Induction Seal Prevents Leaks During Shipment
Bryson Industries, Inc., Greensboro, NC, manufactures and packages a broad range of nontoxic household cleaners, including stainless steel polish, BBQ grill and grid cleaner, screen cleaner, and boat and patio furniture cleaner.
Based on customer feedback, Bryson learned that there was a good potential market for a “green” grill cleaner. The company experimented with various green grill cleaning blends for about five years before launching a non-toxic, biodegradable formula and a new, recyclable package design. The grill cleaner was a market success. So Bryson proceeded to roll out a series of other “green” household cleaning products over recent years. Twelve different Bryson products under five different brands are currently distributed though major retail outlets such as Best Buy, Kmart, Kroger, Lowe’s, Menards, Sears, Target, Wegman’s, AAFES, and Cabela’s.
Packaging uniformity
Bryson Industries COO Tommy Lancaster notes, “All these reformulated products now are packaged in similar containers to reduce raw material inventory hassles.” The firm selected PET, notes Lancaster, in the hope that consumers would put bottles in the well established PET recycle stream once the bottles are empty.
The PET bottles, from Pretium Packaging, are decorated with PET shrink sleeve labeling that is flexo printed in seven colors by CL&D Graphics. The labeling system eliminates glues and solvents.
Bottles are filled on a Model SK5000 overflow filling machine from Surekap. A six-spindle Model 5001 machine from KISS Packaging applies trigger-style caps supplied by Inmark.
But not all bottles get a trigger-style cap. Bottles sold through a television shopping network require an induction seal to offer leak protection, tamper evidence, and extended product shelf life. So for bottles destined for this distribution channel, a white 28/400 polypropylene cap with an induction seal liner is applied. These bottles then pass through an induction sealing machine supplied by Enercon Industries Corp. The Enercon system was purchased through Enercon distributor Packaging Machine Resources.
Lancaster says, “We were novices when it came to induction sealing. PMR’s Mark Pegram was extremely knowledgeable about the Enercon line of sealers. He was the primary reason we chose the system. And the expertise and education Enercon brought to the table was impeccable.”
After testing the induction sealing technology, Bryson decided to purchase an automatic Enercon Super Seal™ system with a deep tunnel sealing head. When Bryson packages products for the television shopping network, the cleaning products are capped and the trigger sprayer is packaged separately.
All products shipped for the television shopping network or any other customers that use UPS or Fedex are induction sealed for leak prevention with triggers included as separate packaging components. Products shipped by regular motor freight are shipped with the trigger spray mechanisms pre-installed in the bottles. For the bottles with the pre-installed triggers, capping speeds are about 60 bottles per minute. For the induction-sealed bottles with insertable spray triggers on the side, the speeds are about 100 bottles per minute.
Tommy Lancaster, Bryson Industries
Induction sealer benefits
According to Lancaster, “After receiving the new induction sealer, it took less than two hours from crate to running production. From concept to negotiations to installation, the process was flawless. What was so nice about the Enercon is that it came practically fully assembled. We were sealing bottles within an hour of receiving the machine.
As a matter of routine, says Lancaster, “We now test one out of every 60 induction seals and find less than .001 percent to not be sealed properly. And usually it’s through no fault of the induction sealer. We no longer get damage claims, so we’re able to keep our ‘on-time, every-time’ promise to our customers.
“Our broker, Mark Pegram with Packaging Machinery Resource, and Enercon’s Larry Sterna were very helpful during the training period. It was painless. I wish I could say that about all our equipment purchases. We could not be happier with our induction sealer investment.”
Portions of this article is Copyright Summit Publishing Co. All rights reserved. PACKAGING WORLD® Magazine is reprinted by permission of Summit Publishing Co. PACKAGING WORLD is a registered trademark of Summit Publishing Co.
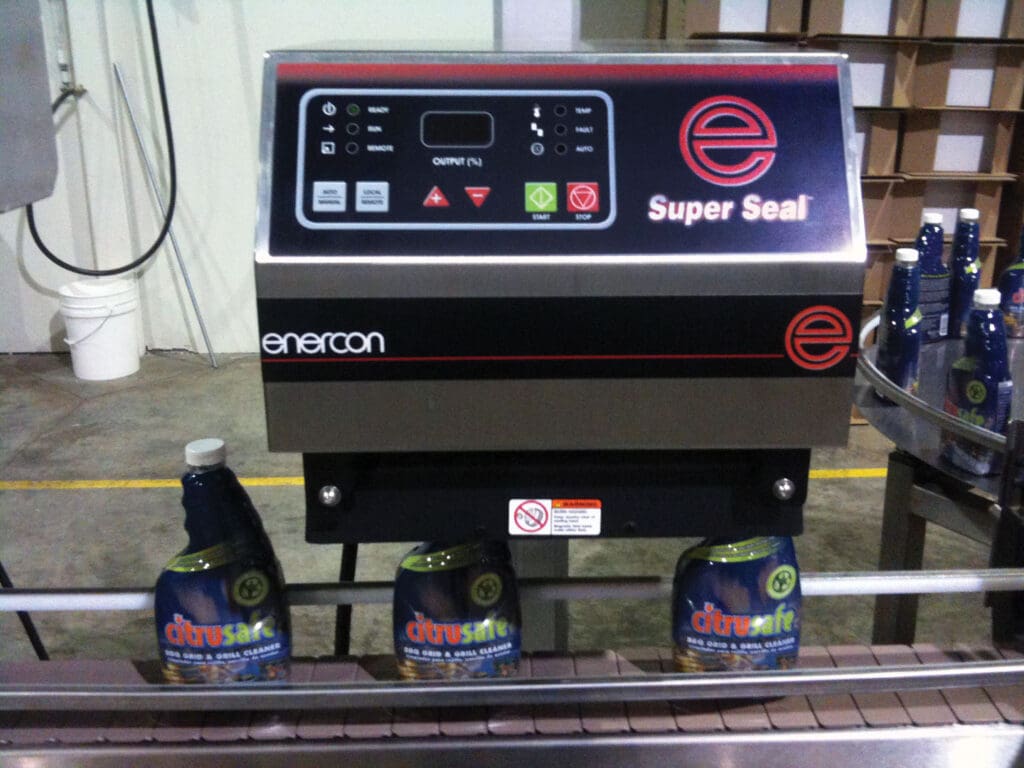