Induction Cap Sealing Basics
Induction sealing is a non-contact heating process that welds a foil laminate (called an inner-seal) to the lip of jars and bottles. The sealing process takes place after the filling and capping operation. Capped containers pass under an induction cap sealer mounted over a conveyor. The FDA recognizes induction sealing as an effective means of tamper evidence.
How Induction Sealing Works
The standard system has two main components, the power supply and the sealing head. The power supply is an electrical generator operating at medium to high frequencies. The sealing head is a plastic case that houses a conductor formed into a (inductive) coil. When energized by the power supply, the head produces an electromagnetic current, called an eddy current.
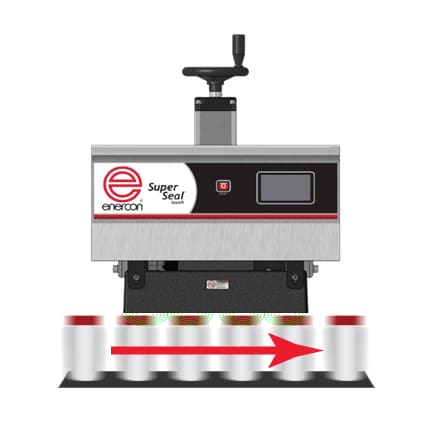
When capped the bottles enter this electromagnetic current, the foil of the inner-seal generates electrical resistance, heating the foil.
The hot foil in turn melts the polymer coating on the inner-seal. The heat, coupled with the pressure of the cap, causes the inner-seal to bond to the lip of the container.
The result is a hermetic seal.
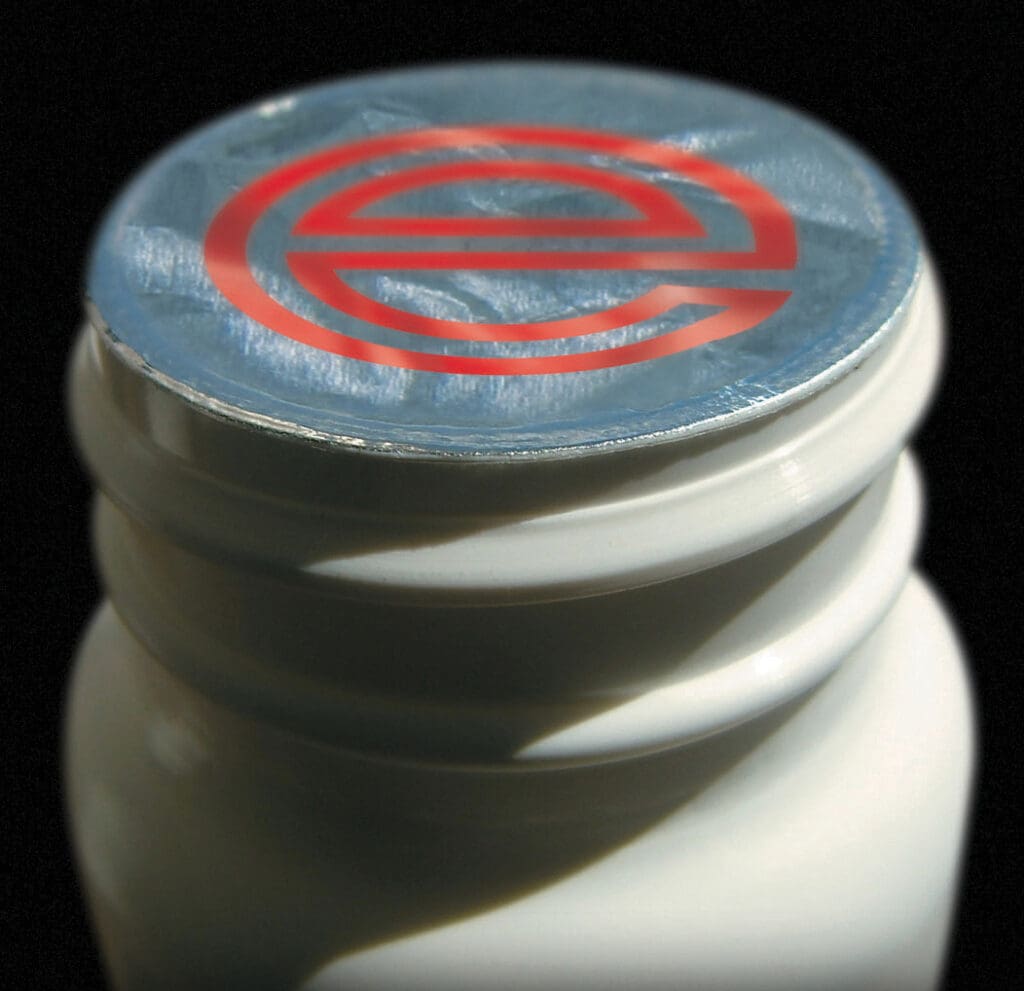
Strength of the Induction Field and Sealing Energy
The strength of the power supply depends on the size of the closure and the speed of the production line, while the design of the sealing head depends on the application. The two most common shapes are the flat head and tunnel head. A flat head disperses the magnetic field widely, allowing you to seal a large area. A tunnel head concentrates the magnetic field around the sides and above the cap. It usually provides a more uniform electromagnetic field and thus a more consistent seal.
Types of Induction Liners
The inner-seal you choose also depends on the application, and there are several combinations of inner-seal materials, including foam-backed and paper-backed foil laminates. The inner-seals may also include custom-printed logos, trademarks, or other messages, such as “sealed for freshness.” In cases where the inner-seal’s liner is a two-piece construction, the heated foil also melts the wax layer. The wax is absorbed into the inner-seal’s pulp board, thus releasing the foil from the pulp board.
When necessary, the inner-seals are very tenacious, forcing you to destroy them to reach the container’s contents. In other cases the seals are easily peeled. Which inner-seal is right for your product depends on several variables. To find the right inner-seal, we recommend that you consult with your cap supplier or with the inner-seal manufacturers.
Types Of Containers That Can Be Sealed
Plastic containers with screw-on plastic caps are easiest to seal. Other applications may take a little more work. It is also possible to seal glass containers and to seal with metal caps, but both applications pose challenges. Glass containers may need to be treated before the lip of the container will accept a seal. And while it’s technically feasible, induction sealing with a metal cap requires further consideration. The sealing equipment will heat both the inner-seal foil and the metal cap, and the metal cap will stay hot for a while – presenting a possible safety problem. In fact, hot metal caps could also melt the plastic threads of a container.
Selecting The Right Cap Sealer, Power Level & Sealing Head
The three major factors to consider when selecting an induction sealer are the size and type of the cap as well as the speed of the production line. You should also consider the type and composition of the container, the type-of inner-seal material used, and the product’s properties. As mentioned earlier, plastic bottles with plastic caps are the easiest to seal.
Many people mistakenly believe that there is a relationship between the kilowatt rating of the power supply and its sealing capability. While it’s generally true that the higher kilowatt rating, the more powerful the system, more kilowatts do not necessarily lead to a higher sealing rate. The kilowatt rating is only part of the equation. The real secret to creating fast, efficient, and consistent seals is the energy transfer from the power supply to the sealing head.
All sealing heads are not created equal, and designing an induction coil for each head is both an art and a science. If you don’t have the correct coil design, increasing the power only wastes energy. It will not significantly improve the quality or rate of sealing.
Reputable suppliers will emphasize sealing performance and system efficiency rather than kilowatt ratings. We’ve seen many sealing systems rate at 1 or 2 kilowatts that outperformed systems with higher kilowatt ratings. Don’t be fooled by a supplier who tells you the more kilowatts lead to better induction sealing. It is simply not true.
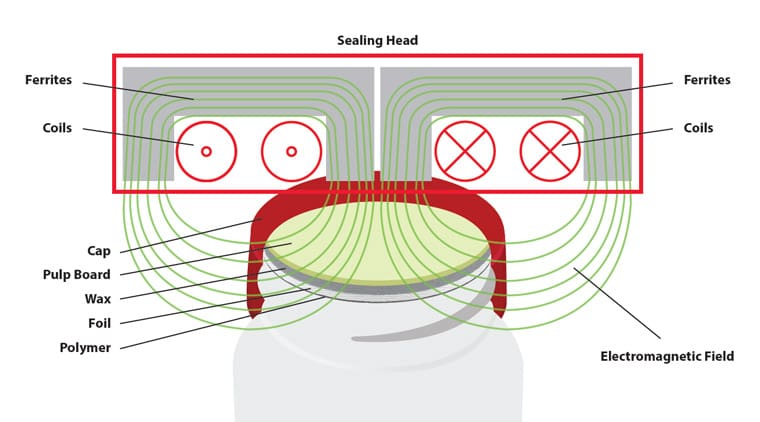