Induction seal improves seal quality and shelf-life for Nestle New Zealand’s Snap-on cap
When Amseal, Enercon’s local representative in New Zealand, brought in a sealing project for a non-round and non-threaded container it would have been easy for Enercon’s induction sealing experts to turn the project down. But instead they rolled their sleeves up and developed a custom solution for one of the world’s leading manufacturers: Nestlé of New Zealand.
Nestlé’s Cambria Park engineering team needed to improve seal quality and shelf life on PET containers with snap-on caps. Nestlé Project Engineer Greg Smith cites the key advantage in switching from heat sealing to induction is seal placement. The heatseal membrane was picked from a magazine and placed over the plastic containers and tacked on prior to sealing. Imperfect membrane placement and imperfect containers caused a faulty seal, resulting in reduced shelflife and product damage.
With induction, the liner is captured inside the plastic snap-on closure as the closure is applied. The cap’s non-round shape is challenging because induction currents typically run in a circular or oval pattern. Through proprietary design technology, Enercon’s engineers came up with a way to force the currents in a non-circular pattern. Of course this all had to be accomplished fast enough to keep pace with the two-up auger filler that cycles 21 times/min. That meant induction sealing would have to take place in 0.7 sec.
“The induction sealing system produces a far superior seal.”
Nestle Project Engineer Greg Smith
“Enercon managed to achieve this short seal time by shaping the induction heads to fit within the container lids,” Smith says. “This helped draw the heating effect towards the outer corners of the container to produce an even seal throughout the container rim.” Nestlé handled the next challenge which was ensuring there was enough pressure on the snap-on cap to successfully seal. They added a special indexing unit whose pneumatic lifts elevate the containers and press them against the induction sealing heads.
The sealing heads also compensate for variations in the cap. They are fitted with a pad that results in more reliable sealing because it molds itself to slight imperfections in the cap.
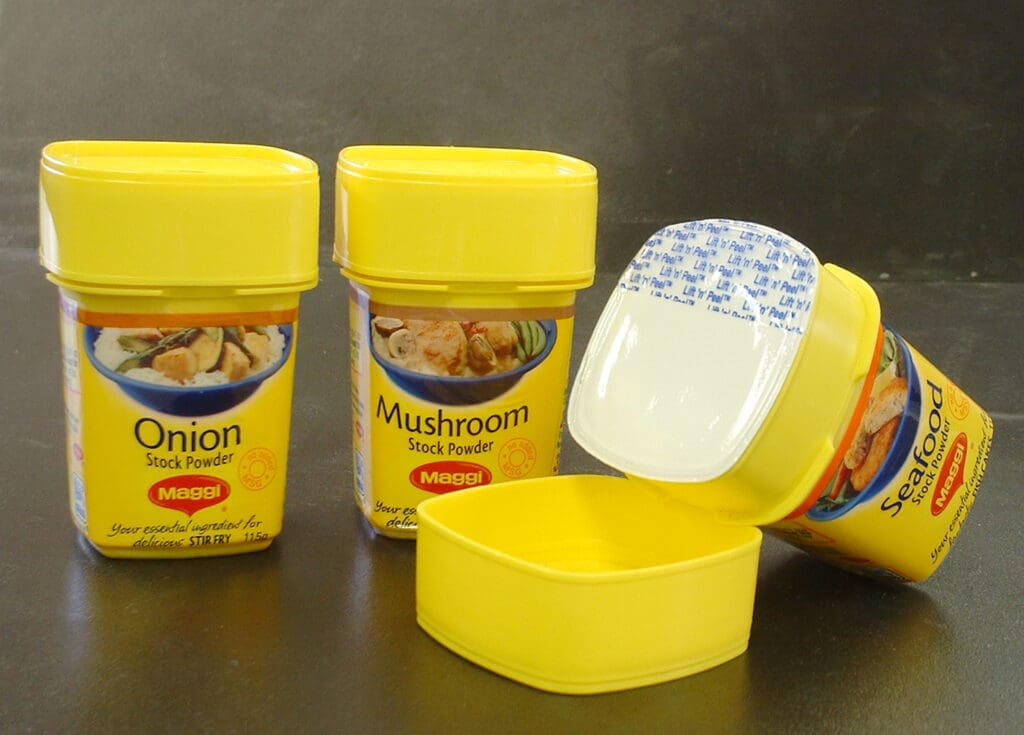