Induction Sealing Hall of Fame
Enercon has worked with leading customers on expanding the application range of induction cap sealing technology. The best examples of this success are represented by HALL of FAME honorees.
The packages below were selected by a panel of induction sealing application experts. Each is being honored for either overcoming technical challenges, improving productivity with an induction seal, or for the significance that the induction seal plays in part of their packaging strategy.
If you think your product belongs in the next class of induction sealing Hall of Famers, contact us.
Most Recent Hall of Famers:
RMR Solutions (Click for Full Story)
Product. RMR-86
Challenge. Improve packaging for new and fast-growing chemical solution used to remove mold & mildew stains in seconds, effectively restoring surfaces back to their original appearance. Initial packaging was subject to leaks through the cap and required products to ship in zip-tied plastic bags to avoid customer complaints. This also prevented the products from being sold through major channels such as Amazon.
Solution. Enercon Super Seal™ Induction Cap Sealer with All-In-One™ Sealing Head and specially vented liners to allow for proper off-gassing. The All-In-One™ Sealing Head enables efficient sealing of a wide array of cap sizes. This sealer performs so reliably that it virtually eliminates customer complaints and leaky packages. The sealed product now satisfies Amazon’s packaging requirements allowing the company to grow its business through new channels.
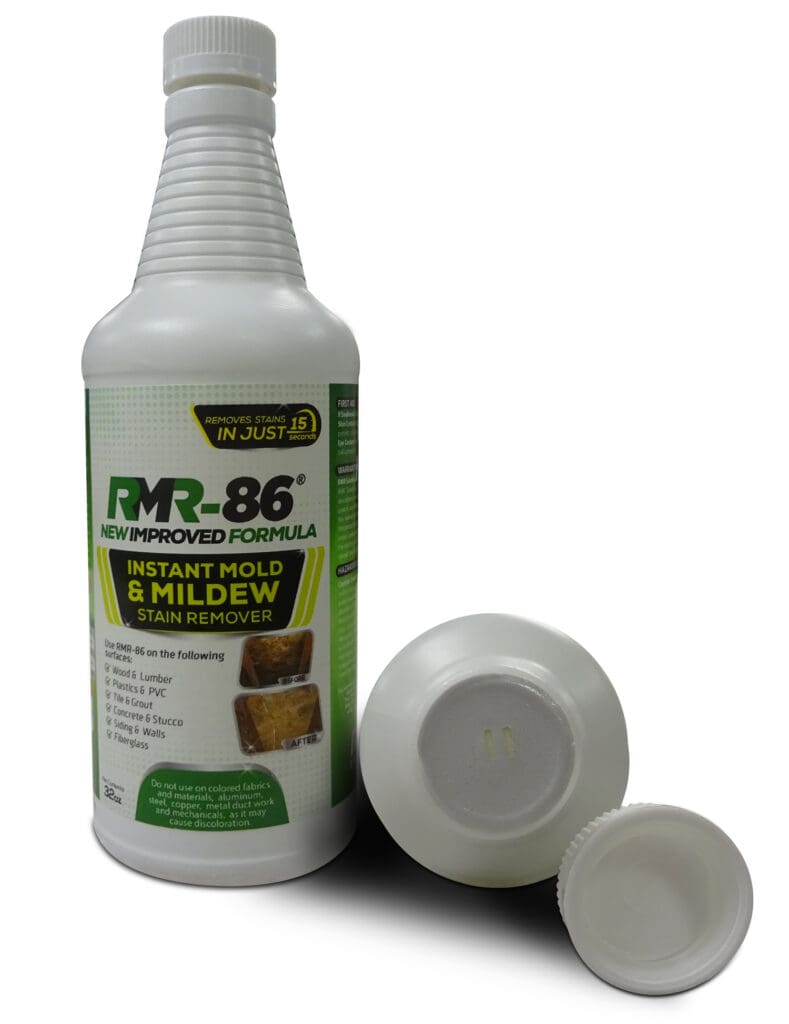
BERICAP Group
Challenge. Create a closure with a liner that provides tamper-evidence, prevent leaks and protects against counterfeiting for high value automotive oils and agrochemical products.
Solution. A unique closure design that features a ring-pull induction liner which provides consumers with easy opening, leak prevention, and assurance against counterfeiting. When the consumer opens the closure, they are presented with a ring-pull which allows them to remove the induction liner. The container cannot be refilled without evidence of tampering, thus thwarting counterfeiting. BERICAP worked with Enercon Industries Limited in the UK to ensure the package could be commercially sealed. Enercon developed and prescribed Super Seal™ Cap Sealers with a special tunnel sealing head for efficient and reliable sealing of the package.
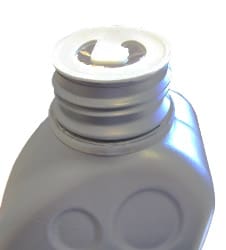
TATCHA
Product. The Pearl
Challenge. Preserve freshness and provide tamper evidence of a new pearl-shaped cosmetic package containing a tinted eye-illuminating product. The pearl-shaped package and cap configuration creates a gap between the induction liner and top of the product.
Solution. Enercon Super Seal™ Induction Cap Sealer with specially designed tunnel sealing head. The unique sealing head directs the sealing energy to the induction liner to achieve energy-efficient and reliable heating of the foil to create the required hermetic seal.
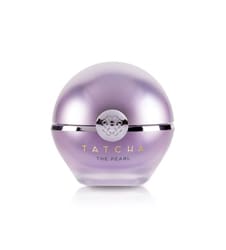
Bay View Packing Company (Click for Full Story)
Product. Pickled Foods
Challenge. Support the company’s move from glass to light-weight plastic jars for their pickle products. Ensure product freshness and prevent leaks on new package.
Solution. Enercon Super Seal™ Induction Cap Sealer to create a hermetic induction seal.
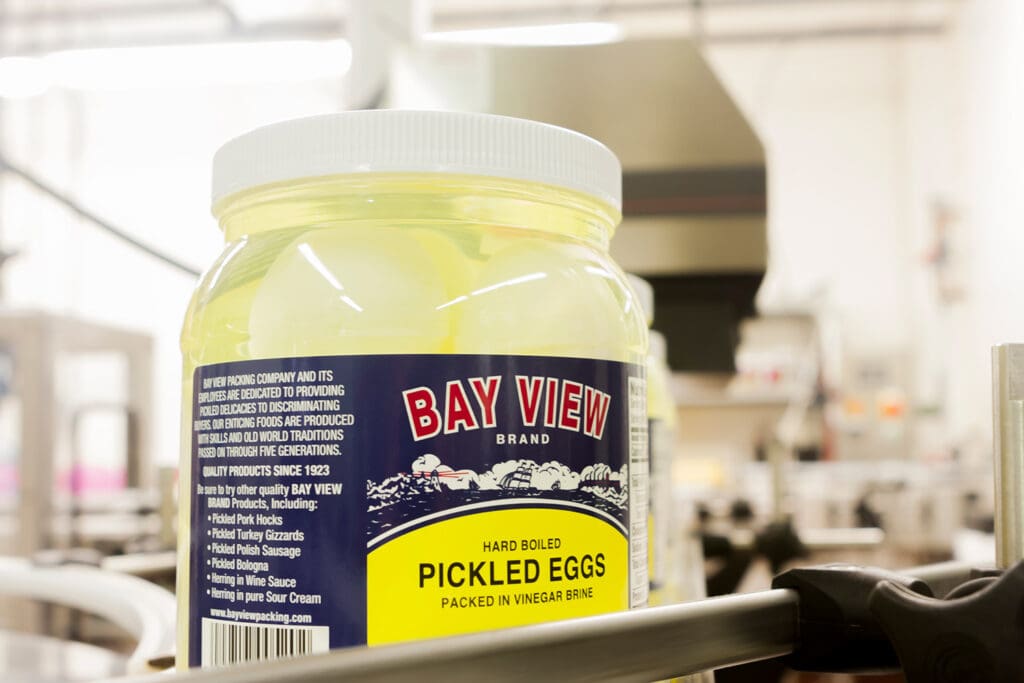
Past Hall of Famers:
DryBev International (Click for Full Story)
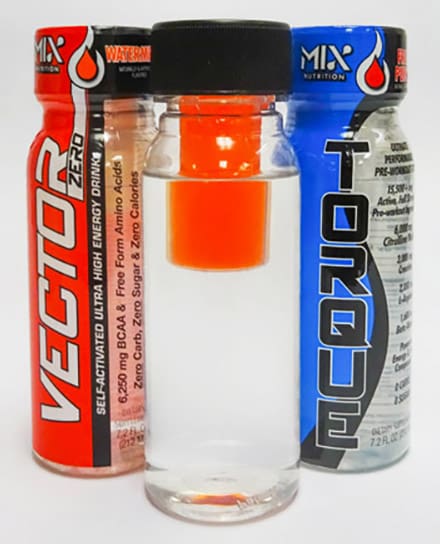
Challenge. New Package Concept allows a powdered formulation to be mixed with a liquid after it has been opened. This extends shelf life and reduces the cost to produce certain types of products. Required a single induction liner to seal two openings to maintain package integrity.
Solution. Enercon engineers configured a special power supply and sealing head combination to ensure sealing energy is applied evenly to the liner to produce two hermetic seals. A traditional induction sealer focuses sealing energy on the outside of the foil.
“To make this packaging concept a reality we needed an induction sealing solution that was scalable and repeatable, Enercon developed just what we needed,” Ted Casey, Owner Dry Bev International
Unilever – Hellmann’s Mayonnaise Squeeze Bottle (Click for Full Story)

Challenge. Seal a new innovative container with a clean lock cap that eliminates drips and offers a precision tip for easy control during use. The container has a recessed foil with a diameter making it much smaller than the diameter of the cap.
Solution. Enercon developed a special sealing head that optimized the induction field to ensure the required sealing power is efficiently delivered to the induction foil. This is critical for creating a consistent hermetic seal and for minimizing the amount of power needed for sealing.
Association of Sauces and Dressings Package of the Year: “We worked with Enercon Industries to design a bottle to help consumers get the most out of the product, and the most product out of the bottle.” Tom Wajda, R&D director at Unilever.
Best Formulations (Click for Full Story)
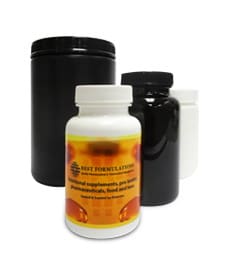
Challenge. Improve induction sealing productivity across all production lines while packaging a wide variety of products and containers.
Solution. The company takes a holistic approach to equipment, looking for suppliers with reliable equipment and training resources to make their operations better. Best Formulations chooses to standardize on Enercon Super Seal™ cap sealers because of their reliability, versatility to seal different cap configurations, and Enercon’s ability to help educate their personnel to maximize their results. As an added benefit, the company learned of Enercon’s plasma treating systems which are now used on every line to improve and enable the company’s ink jet coding processes.
As seen in Packaging World and Contract Packaging Magazine: “It’s a priority for us to focus on selecting key suppliers for packaging equipment which embody the trifecta of a good supplier; knowledgeable people, reliable equipment and support for products and applications,” Dwayne Chrest, Production Manager at Best Formulations.
Mendes Gonçalves (Click for Full Story)
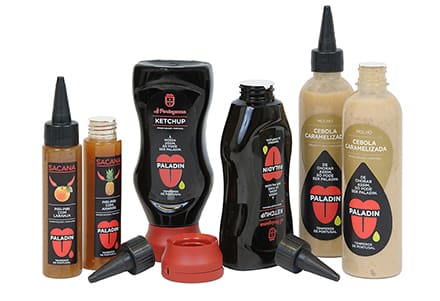
Challenge. Induction seal 120,000 bottles per day, many with a conical dispensing cap, to prevent leaks, provide tamper evidence and extend shelf life for exporting.
Solution. Enercon in the United Kingdom worked with this Portuguese company to ensure their full range of products could be sealed at production speeds. For the conical capped containers which provide shelf presence and consumer convenience, Enercon designed a special sealing head to direct the sealing energy towards the induction liner. Sealing heads may be changed as needed for different applications.
“The Enercon machines are stronger, more efficient and can be easily integrated into production lines to maintain fast production speeds,” Carlos Prino, Industrial Projects Director at Mendes Gonçalves.
Berry Plastics Group – Cosmetic Tubes
Challenge. Induction seal a tube prior to filling.
Why Induction? – Satisfy customers’ request for a closure which prevents leaks, deters tampering, and ensures product freshness.
Solution. Berry Plastics worked with Enercon to creatively position the Super Seal™ Touch’s sealing head to integrate with their existing line configuration. The recipe management option also helps reduce setup time and ensure consistent sealing results when switching between lines, cap sizes, and operators.
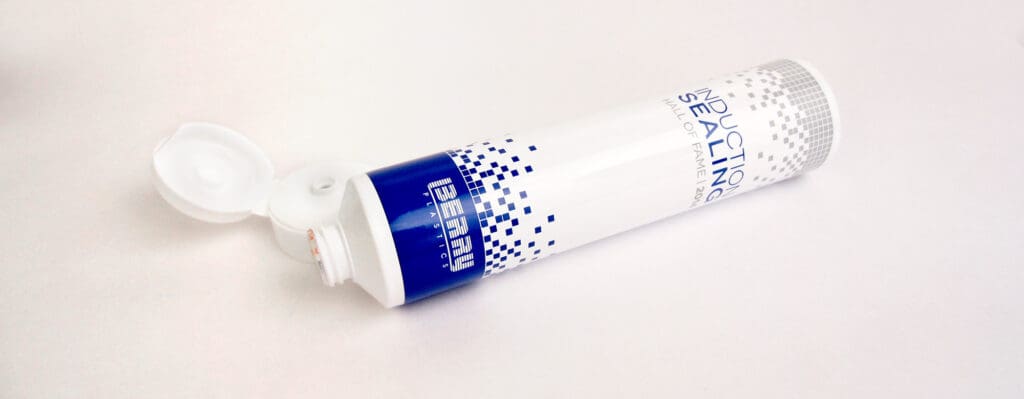
Belcorp – Triple Acción
Challenge. Triple Acción’s uniquely shaped cap creates a large gap between the seal and the top of the cap.
Why Induction? Prevent product counterfeiting, avoid leaks and stop exposure to oxygen and humidity which affect the products’ effectiveness and appearance.
Solution. Enercon’s Super Seal™ coupled with a sealing head specifically designed by application engineers to focus the sealing energy on the foil in the cap. Enercon was the only induction sealer supplier Belcorp found that could deliver consistent seals and adhered to their corporate quality standards.
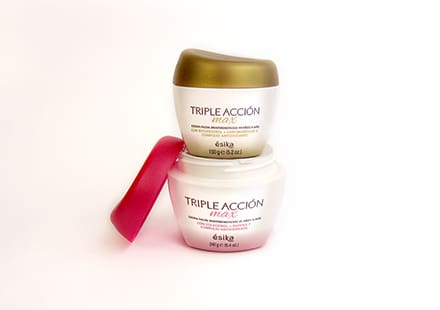
T. Marzetti – Simply Dressed
Challenge. Create a new package design that reflects the product’s clean and simple ingredients by eliminating the need for a shrink wrap over the closure, while establishing its own identity in a competitive marketplace.
Why Induction? Provide tamper evidence, preserve product’s freshness & provide an easy opening experience for consumers.
Solution. Enercon’s Super Seal™ induction sealer, with an energy efficient tunnel sealing head creates a clean hermetic seal for product freshness and tamper evidence.
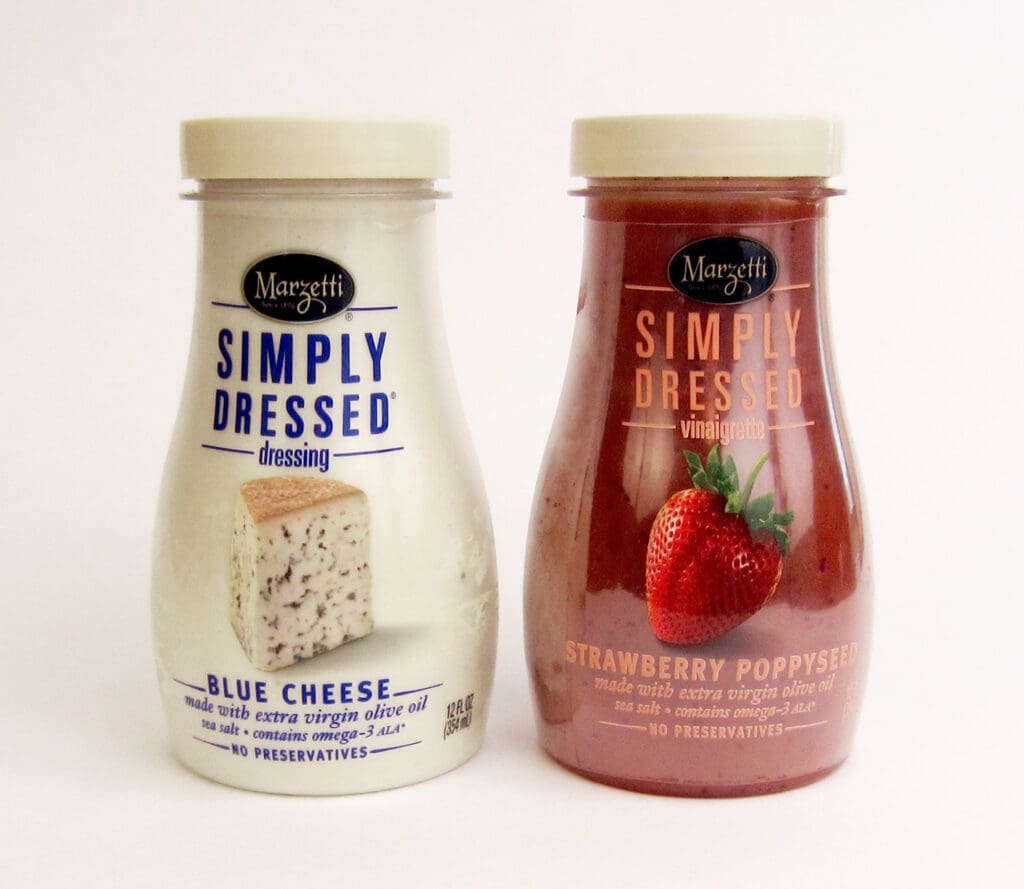
Zipz Wine – Single Serve Wine
Challenge. Switch from conduction sealing to induction sealing to alleviate seal failures.
Why Induction? Prevent leaks and oxygen migration to ensure product freshness while still providing an easy peel off solution for consumers.
Solution. Zipz designed a new container made with an oxygen-scavenging PET blend. They also incorporated threads in the closure which provides the pressure required for Enercon’s Super Seal™ Touch to create a hermetic seal expanding the shelf life to almost two years.
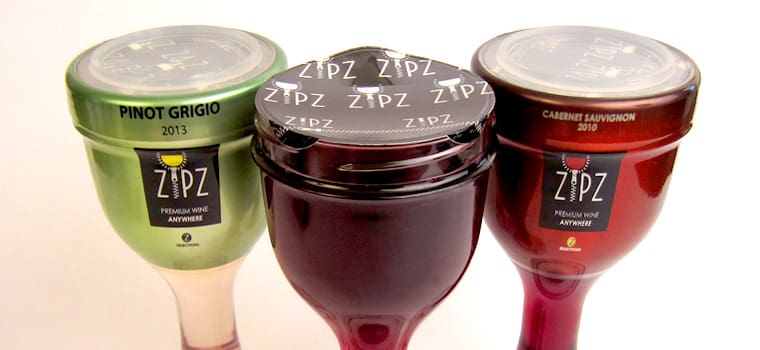
GreenBottle – Milk Bottle
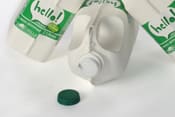
Challenge. To seal a new type of milk bottle that is completely recyclable. The outer layer is made of a paper shell with a thin plastic inner lining to hold the milk. The package requires sealing which must be accommodated on existing milk lines throughout the United Kingdom.
Why Induction? Preserve freshness, provide tamper evidence, prevent leaks and extend shelf life.
Solution. Enercon worked with the original container designer to ensure that the shape of the container opening is consistent with the traditional round UK milk bottles so that no sealing head changes would be required on UK bottling lines currently sealing with Enercon Super Seal and Super Seal Max induction sealers.
PepsiCo Tropicana Products Division – Tropicana Pure Premium
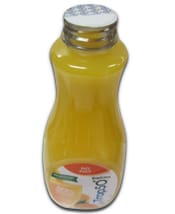
Challenge. Project “Inspiration” updated Tropicana Pure Premium packaging from gabletop cartons and white HDPE containers into four new PET bottles that have high appeal with consumers and environmentalists. The PET shift began in 2011, when a 59-oz ESL gabletop was replaced by an injection stretch blow molded (ISBM) PET featuring an induction seal.
Why Induction? Preserve freshness and prevent leaks.
Solution. High Speed Enercon Super Seal™ Max induction cap sealers with sealing heads optimized for the cap, liner and container configuration.
Justins Nut Butter – Sustainability
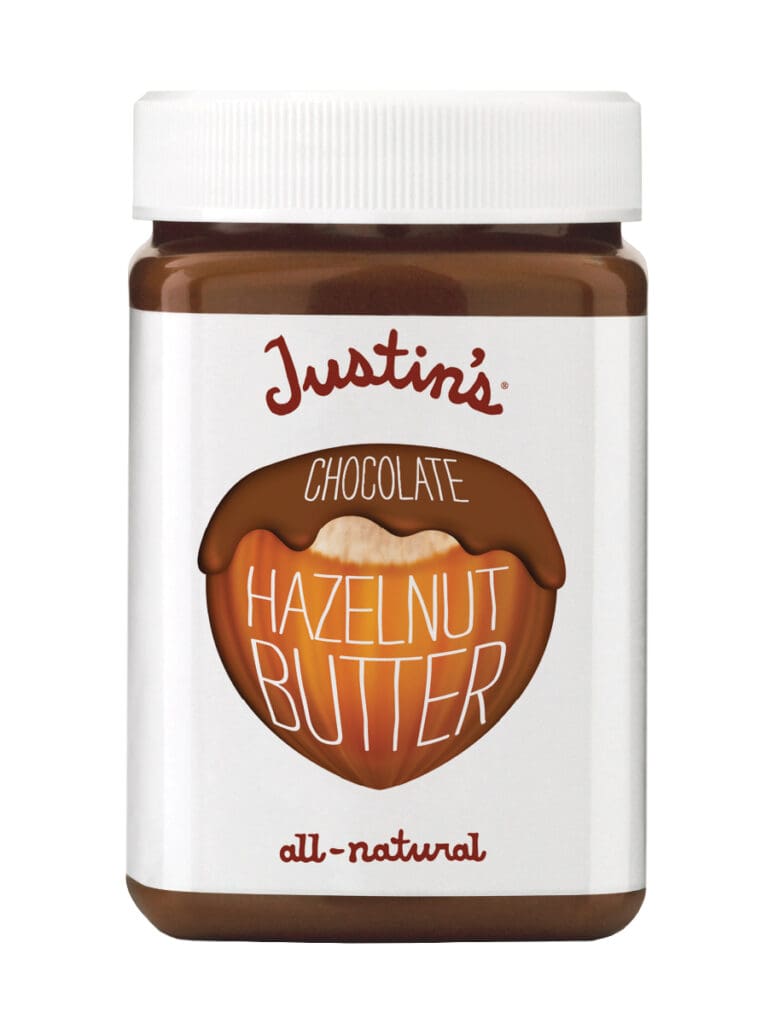
Challenge. Formulate all-natural nut butters & produce them in the most sustainable way possible. In addition to selecting packaging materials that are sustainable such as a new 16oz, PCR PET jar made from 100% recycled plastic, selecting packaging technologies to ensure product would not spoil prior to arriving in their customer’s homes.
Why Induction? Prevent oil seepage leaks, preserve freshness and extend shelf life.
Solution. Enercon Super Seal™ induction cap sealer with foil inspector and Enercon e-jector™ container rejection system
SaltWorks – Airtight Gourmet Packaging
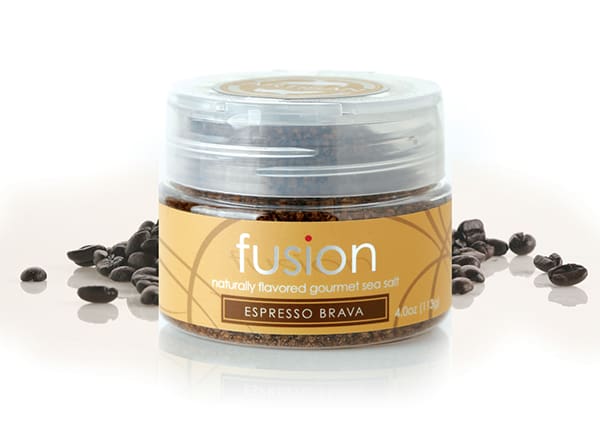
Challenge. Maintain product freshness for artesian gourmet salts packaged in PET containers ranging from 4oz to 32oz where pressure sensitive liners have failed.
Why Induction? An airtight seal was required to ensure the oxygen scavengers and desiccants inside the container performed properly. Induction provides a hermetic seal.
Solution. Enercon Super Seal cap sealer with All-in-One Universal sealing head.
KIK Custom Products – Top Job Cleaning Products
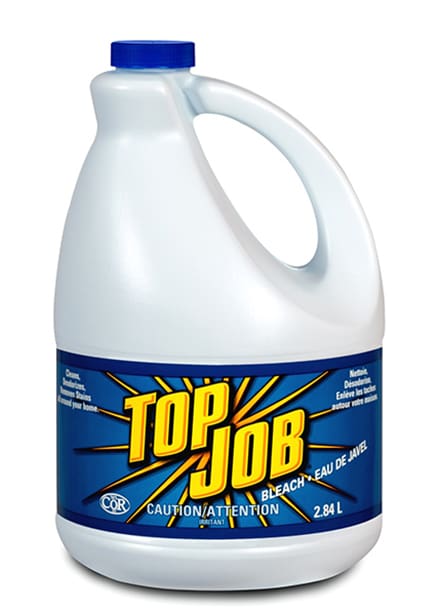
Challenge. Prevent container leaks and improve productivity on their high-speed chemical packaging lines sealing gallon HDPE containers with 43mm caps. Required greater consistency in induction sealing results and support from their suppliers.
Why Induction? Induction seals are a cost effective, reliable and production friendly technology designed to prevent leaks.
Solution. Switched to an Enercon Super Seal™ induction cap sealer with sealing head optimized for their application. They were impressed with performance and support and replaced all of their existing induction sealers with Enercon units. The most recent being a Super Seal™ Touch for increased sealing power and operator control.
Healthspan – Nutraceuticals
Challenge. Seal a flat container with a snap-on cap that lacks torque required for conventional induction sealing. This uniquely shaped container enables an online distributor of health pills to ship its product for the same price as a letter in the United Kingdom.
Why Induction? Tamper evidence, preserve freshness.
Solution. Enercon’s Super Seal™ induction sealer, with a tunnel sealing head, combined with a thick liner and additional support guides to ensure the package travels upright underneath the sealer.
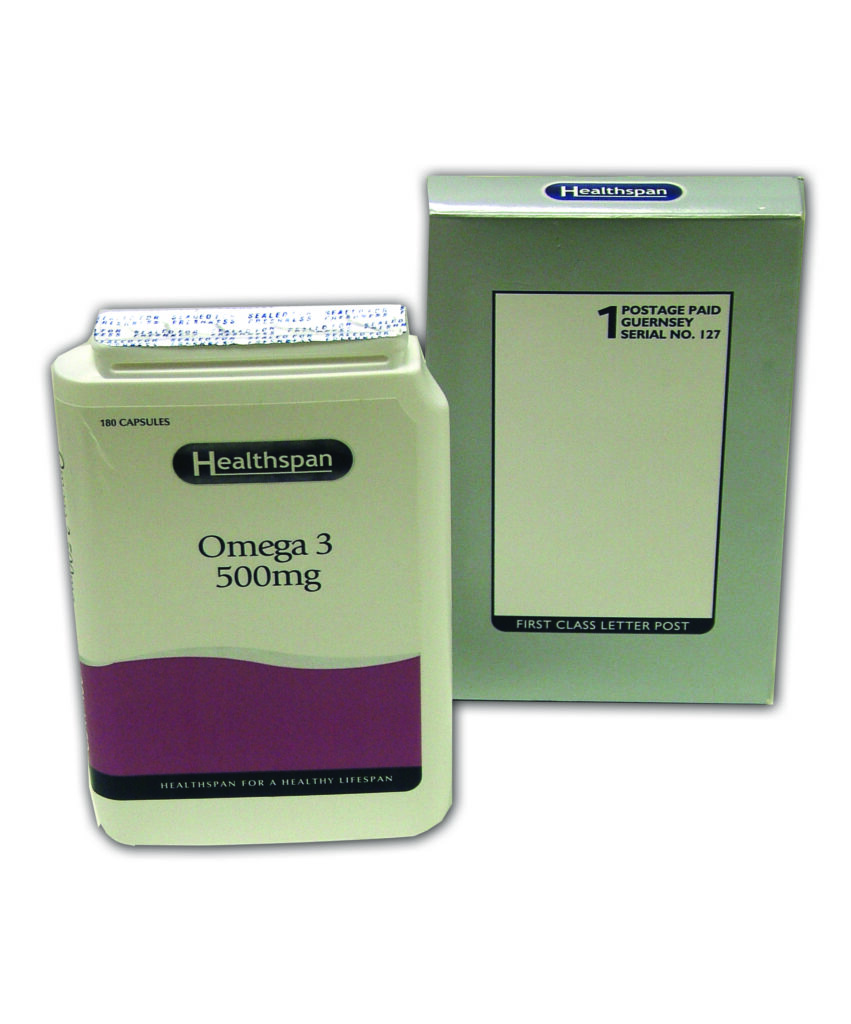
Pure Bioscience – Disinfectant
Challenge. Eliminate stalled bottles and melted caps from packaging line.
Why Induction? Prevent leaks and help ensure a two-year shelf life.
Solution. PURE Bioscience was the first packager to run production with the new Enercon Super Seal™ Touch. The cap inspection system eliminated the stalled bottles and melted caps. They are also taking advantage of advanced technology such as the intuitive touchscreen interface and integrated cap inspection sensors to meet their demand for optimum efficiency.
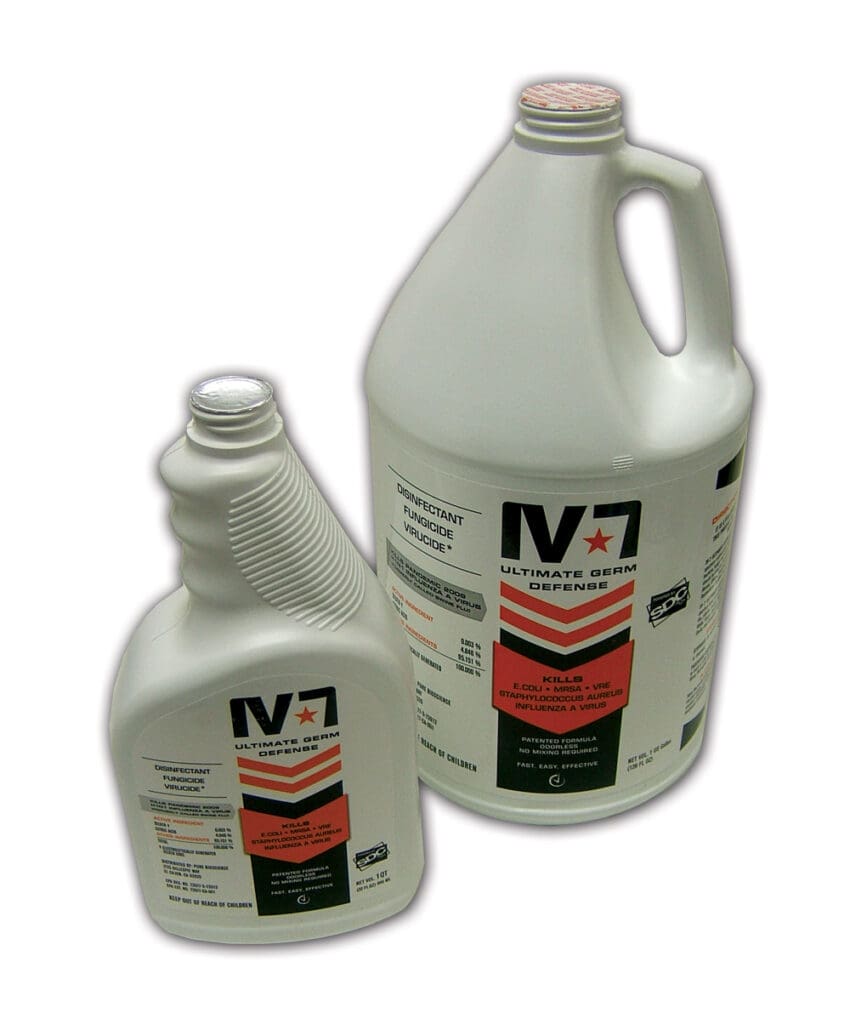
Floratine Products Group – Turf Chemicals
Challenge. Securely seal the container and prevent bloating and contracting of the container prior to use.
Why Induction? Prevent costly chemicals from leaking during shipping.
Solution. Performance Systematix and TricorBraun combined to find a perfect cap and liner combination while Enercon’s Super Seal™ provided the technology to seal the container. Performance Systematix’s vented Circumvent® foam liner and a vented Airfoil® heat induction seal allows the product to breathe without leaking. In addition, they also use a cap which contains a tiny 0.188″ hole allowing the container to vent while still repelling the liquid product.
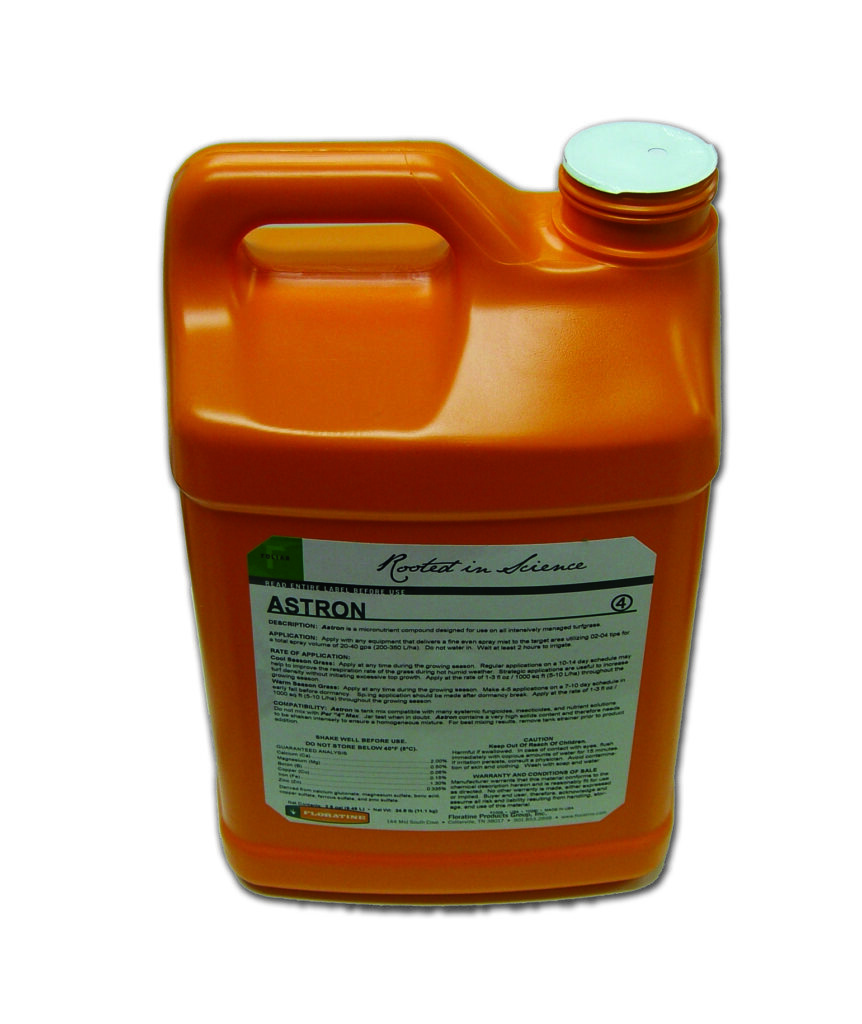
Charlotte Products – Disinfectant Wipes
Challenge. Large 130mm snap cap closure without threads to create required pressure for successful sealing.
Why Induction? Prevent wet wipes from drying out and disinfectant from leaking prior to use.
Solution. Combining a thicker induction liner with the snap cap to create enough pressure for the Enercon Super Seal™ with all-in-one universal sealing head to seal the bottle without the use of torque.
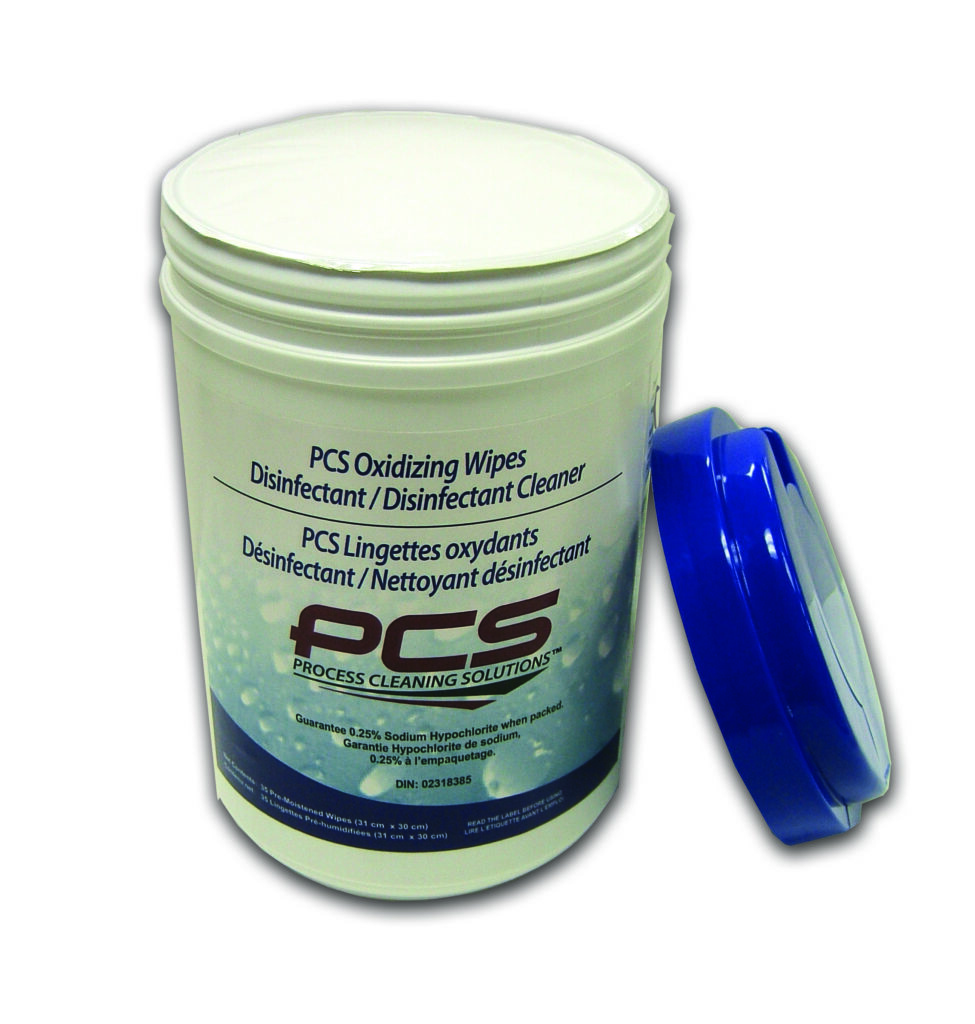
Nature Works – PLA Containers
Challenge. Create biodegradable plastic container from renewable plant sources. Ensure container can be induction sealed.
Why Induction? Preserve freshness, ensure tamper evidence and leak protection.
Solution. All testing conducted by Enercon has proven that these PLA containers can be sealed with existing Super Seal technology. Based on the cap size and line speed a variety of induction sealing head designs can be implemented.
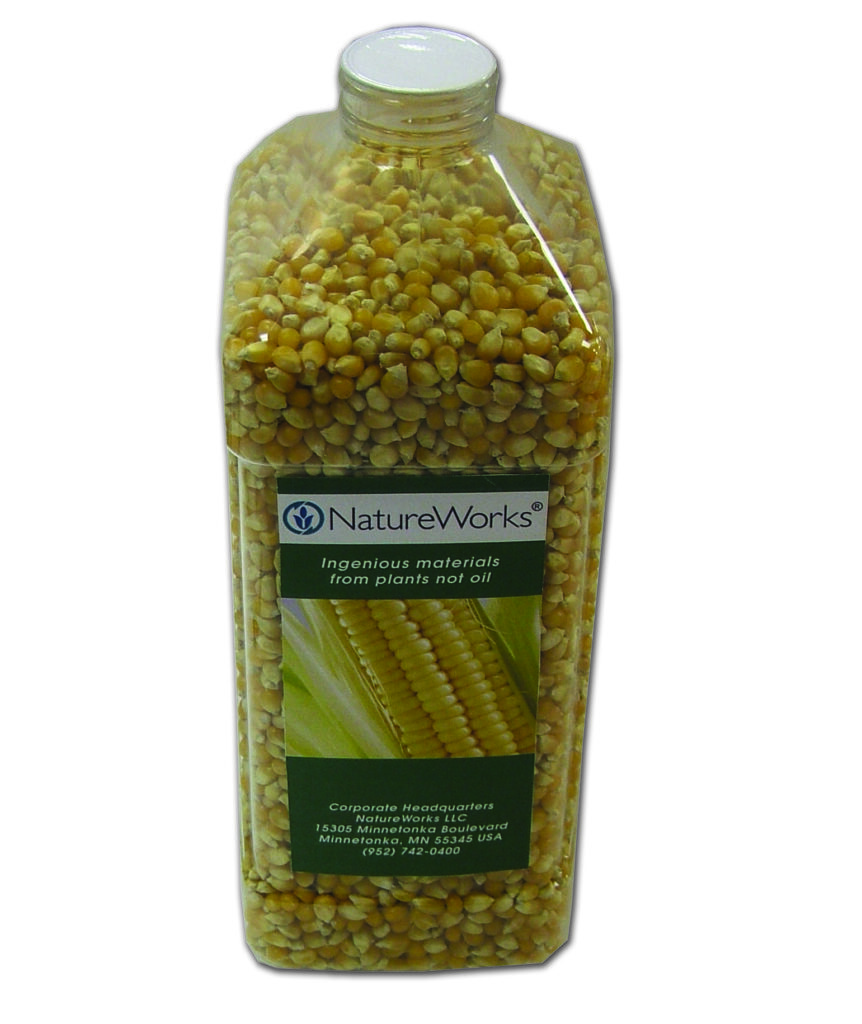
Y Water – Y Water, Inc. (USA)
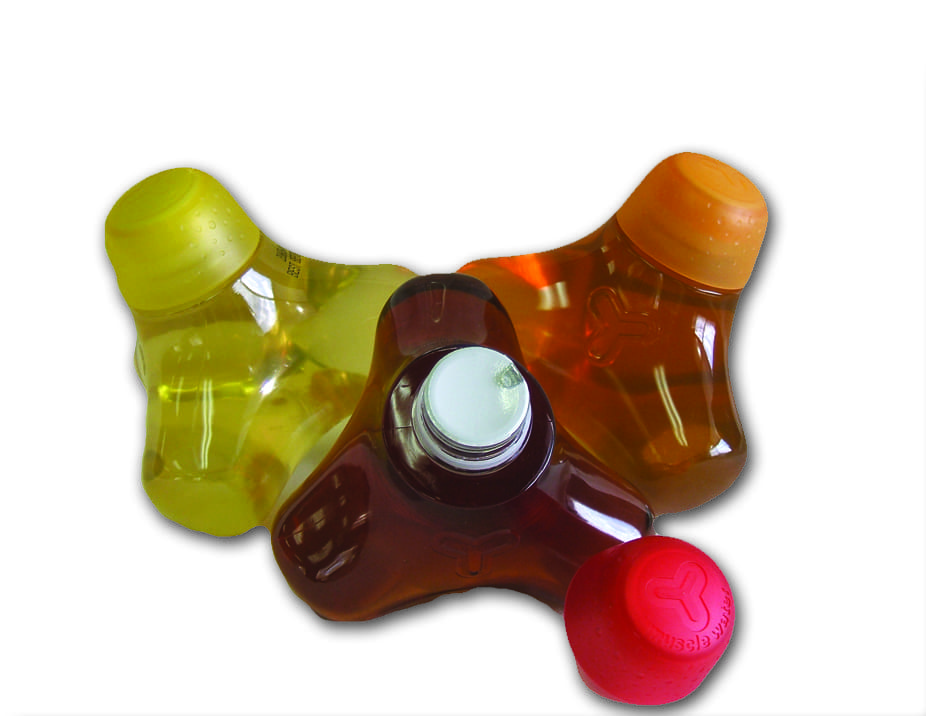
Challenge. Develop an innovative packaging design and concept while ensuring product freshness for the organic beverage. The creative design features Eastar™ EBO62, a unique copolyester resin which makes it 100% recyclable and reusable, doubling as a aftermarket toy.
Why Induction? Preserve freshness, instill tamper evidence and leak protection for the enriched water drink.
Solution. Enercon Super Seal™ induction cap sealer and deluxe cap inspection system. Energy efficient, tunnel sealing head creates a hermetic seal for product freshness and tamper evidence.
Whole Milk – Tesco Stores Ltd. (United Kingdom)
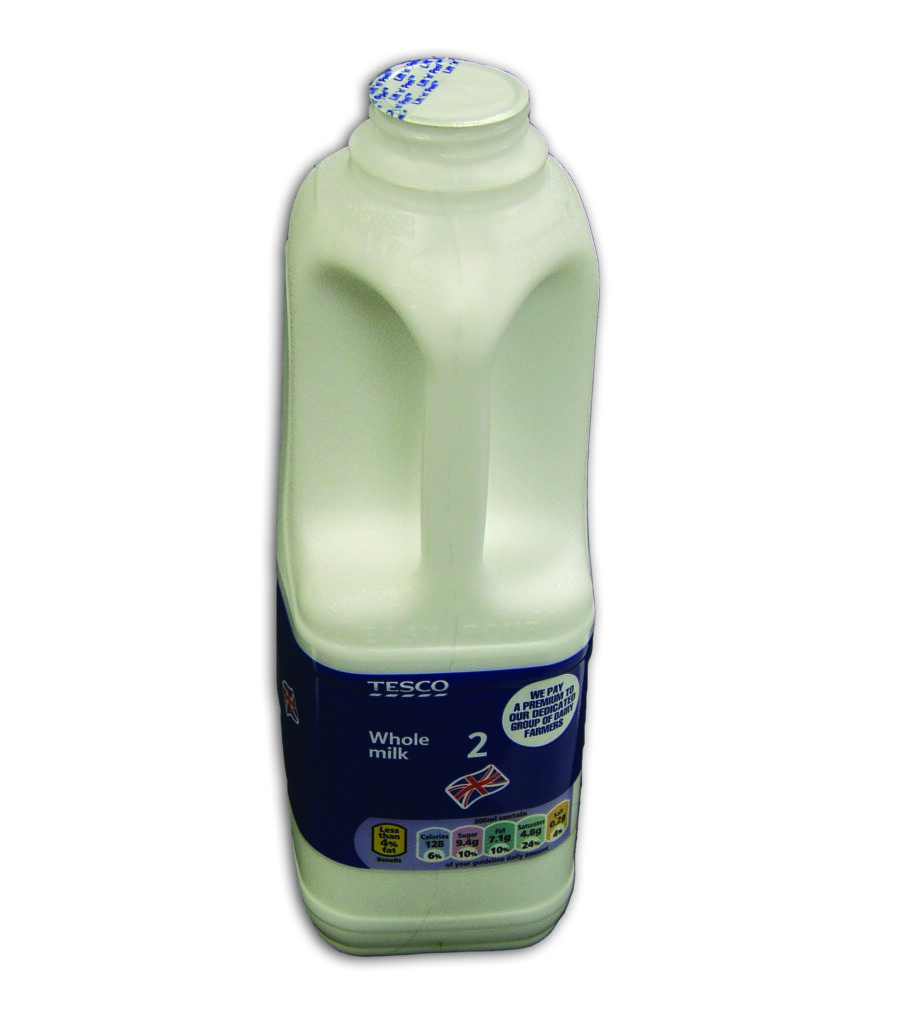
Challenge. The United Kingdom milk industry was encountering 1.5%- 2% product waste during transport and production of milk; the equivalent of 56 million liters of milk and 3.2 billion plastic bottles each year.
Why Induction? Prevent leaks, reduce waste and preserve freshness. Provides additional benefit of reducing pack weight by eliminating the need for a tear band and allowing for a thinning of the neck and shoulder of the bottle.
Solution. With Enercon’s Super Seal™ Max the UK dairy industry reduces waste and pack weight.
Horlicks™ – GlaxoSmithKline (United Kingdom)
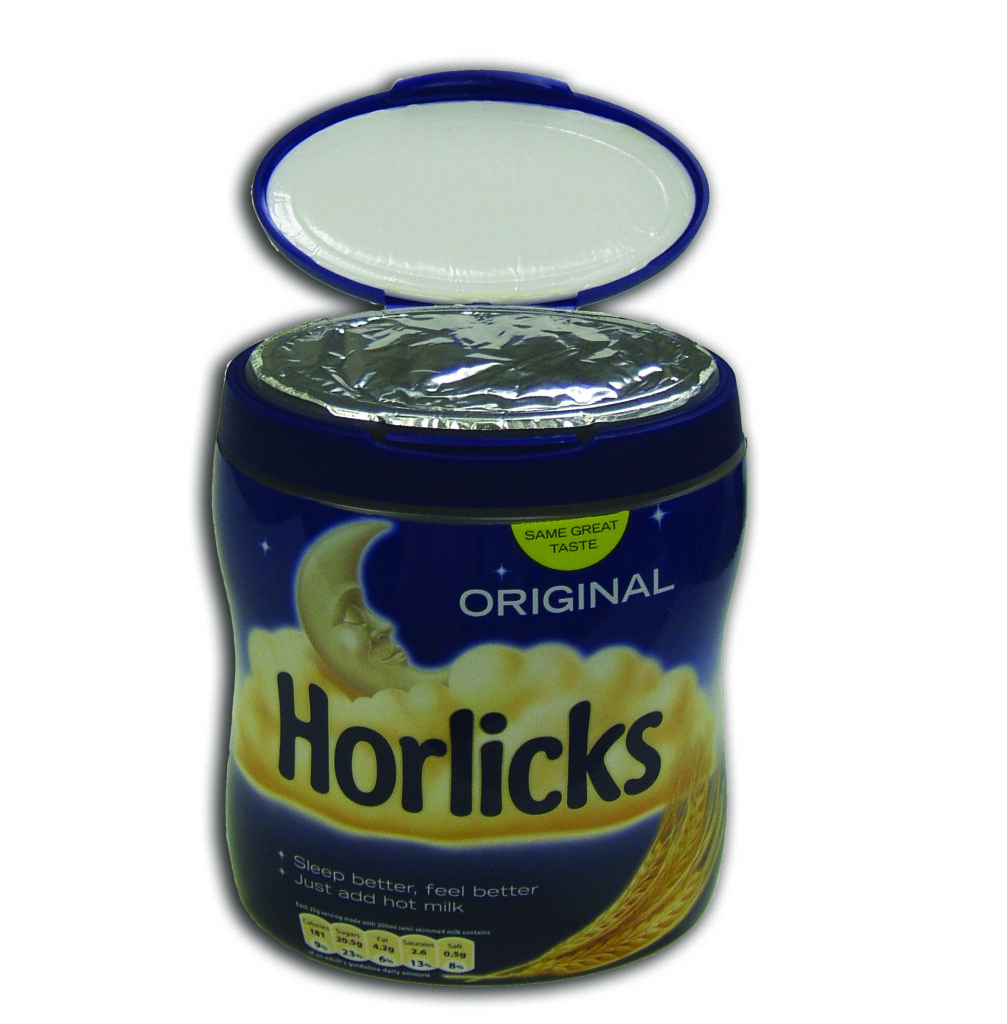
Challenge. The oval shape cap of this European household staple creates a challenge because induction sealing eddy currents travel in a circular path. The snap-on cap lacks torque required for conventional induction sealing.
Why Induction? Create an airtight seal to prevent product exposure to moisture.
Solution. Enercon engineers coupled their top belt sealer with the Super Seal™ Max. The top belt sealer is used to ensure that caps apply pressure on the foil during sealing and a customized coil for the Super Seal Max sealed the deal.
Ball Valve – Banjo Corporation (USA)
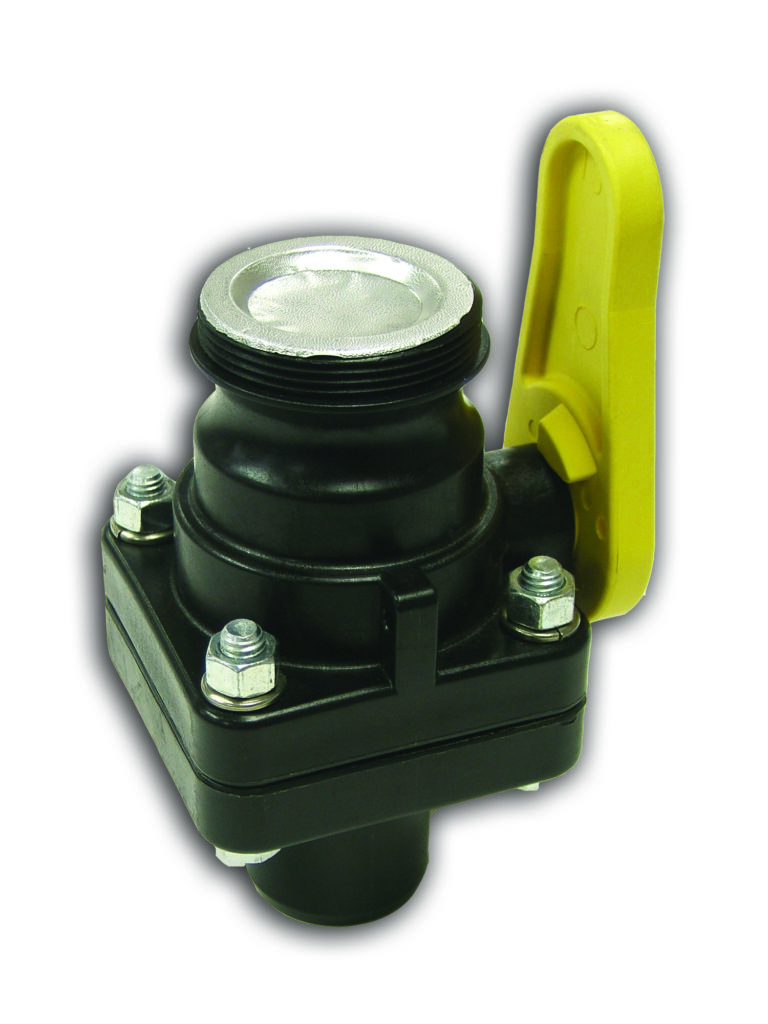
Challenge. Eliminate need for a cap.
Why Induction? The ball valve is used in water cubes at construction sites; a hermetic seal replaces the cap, reducing production costs and also keeping dirt and grime out of the water supply.
Solution. Banjo Corp. started with Enercon’s Pneumatic Jr. As business increased so did the need for faster production. Banjo upgraded to a customized linear indexing sealing system to meet their line speed requirements.
TUMS® – GlaxoSmithKline Beecham Consumer Healthcare
Challenge. Induction sealing is traditionally used to seal containers with round openings. Oval shaped foil creates a challenge since induction sealing eddy currents travel in a circular path. Standard snap on caps do no provide enough pressure on foil to achieve seal.
Why Induction? Preserve freshness, instill tamper evidence eliminating cumbersome and hard to maintain conduction sealing equipment.
Solution. Enercon Super Seal™ induction cap sealer with special sealing tunnel that directs the induction field across the oval foil for in-line production. Snap on cap features thicker pulpboard insert that applies required pressure on foil for sealing. The improved system created less downtime, less scrap, less conveyor, and higher speeds resulting in improved efficiences for GlaxoSmithKline Beecham Consumer Healthcare.
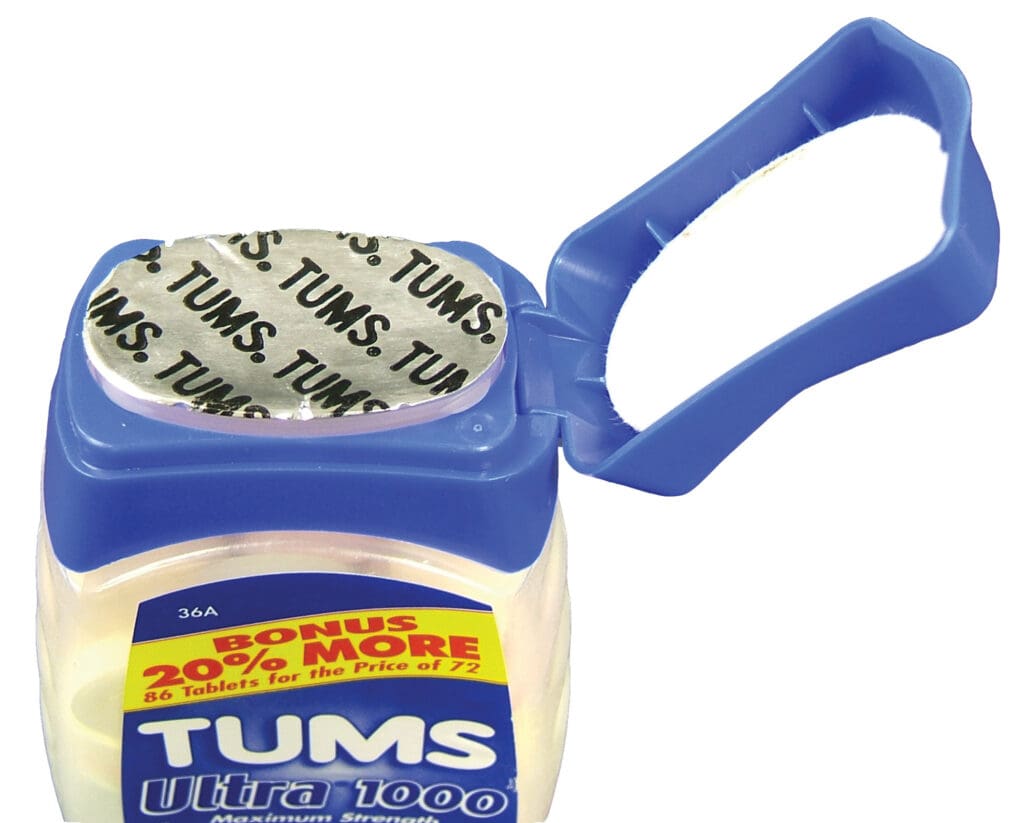
NESCAFE® – Societé des Produits Nestlé S.A.
Challenge. High speed line with new package design features cap and bottle profile with large air gap on sides and top of the induction seal. The strength of an induction field drops off proportionately to the square of the distance traveled which means this applicaiton presents and extreme challenge to deliever enough sealing energy to achieve a successful seal.
Why Induction? Preserve freshness and instill tamper evidence. The company already had an Enercon induction sealer.
Solution. Enercon’s application engineers reconfigured the internal design of a standard tunnel sealing head to specifically refocus the sealing energy to the position of the foil. The high-speed application also required the industry’s most powerful induction sealer: The Super Seal™ Max.
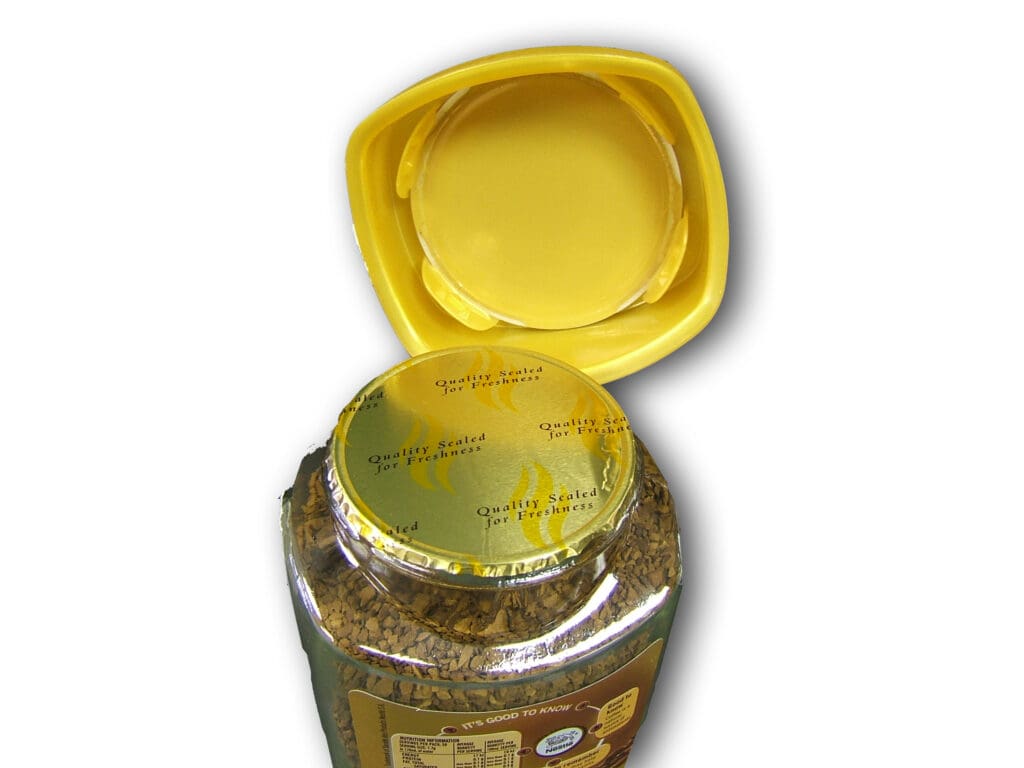
WILDCAT – Wildcat R/C Fuels, a division of CAE, INC.
Challenge. Seal two caps of differing heights with one induction sealer.
Why Induction? Prevent leaks and optimize throughput.
Solution. An Enercon Super Seal™ Max cap sealer with modified tunnel sealing head. The sealing head provides an extremely wide active sealing area to ensure successful sealing without the risk of overheating either seal.
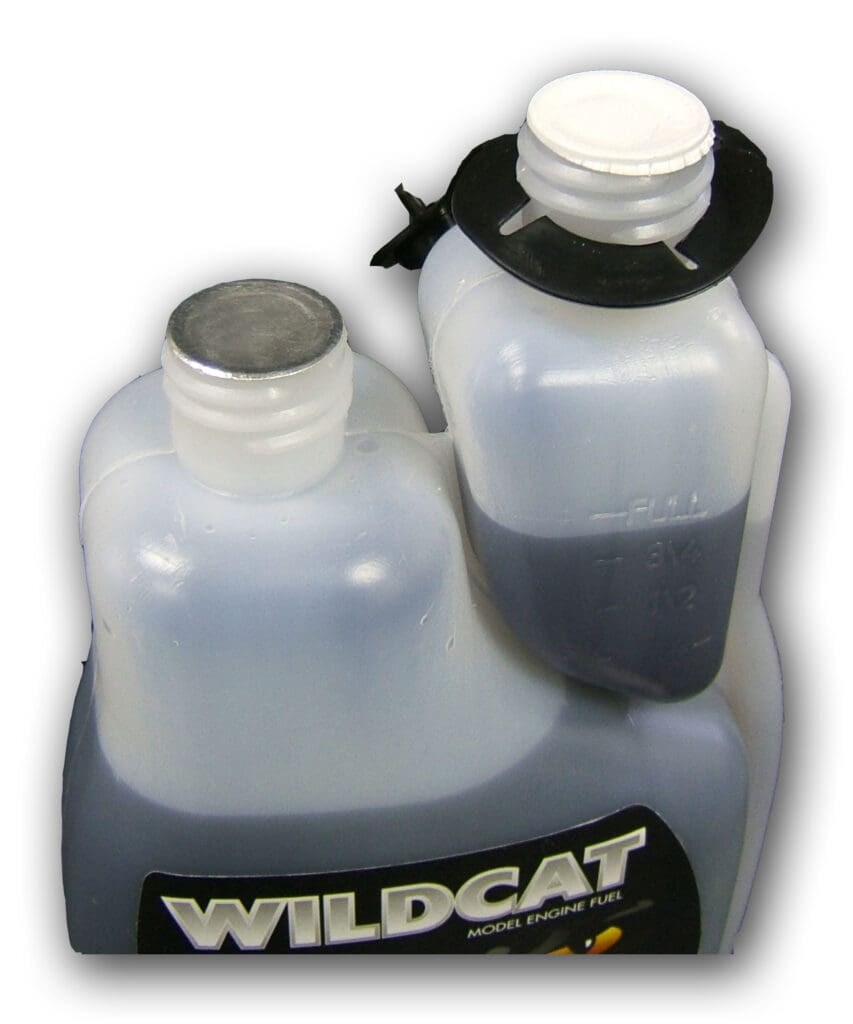
