Inconsistent Application Torque Equals Inconsistent Seals
In order to get a good hermetic seal, it’s necessary for the foil innerseal inside of the cap, to be in contact with the lip of the container and have consistent pressure around the circumference. This is accomplished by applying the cap with the correct application torque.
Most packagers don’t realize the effect application torque has on the induction sealing process. For many years, the suggested application torque to achieve a good induction seal has been one-half of the diameter of the cap in inch/pounds.
As an example, a 38mm closure should have an application torque of 18-20 inch/pounds, a 53mm closure, 25-26 inch/pounds and so forth.
Cap Size (mm) | 15 | 18 | 20 | 22 | 24 | 28 | 33 | 38 | 43 | 48 | 53 |
Torque (inch/lbs) | 6 to 9 | 7 to 10 | 8 to 12 | 9 to 14 | 10 to 16 | 12 to 18 | 15 to 25 | 17 to 26 | 18 to 27 | 19 to 30 | 21 to 36 |
In many cases, especially when the caps are being applied by hand, application torque is all over the place. The result is inconsistent seals. You can imagine what will happen when you have six different people applying closures. You end up with six different application torques.
This can also be caused by cappers that are out of adjustment or have worn tightening wheels. Another cause of inconsistent seals is mechanical in nature, caused by poor bottle/closure tolerances, resulting in the caps and bottles not fitting together properly. Sometimes these irregular fits can be solved with the proper types of foil innerseal.
However, in discussions with cap, bottle, and innerseal suppliers, they all agree the biggest problem is inconsistent or insufficient application torque.
If you have a percentage of containers that are not sealing properly, check your application torque. It may save you a lot of problems.
Check out the online torque guide or contact us for a personal copy of the cap ruler and torque guide.
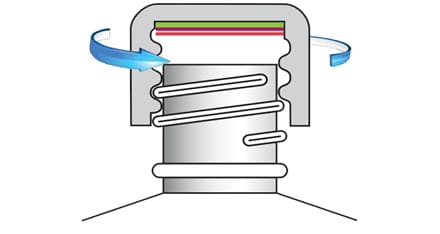