Understanding application & removal torque
One of the key variables in the induction cap sealing process is torque. As it relates to induction sealing, torque stands to be the topic your packaging team needs to understand most. There are two types of torque your team should know about – application torque & removal torque.
We get questions about application torque every day. The questions we don’t seem to get quite as often pertain to removal torque. That changed this week when, a curious packager asked the question … what should my removal torque be after sealing?
The answer isn’t necessarily difficult, but you’re really going to want to look at a couple of items. The first piece is the immediate removal torque. Immediate removal torque refers to the removal torque measured after letting the bottle relax for one minute after capping but prior to sealing. Removal torque you’ll measure, should be about 50% of the application torque.
Cap Size (mm) | 15 | 18 | 20 | 22 | 24 | 28 | 33 | 38 | 43 | 48 | 53 |
Torque (inch/lbs) | 6 to 9 | 7 to 10 | 8 to 12 | 9 to 14 | 10 to 16 | 12 to 18 | 15 to 25 | 17 to 26 | 18 to 27 | 19 to 30 | 21 to 36 |
So, if you’ve got a 38mm closure that you’ve applied 18 in-lbs of torque to, your immediate removal torque will be approximately 9 in-lbs.
When you add induction sealing to the mix, you’ll likely be a bit lower than what the immediate removal torque is. I say a bit lower because the actual amount will vary based on the specific heat induction seal material used.
Any time you heat an induction seal you are shrinking the overall height of the liner. The heat seal layer will compress as it begins to flow & adhere to the land area of the container. Secondly, if you are using a two-piece liner with a wax release layer this layer of wax is absorbed into the pulp board secondary liner, again creating a shrinkage in the overall height of the liner.
Knowing all this you will want to take a representative sample of your packages and measure the immediate removal torque from all heads of your capper. This will verify you have consistent application torque being applied by any and all heads of your capper.
Additionally, you’ll want to measure the removal torque after induction sealing. If you have consistency in your process leading up to the sealer, you will see consistent removal torques exiting the sealer.
If the removal torque after sealing ends up being lower than what you package requires, you may choose to add a re-torquer into your line. Where we see this most often today is with child resistant closures (CRC). You may need to apply some additional torque to the closure after sealing to ensure you meet the required torque to activated the child resistant feature of these closures.
The key to most aspects of the induction sealing process is consistency. Removal torque is no different – if you can apply torque consistently, you’ll see consistency after sealing as well.
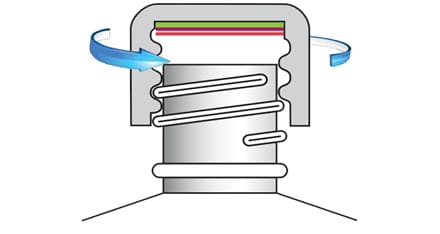