Induction Sealer KIKs Production Speeds Up a Notch
KIK Custom Products (Concord, Ontario) manufactures private label products for some of the world’s largest retailers as well as, contract manufactures brand products for companies such as P&G, Colgate and Johnson & Johnson. They have fourteen manufacturing sites across Canada and the United States and three major distribution centers. Their portfolio of products range from household cleaners like bleach to personal care items such as shampoo.
The Classic Division of KIK is responsible for manufacturing private label household cleaners. Retailer (generic) brand bleach is KIK’s original product line and still thrives as their core product. Mario Ottati, Director of Engineering, is charged with the responsibility of overseeing the Classic Division’s packaging equipment which includes 20 lines dedicated to bleach across several facilities.
In-House Equipment Exploration
Ottati is constantly on the lookout for packaging equipment that will keep KIK’s production running at full capacity. While visiting one of KIK’s personal care facilities, he inquired about the Enercon Super Seal™ induction sealer mounted on their line. What appealed to him was the compact design with the stainless steel cover and the enclosed sealing head.
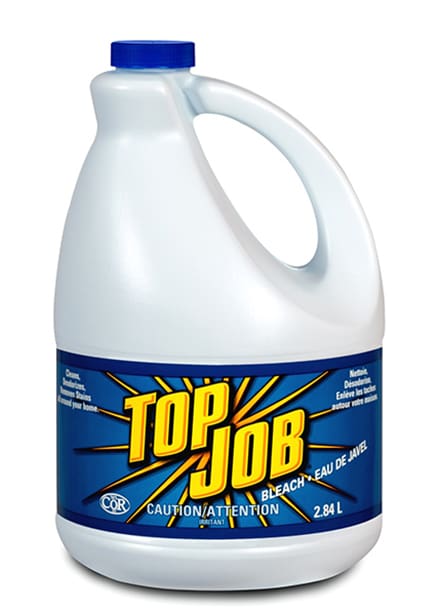
With the corrosive nature of bleach, it is important to Ottati that all the components in the sealer are durable. An induction seal is necessary on bleach bottles to prevent leaking of the potent chemical.
“Enercon’s equipment is designed to hold up in the most challenging environments,” states Jeff LaGrange, Enercon Product Manager. “We have numerous installations across the globe operating in harsh environments.”
The cap sealer is comprised of two main components: the sealing head and power supply. An induction seal is created when a capped bottle with a foil passes under the sealing head. The sealing head produces an electromagnetic current, which then heats the foil in the cap. The polymer coating on the inner-seal melts, releasing it from the cap and bonding it to the lip of the container.
“Every bottle of bleach has to be induction sealed. If the induction sealer goes down, the whole production line goes down,” explains Ottati.
In 2009, Ottati received a used Enercon Super Seal™ cap sealer from another KIK facility and put it to the test. KIK packages a range of different sized bleach containers made of HDPE and topped with 38mm child resistant caps.
“The most immediate difference I noticed was in terms of maintenance. There practically was none! With our other vendors, every six months we had to either replace a sealing head or power supply.”
KIKing up Production Speed
In 2010, Ottati purchased his first Super Seal™ induction sealer with a narrow tunnel sealing head optimized for his application. As a result, KIK’s bleach production lines were running faster and they were also getting much more consistent seals.
“Since that moment, I have not purchased another brand of induction sealer. Enercon is our preferred vendor,“ says Ottati.
“One time, I had an emergency and needed an induction sealer as soon as possible. I called Enercon and within a day and half it arrived at our facility. Enercon puts their customer’s needs above their own.”
With the release of Enercon’s new Super Seal Touch, KIK started installing them on their line enabling them to ramp up their lines speed even more as they continued to phase out their old equipment. The new touchscreen control also appealed to Ottati. He found that non-technical operators were able to easily navigate through the settings and the clear interface made it easy to see from a distance.
Quality Control
With the potent potential of bleach, KIK takes every measure to be in control of their product packaging. They added foil detection to their induction sealers to help identify caps with missing foil liners. The bottle is then discarded before leaving the packaging line, eliminating the chances of a leaky product.
KIK blow molds their own containers to ensure consistent quality. In addition to installing new induction sealers, they also purchased new inline cappers from Pack West Machinery (Irwindale, CA). In return, KIK now has an efficient, reliable packaging process running at faster speeds than ever before.
“Operation costs have gone down considerably due to the increased uptime. Enercon machines never fail,” concludes Ottati.
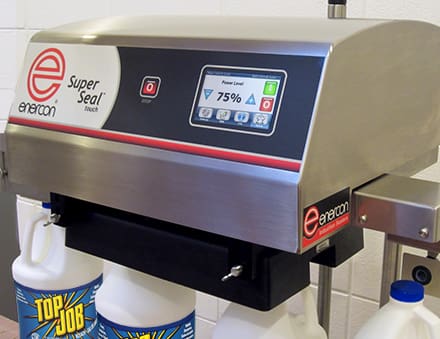