Options for Surface Treating Extruded Film
Traditionally, film extrusion lines utilize a metal electrode and covered roll configuration. However, there are exceptions. Some companies choose a Bare Roll system to eliminate any roll covering concerns. While others have selected a new Plasma3™ atmospheric plasma system for their extruded film applications.
Fixed or segmented applications?
For simple applications that do not require lane treating, a fixed width metal tube electrode provides adequate treatment levels. For demanding fixed width applications, a powerful metal fin electrode is ideal.
Another option for applications that require higher kW power and large ground rolls is Enercon’s Universal treating system. This system features a comparably smaller base roll than a metal electrode system and features ceramic electrode technology with a proprietary ceramic roll covering.
Lane treatment requires a segmented electrode. There are two styles of segmented electrodes; flip segments and push/pull segments. Flip segments provide an economical solution for low power and less demanding applications.
Operator-friendly push/pull segments provide positive control over a wide range of web path options.
Stations with push segments can also handle greater amounts of power and are therefore better suited to lines that operate at moderate and higher line speeds.
Aluminum or stainless steel?
Whether you select flip segments or push segments, it’s important to understand the benefits of stainless steel over aluminum. Aluminum material is low in cost and an easy material to fabricate, so it could be argued that aluminum is an excellent choice for electrode construction. That is until one looks at what happens to an aluminum electrode during use.
The corona process creates a harsh environment for the electrode. Aluminum will oxidize over time causing the segments to stick together. This problem causes areas of treatment or non-treatment along the width of the electrode. Also, aluminum is a good conductor of heat. Corona electrodes operate in temperatures of 150 to 180 degrees C. At these temperatures, it is very difficult for the aluminum electrode to remain parallel to the ground roll. Once the aluminum electrode warps the air gap between the face of the electrode and the roll surface changes and so does the corona and ultimately the dyne level.
It is for these reasons we recommend stainless steel electrodes as they offer superior performance, durability and lower cost over the life of the treater.
In many cases, it’s the old “You can pay me now or pay me later” syndrome. So be sure to evaluate your budget, short/long term needs, and the importance of reliability and consistent performance.
For more information on selecting the right electrode for your application contact us today.
Watch an on demand webinar or read the now available white paper: “Optimizing your film extrusion line for surface treatment“.
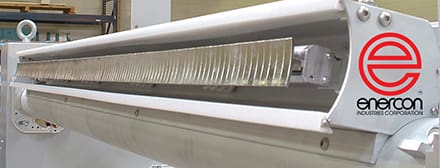