Oil company goes green with air cooled induction sealers
Olive oil has been produced for thousands of years dating back to the time of Homer who referred to it as “liquid gold”. Today when you visit the grocery store you see hundreds of varieties lined up on the shelf, varying in flavor and price. As the product has evolved over the centuries so have the packaging methods.
The late Joseph O. Basile started Catania-Spagna (Ayer, MA), an oil processing and packaging company, over 100 years ago in 1900. Four generations later, while Catania-Spagna is still providing their customers with the same service, quality and reliability, their methods and packaging technology have evolved.
Catania-Spagna packages and processes cooking oils ranging from vegetable to fine olive oil, servicing the retail, restaurant, bulk and export food industry. They operate four packaging lines to keep up with their demand, two of which rely on induction sealing technology.
Induction sealing technology is comprised of two main components, the power supply and the sealing head. When energized by the power supply, the head produces an electromagnetic current, called an eddy current. The capped bottles enter the electromagnetic current and the foil of the innerseal generates electrical resistance, heating the foil. The hot foil in turn melts the polymer coating on the innerseal. The heat, coupled with the pressure of the cap, causes the innerseal to bond to the lip of the container. The result is a hermetic seal.
Induction sealing technology isn’t new to these seasoned packaging veterans. They’ve used induction sealing for over 20 years to keep their products’ seal integrity intact. Catania-Spagna started using Enercon (Menomonee Falls, WI) equipment in the 90s when installing their water-cooled induction sealing systems. After over a decade of use it was time to upgrade.
There has been a rapid shift from the use of water-cooled induction sealing systems to air-cooled systems across the packaging industry. Enercon’s breakthrough in sealing head design allows for higher sealing efficiencies and the elimination of the water recirculator. Air-cooled power supplies are able to achieve speeds that were once only in the realm of water-cooled systems and require a lot less maintenance.
“Our 2008-2009 initiative was to go green; one of the first places we started was by replacing our Enercon water-cooled induction sealers with air-cooled systems,” said Steve Sampson, Vice President of Operations.
Catania-Spagna replaced five of their water-cooled induction sealers with Enercon’s Super Seal™ air cooled systems. The induction sealers support their “gallon line” and “jug-in-a-box line”, sealing high density polypropylene containers ranging from three liters to two and a half gallons. They use a universal sealing head which gives Catania-Spagna the flexibility to run containers with cap sizes ranging from 20-120mm without having to switch sealing heads.
In addition to the energy saving obtained by the elimination of the water recirculator with the latest air-cooled design, the systems have proven to reduce downtime, maintenance and the amount of defective product. Catania-Spagna has saved thousands of dollars a year by upgrading their equipment.
“The water recirculator had to be flushed on a regular basis. We also struggled with rust and corrosion from the water recirulator. Now, the down time is practically non-existent,” says Sampson.
Catania-Spagna’s green incentive didn’t stop there. They also installed two new energy efficient air compressors, variable-frequency drive pumps and motors which optimize the energy output to the amount of energy actually needed, a new lighting system triggered by sensors and started an in-house recycling program which saves on trash disposal. With these simple green changes Catania-Spagna was not only able to conserve energy but they also save a lot of green. Sampson reported they save upwards of $100,000 a year on energy costs.
With a hundred years of packaging experience under their belt Catania-Spagna knows how important progress is in the packaging industry. They continue to apply innovative packaging solutions, allowing them to keep an edge by delivering their customers the same quality product at a competitive price.
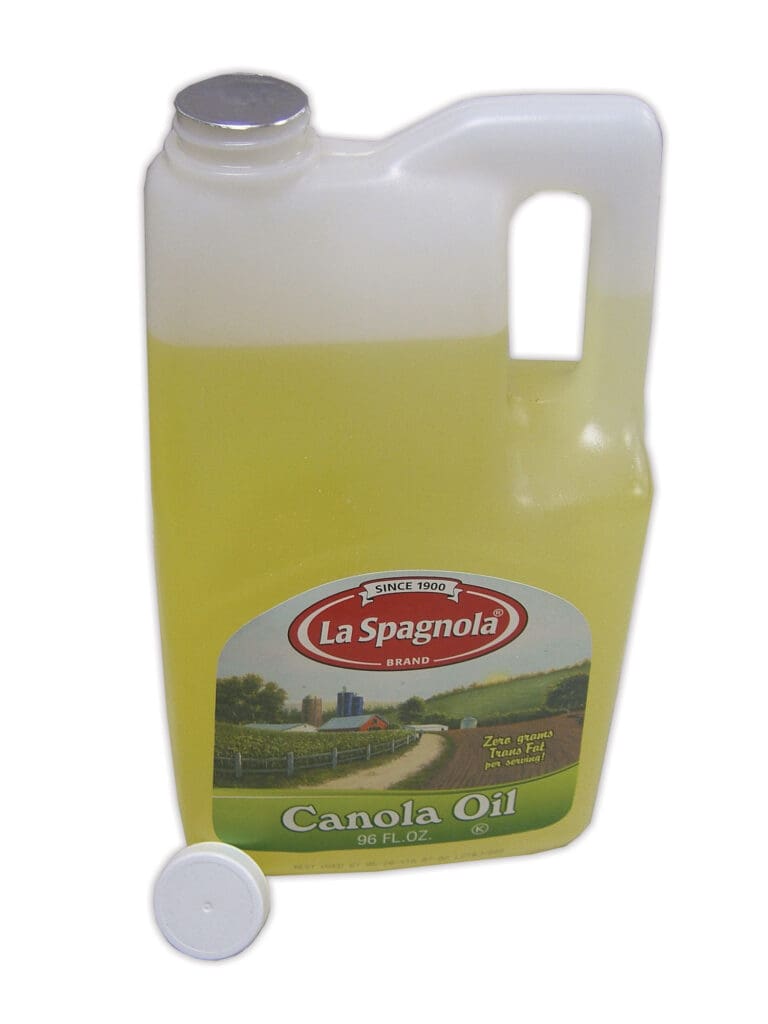