Corona Treatment Builds Better Bonds for BOPP Laminates at Prestige Pak
In 1967, Biaxially oriented polypropylene (BOPP) wasn’t regarded as a popular substrate for flexographic printing. James Kuber saw an opportunity and launched flexible-packaging converter Prestige-Pak (now CP Flexible Packaging) in Fond du Lac, WI. Decades later, President Vince Kuber continues to invest in equipment as he sees store shelves filled with products packaged in laminated, flexible bags and pouches.
Most recently Prestige-Pak decided to ride the wave with a 59-in. Super Simplex solventless laminator from Nordmeccanica NA. “The laminator came swimming in from Italy,” Kuber jokes,” and was used for a demonstration in Long Island, NY, before it was shipped to our facility. This is a new direction for us. With better barrier properties, longer shelf life, and the ability to keep oxygen out of the package, laminating has come a long way in a very short amount of time.”
Shortly after the laminator installation, Prestige-Pak added two 59-in.-wide Enercon Universal roll corona treaters to ensure lamination strength and improve dyne levels.
After careful analysis of all of the proposals presented, the decision was a no brainer, says Kuber. “The logistics of having Enercon in our backyard, and the added value just made more sense.
“As the guy who writes the check, what was important to me was not to be nickeled and dimed at every turn,” he continues. “We had one company that offered us a Cadillac —what we needed, and another that offered us a stripped-down Chevy. By the time we added options to try to bring the Chevy up to the level of the Cadillac, we would have spent 25-percent more to get it there.”
Adds Prestige-Pak plant manager Gregg Leisten, “In looking at competitive proposals, something didn’t seem right. We had the feeling we weren’t comparing apples to apples.”
With the addition of the corona treaters, the primary and secondary webs on the laminator are treated to dyne levels close to 44. Each treater features a Compak 2000 7.5-kW power supply with a watt-density control function that automatically adjusts the treater power level to match the web speed. This reduces waste and ensures consistency.
Enercon’s treater design is mechanically and electrically integrated specifically for the Nordmeccanica laminator, which allowed installation to take place in hours rather than days. The laminator was also pre-drilled for easy fitting of the treaters. “Set-up was plug-and-play,” says Leisten. “With all the pre-engineering involved, I wouldn’t expect anything less.”
Predominately serving the snack-foods packaging market, Prestige-Pak is capable of laminating plastic to foil and plastic to paper. “We serve a niche market,” says Kuber. “We have mastered short-runs and the business model. Our changeovers are as quick as a pit crew.”
Forming a bond
Prestige-Pak decided it was a worthwhile investment to add similar Enercon High-Definition corona treaters to its 8-color CI-flexo press from Paper Converting Machine Co. This addition is expected to improve print repeatability and eliminate pinholing defects.
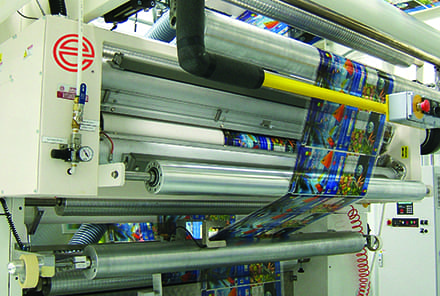