Put your rubber mallet and 2×4 away if you’re serious about high performance covered roll systems.
Let’s talk about covered-roll systems for blown and cast film surface treating. Our observations are made based on my visits to dozens of plants in the past year. I’ve worked with some of the best in the field and I’ve found a common denominator that they all share. They not only understand their equipment, but they also understand their processes.
Believe it or not, we’ve been in plants where a rubber mallet and a 2×4 are required tools for adjusting the segments on a corona treater. If you don’t understand why this isn’t a good idea, call us (262-255-6070) and we’d be happy to discuss the importance of a consistent air gap.
To be fair, it’s really not the fault of the poor guy who has to make the adjustment. When an aluminum electrode is used to generate corona, the inevitable chemical result is aluminum-oxide. Aluminum-oxide is a nasty compound which makes electrode segments stick. Most high-performance lines rely on the more stable stainless-steel electrodes.
Don’t be fooled by aluminium coatings
Some operations, who have worn their mallet out, finally break down and purchase a new treater. Some try their luck with an aluminum electrode that has been coated. To their credit, many treater manufacturers have tried to develop coatings to avoid corrosion. Anodized aluminum, Teflon coatings and hard coatings work great. Great for about six months that is. After these coatings break down, and they will, it’s back to the tool crib for a new mallet.
Another problem with aluminum electrodes is that they are less conductive to heat than stainless steel electrodes. This makes it virtually impossible to maintain a consistent air gap. Inconsistent air gaps produce inconsistent treatment and translate into scrap material.
There’s a place and a budget for surface treaters with aluminum electrodes. But stainless steel electrodes offer superior performance, durability and lower cost over the life of the treater. It’s important that you evaluate your budget, short/long term needs, and the importance of reliability and consistent performance. In many cases, it’s the old “You can pay me now or pay me later” syndrome.
Hot Tip: Two Power Supplies are Better than One
Most blown or cast film treating systems are designed with two electrode stations regulated by a single power supply. Some forward-thinking converters have realized that using individual power supplies for each station provides more process control.
By nature, or science if you will, electricity follows the path of least resistance. And while your corona treater leaves Enercon with precision air gap alignment, over time the air gaps will ultimatley vary (especially if you hit the segments with a mallet and 2×4).
In the days of low frequency power supplies, air gap wasn’t as critical. The advantages of today’s high frequency power supplies are many, but their performance related to air gap is more sensitive than their predecessors. As an example: if you have a 5-kW power supply, the station with the smaller air gap will deliver more corona than the other station. For some applications, this creates no real difference, but for others it could mean the difference between scrap and saleable material.
If blocking is a problem, two power supplies can be used to creatively reduce or eliminate the problem. If you set one power supply at a slightly lower, but acceptable power level, the two sides will have slightly different dyne levels. Blocking is a less likely occurance with differential treatment.
Be honest and provide meaningful operating data.
We’ve found many companies request a surface treater that can run at 400 fpm. After visiting their facility, we often find that the company never runs at 400 fpm, and their most typical runs are much slower. In fact, some operations regularly run at speeds less than 100 fpm with a system designed for 400 fpm.
From sports cars to high-speed boats, and yes corona treaters, all high performance equipment have ideal operating ranges. A treater optimized for 400 fpm will not perform as well at 25 fpm. If you really need a treater that can efficiently handle a wide operating range let us know up front. We’ve developed some special configurations that are geared towards operating over wide ranges (mallet not included).
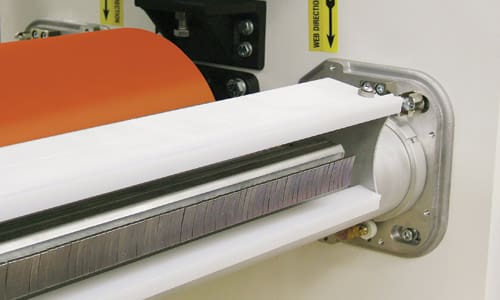