we contacted Jessica, she was able to get us back up and running and provided us with advice on what to do in the future to avoid these types of issues,” recalls Doug Beckham.
Importance of Setting up an Operating Window
Achieving a Perfect Seal requires the right sealer & sealing head along with compatible caps, bottles & liners. But in addition to that, Enercon shares with its customers the final key in achieving a perfect seal: setting up an operating window for each application. Toellner explains, “Setting up an operating window is a cornerstone principle to achieving a perfect seal and is affected by three variables: pressure, heat and time. Pressure on the liner is created by the cap torque on the closure, which should be sufficient and consistent. Heat is applied through the Enercon induction sealer via an electromagnetic field. Time is how much dwell time a foil liner needs under the induction coil to heat to the correct temperature for a perfect seal. The key to dwell time is knowing your conveyor speed. If your conveyor speed is consistent, you simply test sealing containers at varying sealing energy levels until you determine when the energy is too low to create a seal and too high because it burns the seal. The range in between is your operating window.”
“Our experience with Enercon has been above the standard in the marketplace due to the support that Enercon provides, not only when purchasing equipment but when we have problems in the field as well,” concludes Beckham.
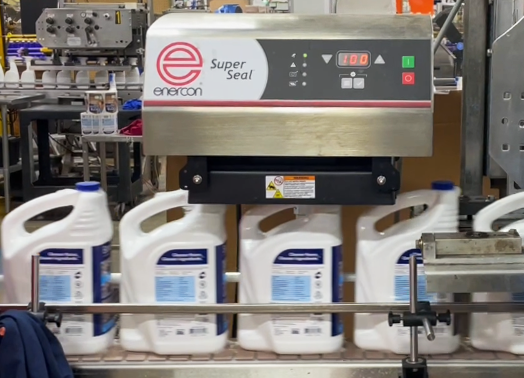