Improve Lamination Adhesion with Surface Treating
For many industrial applications, the use of a single ply of a material does not provide all of the critical properties required for the optimal performance of a product. In these cases, a composite of two or more layers of material can provide this required performance. A common method of creating such a composite is to laminate various materials to each other with an adhesive. This solution is commonly employed in the packaging industry where the end-products require more than one functional property, such as high tensile strength or low gas permeability. The laminate construction can become complex due to the characteristic of the specific application. A typical laminate used in the medical packaging industry, for example, may be a lamination using films of polyester / polyethylene / metal foil / polyethylene. Surface treating solutions such as corona treaters, atmospheric plasma systems and flame treaters are often used to improve lamination adhesion.
Laminating adhesives are available in a variety of technologies, viscosities, and solids concentrations. However, the primary objective of these adhesives is to maximize peel strength within the bond. For lamination adhesion to plastics for example, peel strength is determined by 1) chemical bonds, and 2) plasticity. The reactivity of the adhesive chemicals, the entanglement of the plastic (polymer) chains with the adhesive, and the mechanical properties of the adhesive are key to achieving a successful lamination bond.
Laminating adhesives can be classified as follows:
- Solvent-Based (Polyether urethane, Polyester, Acrylic)
- Solventless (100% solids – Polyether urethane, Polyester Urethane)
- Water-Based (Polyether urethane, Acrylic)
- Radiation Curable (100% solids)
- Combination radiation curable
Each category has a number of applicable base polymers and a wide variety of formulation possibilities. The adhesive in a laminate is often chosen for more than only its bonding ability. In addition to bonding the substrates together for the life of the laminate, the adhesive might need to perform other functions that are necessary to the success of the final product. These additional functions could include: increased or decreased gas permeability, flame resistance, thermoforming capability, optical clarity, electrical insulation or conductivity, chemical and heat resistance, etc. The specific formulation will heavily depend on the nature of the laminating process employed, the nature of the film substrate, and the final physical properties desired.
These adhesive chemistries all require preparation of the substrate surfaces (one or both) by surface treatment. Proper surface preparations will help ensure a long lasting bond and prevent delamination from occurring. In order for the adhesive to effectively wet and bond to the substrate, the adhesive should have a surface tension that is lower than the surface tension of the substrate being coated by approximately 10 dynes/cm. Surface preparation by corona, flame or atmospheric plasma can each individually improve the efficiency of the lamination process. For example, in-line surface treatment to 48-50 dynes/cm is suggested for best results with solventless and radiation-curable adhesives, whereby 40-44 dynes/cm can be sufficient for solvent-based lamination adhesives. Treatment levels lower than these benchmarks usually results in inconsistent and poor adhesion.
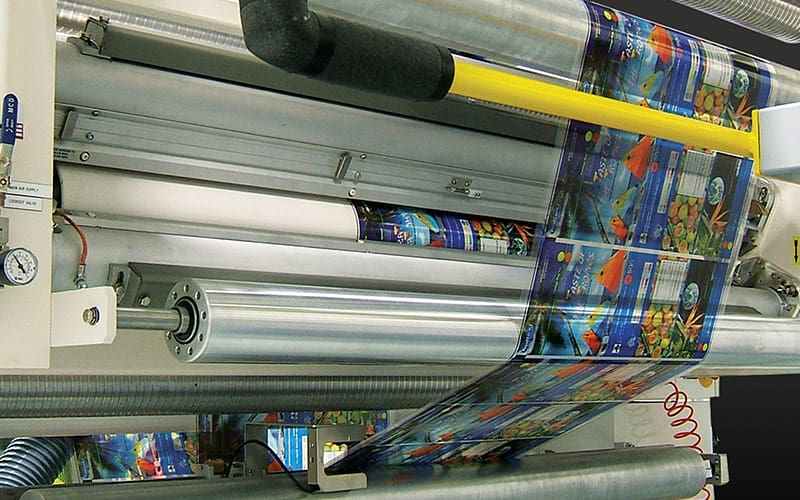