Experience Produces Results at Legacy Flexo with Flexographic Printing and Corona Treatment
In 2011, Dan Aberly and Mark Carrick established Legacy Flexo Corporation with a vision to provide high quality flexographic printing services for film, nonwovens and paper. The two flexographic printing veterans had industry experience, but needed to build a company from the ground up. Their first major investment was a used Comexi FX2108. The 8 color 67” wide press provided them with the capabilities to get their business off the ground. Since then, the Legacy Flexo Team has expanded at an aggressive pace adding four more presses in seven years.
According to Alex Schaefer, Legacy Flexo’s Maintenance and Safety Manager, the company’s success is fueled by its aggressive use of their equipment, “We push these systems 24/7 to get the most productivity possible out of each of them.” In addition to the Comexi press, their line-up of presses includes a PCMC ProVision, Fischer & Krecke 36S, PCMC FusionMAX and PCMC Fusion C. All but the PCMC Fusion C were purchased used.
Corona Treating Integral to Printing Success
When purchasing used presses, the buyer inherits the equipment as is. The company’s first press came with an Enercon treater that had been poorly maintained. Schaefer and Legacy Flexo’s team worked with Enercon to refurbish the now 20-year-old treater into working condition. Schaefer says, “We got to know the Enercon team really well during this process. They are a remarkable group who support their equipment and know their applications.”
Their next used press, the PCMC Pro-Vision, did not come with a corona treater. Initially Legacy Flexo printed with solvent inks on the press. “We wanted to eliminate the cost of the solvent inks so we contacted Enercon for another corona treater. They were able to recommend a treater to meet our needs and mount seamlessly into the PCMC press.”
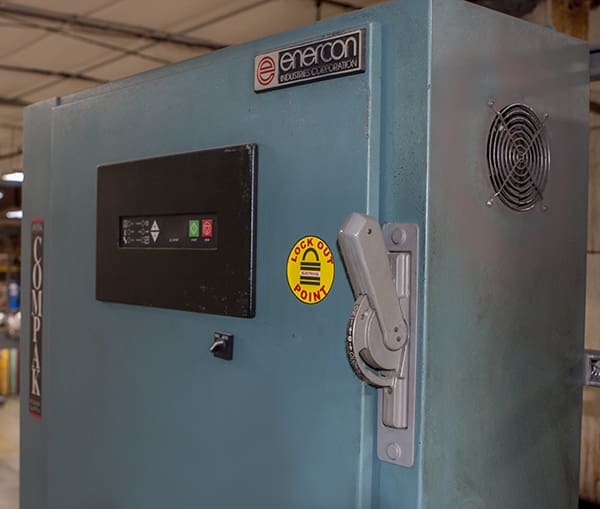
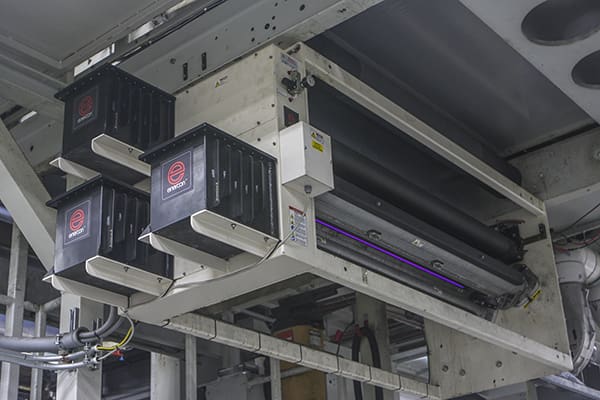
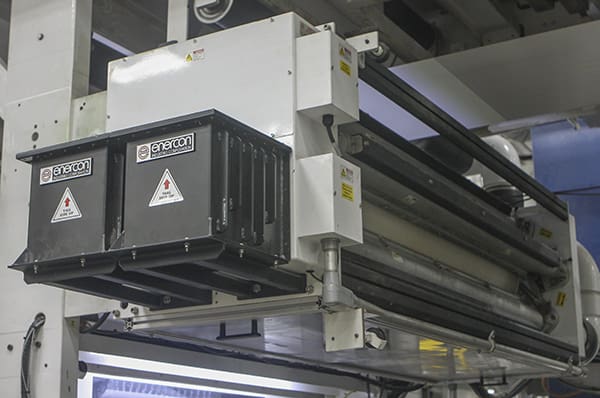
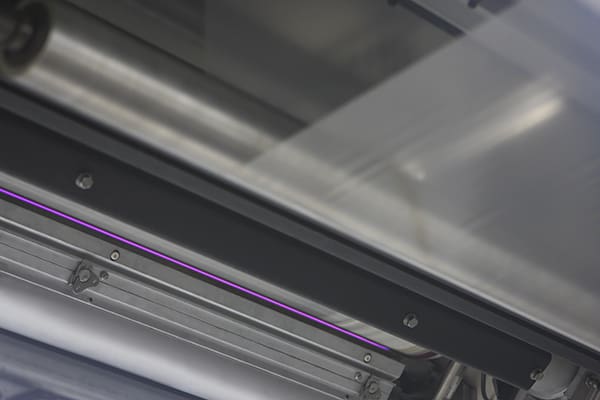
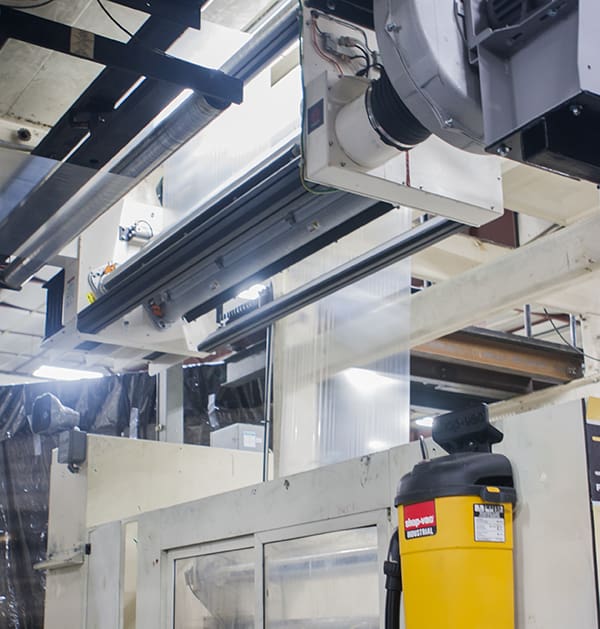
The flexographic printer depends on surface treatment to ensure ink adhesion. “Even though we purchase pretreated film, we bump treat to ensure we prepare the surface for optimal adhesion,” says Schaefer.
Their third used press is a Fischer & Krecke 36S which is capable of speeds up to 3,280 fpm. For this system Legacy Flexo purchased a new corona treater from Enercon capable of delivering high watt density levels at high speeds. The system features multiple electrode assemblies and Enercon’s power supply design the Compak™ ProFlex. The power supply provides an easy to use touchscreen interface that provides operators with operating control and advanced system diagnostics.
With 20kw of power, the treater is capable of handling the most demanding polyethylene and polypropylene flexographic printing applications.
Getting installations right & keeping up with maintenance
The ability to incrementally grow the business with used presses running 24/7 requires an understanding of how to properly install and maintain the systems. Legacy Flexo is vigilant when it comes to these types of details. Schaefer’s team worked closely with Enercon to ensure best practices were followed when installing the systems including configuring the exhaust runs.
Selecting the right materials, limiting the length and number of elbows in the exhaust ducting are key to ensuring proper air flow. Exhaust air removes ozone and other by products from the work area as well as cooling the electrodes. Maintenance is equally important and Schaefer’s team mounted a Shop Vac® to each press so they could efficiently clean the electrodes assemblies. This commitment minimizes downtime when the presses should be fulfilling customer orders.
“We push these systems 24/7 to get the most productivity possible out of each of them.”
Alex Schaefer, Legacy Flexo’s Maintenance and Safety Manager
More presses and more growth
As Legacy Flexo has grown their commitment to their customers, quality printing and fast turnaround has remained a constant. In fact, that’s what’s driving additional investments. To expand their capabilities they recently added a used PCMC FusionMAX and a new PCMC Fusion C.
The investment in their first new press was the result of rapid customer demand for their printing services. The press happened to be immediately available as it was a demo model. The PCMC Fusion C increased Legacy Flexo’s capacity and provides fast make-ready and waste-saving features.
The current facility is 107,000 ft², but plans are already underway to expand to 180,000 ft² by 2019. Legacy Flexo is focused on growing and increasing capacity while maintaining their ability to offer their customers cost savings and high levels of service and quality.
Alex Schaefer concludes, “We’ve built a really strong foundation at Legacy Flexo and our customers have confidence in us. We are flexographic printing specialists. Our team is experienced and we rely on key partners like Enercon to ensure we continue to deliver the best flexographic printing services possible.”
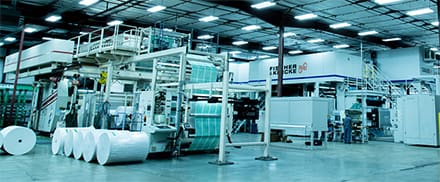