How Flame Control Systems Optimize Treatment
Flame is the world’s original surface treater and is commonly used on extrusion coating lines, paperboard processing and foil cleaning applications. If you haven’t considered a flame treater in some time you will be surprised at today’s advanced combustion control options and new high velocity burners that deliver effective and repeatable treatment.
Managing the chemistry of your flame treater is key to ensuring consistent treatment results. If the air/ gas ratio mixtures are allowed to fluctuate without compensation, your treatment results may vary. Enercon offers several different flame control technologies, and this article will provide insights regarding the benefits of each.
Manual Adjustment
The most basic and economic control technology is manual adjustment. This control configuration measures both air and gas volume being fed to the burner by means of visual meters that must be verified by the user. This is an open loop system. This type of control is only recommended for applications where the power level remains consistent and the material being treated is not sensitive to changes in power density or air/gas ratios for successful treatment.
Volumetric Flow Control
Measures both the air and gas volume being fed to the burner, but does not compensate for changes in temperature or atmospheric pressure. Most applications will not be affected by these small changes. It automatically adjusts both air and gas flows based on values input by the user of air flow rate and air/gas ratio making it a closed loop system.
Mass Flow Control
Mass flow control systems measure both the air and gas volume being fed to the burner and compensates for changes in temperature and atmospheric pressure for the most accurate and repeatable flame chemistry. It is a closed loop system that automatically adjusts both air and gas flows based on values input by the user of air flow rate and air/gas ratio.
Oxygen Analyzer
An oxygen analyzer may be used in conjunction with a mass flow or volumetric flow control system. An oxygen analyzer takes a sample of the air gas ratio, combusts it, and then reads the amount of oxygen leftover. This feedback can be used to determine the air gas ratio. When used with a mass or volumetric flow system, the flow feedback for the gas is replaced by an oxygen analyzer.
Some considerations when using an oxygen analyzer include:
- Slower response time. Samples are taken downstream of the mixing venturi, get combusted, then analyzed, changes to the air/gas ratio are much slower so over correction is possible.
- Indirect measurement. Both the standard mass flow and volumetric flow systems directly measure the entire volume being sent to the burner. The oxygen analyzer is just taking a small sample and is assumed to be representative of the mixture sent to the burner.
- Unable to measure a rich condition. An oxygen analyzer is incapable of measuring the degree of a rich condition. Due to the nature of a rich condition (not enough oxygen to fully combust all of the gas) there is little to no excess oxygen to measure. The standard mass flow and volumetric flow systems are capable of detecting and regulating ratios across the entire range of combustible mixtures.
- More maintenance. The oxygen analyzer requires periodic calibration to maintain reliable air gas ratio control.
- Higher Cost. The oxygen analyzer option is an added cost over the standard systems.
Contact Enercon today to learn more about how these flame control systems will ensure consistent treatment for your application.
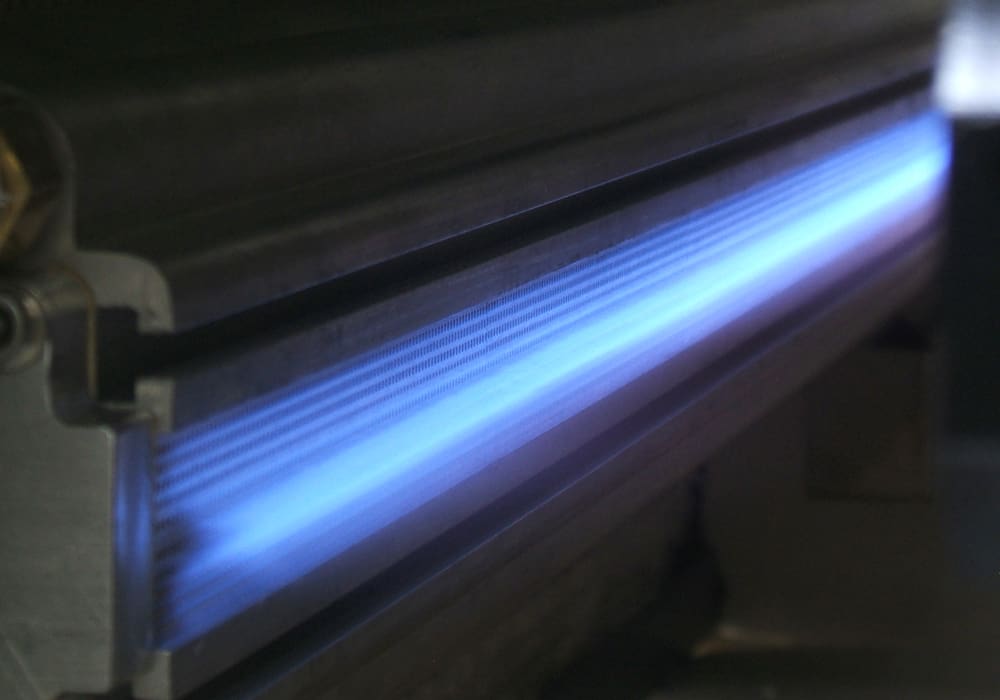