TIDI Relies on Enercon for Custom & Standard Corona Treating Solutions
Support Caregivers. Protect Patients. These four powerful words provide the mission for TIDI Products LLC employees. So when the company corona treats LDPE on their blown film lines the stakes are high. TIDI’s customers depend on their hospital gowns and related products to protect them. This means their extrusion and converting lines need to perform at the highest levels. When it comes to corona treating, TIDI has found Enercon to be their vendor of choice for both custom and standard projects. Its most recent project involved replacing a problematic corona treater on a blown film line. In the process, TIDI learned that Enercon delivers on four words of their own: Reliability. Efficiency. Customization. Support.
Reliability
“We run these blown film lines 24/7. They supply the entire plant. If we have extended downtime on these lines it can create issues for our entire production schedule,” says Project Engineer Aaron Riddle. Corona treatment at the time of extrusion is a critical requirement for successful TPT (Tissue /Paper /Tissue) lamination.
Over the years, TIDI has been replacing older corona treating power supplies in the plant with Enercon units. “We have a lot of experience with Enercon power supplies. They are bulletproof, very reliable, and amazingly easy to troubleshoot compared to our older systems,” says Paul Hallman, Electrical Project Technician. This was the initial reason the company chose to work with Enercon on the new project. Along the way, they learned about many more advantages of working with Enercon.
For TIDI’s blown film application Enercon specified a system with stainless steel electrodes. This provided immediate results. Their previous system from a different vendor had cheaper electrodes made from aluminum. Paul Hallman explains, “The other corona treater required a lot of maintenance. The electrodes oxidized and a white powder was created which was an ongoing problem.” With the Enercon corona treater this problem has gone away.
“Our team was really impressed with how Enercon’s application expertise and technology combined for such an efficient system design. Even performing routine maintenance is an efficiency improvement. The pivoting and hinged design of the Enercon electrode assembly is vastly superior to anything we’ve worked with before. The access for cleaning is excellent.”
Paul Hallman, Electrical Project Technician at TIDI
Efficiency
Enercon’s application expertise also contributed to ensuring TIDI’s new system was properly sized for their applications. For the 1600mm wide LDPE blown film line, Enercon specified 6-inch ceramic covered ground rolls. This was a pleasant surprise for TIDI. The older system had incredibly large rolls weighing 800 pounds each while the new ones were 75% lighter.
“Our team was really impressed with how Enercon’s application expertise and technology combined for such an efficient system design. Even performing routine maintenance is an efficiency improvement. The pivoting and hinged design of the Enercon electrode assembly is vastly superior to anything we’ve worked with before. The access for cleaning is excellent,” says Hallman.
Customization
The treater being replaced was located near the top of the blown film tower. It was out of sight and out of mind; so, the TIDI team talked with Enercon about locating the new treater on the first mezzanine. Since there had not been a treater in that spot previously the companies had to coordinate a custom design for the treater. “Enercon custom designed this treater much narrower than their standard two sided treater. Their engineering team did a great job making this fit,” notes Hallman. “Enercon was very responsive and understood what we needed, right down to the space required for wiring pathways and available locations for the high voltage transformers and power supplies,” explains Riddle. With this configuration both electrode assemblies are accessible from a single side.
TIDI added LED indicator lights at the station to allow operators on the mezzanine to quickly identify the corona treater’s current station status. And a plexiglass cover is used to allow line operators and maintenance personnel to inspect high voltage connections and verify if the roll is spinning.
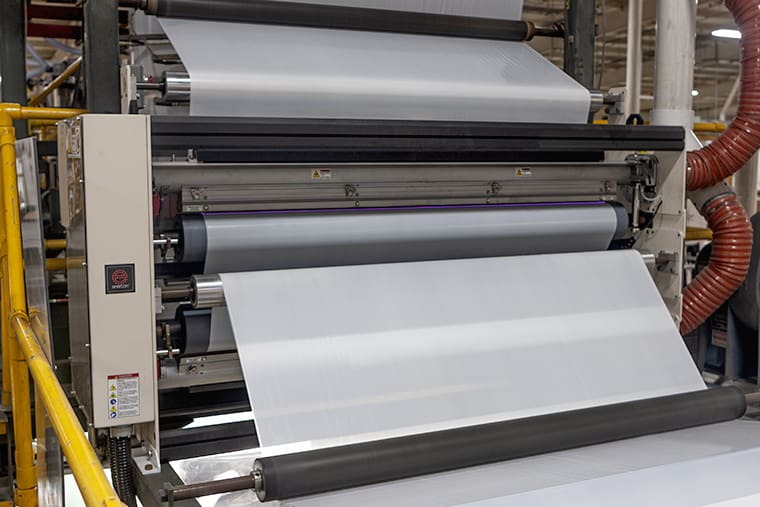
“Enercon was very responsive and understood what we needed, right down to the space required for wiring pathways and available locations for the high voltage transformers and power supplies.”
Aaron Riddle, Project Engineer at TIDI
Support
Aaron and Paul worked together with Enercon from the concept of the project through installation and both were impressed with the support from Enercon. At the beginning of the project, the team sited Enercon Sales Manager Aaron Hootkin with providing insights on how to best achieve their goals of relocating the treater position and was very responsive getting them in touch with the technical team at Enercon. “I hate to say it, but we’ve had other vendors who just aren’t responsive. And sometimes when their service personnel visits, they just shrug their shoulders without being able to offer a solution,” explains Paul. “With Enercon it’s always a purposeful visit.”
Before the corona treater was shipped, TIDI sent a team to Enercon for final approval and training. A cross functional team including line operators, maintenance, and engineering attended. The free training program put on by Enercon helped the company get off to a fast start with the system. Additional resources such as free on-line training webinars and surface treating handbooks also contributed to a successful start-up.
“From start to finish, we couldn’t imagine this project being any more efficient or smoother,” reflects Hallman. And with their customers depending on them, that’s just what the doctor ordered.
