Solvent-Based Printing Improved with Corona Treatment
Enercon has the fortunate opportunity to share ideas with solvent-based printers from around the globe on an almost daily basis. To say the world of printing has changed in the last 15 years is an understatement.
More complex film compositions, more intricate graphic designs, shorter press runs, faster production speeds, greater scrutiny with higher expectations on print quality have changed the rules and the conventional wisdom regarding surface treatment and solvent-based printing.
As one long time press supervisor recently said, “It used to be that the corona treater was an inexpensive insurance policy against film defects. We knew we could run without the treater, but if something went wrong with the material, the losses on a large run could be staggering.”
His point is well-taken. And for many, the corona treater is still viewed as an economic insurance policy and not a necessity. But that’s old school thinking, and ready or not, new school is now in session.
Many printers are learning that there are several advantages to be gained from adding in-line surface treatment to their process. These printers are innovative leaders that are proactive in taking control of their printing processes.
The Benefits of Treating
The key equation for successful printing is the difference in the surface energy between the ink and the substrate. If the surface energy of the ink is higher than that of the substrate, it will not “wet out” and the resulting adhesion and print quality will be poor. Solvent-based inks have a relatively low surface energy and are primarily used in conjunction with a variety of pretreated substrates.
Let’s take a look at four benefits of surface treating pre-treated material on solvent presses.
1. Improved Print Quality
Today’s film manufacturers do a fantastic job of ensuring the pre-treated film you purchase meets specifications. But in the real world, variations cannot be eliminated. Complex film compositions with additives can be particularly troublesome.
Presses that combine the benefits of solvent inks with the control of corona treating optimize their process.
A surface treater puts the control in your hands. Over time, print quality will be better on a press with in-line surface treating than without. Ink adhesion and wetting will be improve, and pinholing in solid colors and gradients can be eliminated. Most importantly you’ll have optimal control over your process.
2. Greater Inventory Flexibility
Surface treatment on all substrates, including the pretreated material that you buy, has a life expectancy. You may have noticed “fresh-film” produces better results than “aged-film.” A corona treater allows you to bump treat “aged-film” thus creating a wider window for your usable inventory.
3. Faster Press Speeds
If the rest of your press can handle it, a corona treater will allow you to run even tough jobs faster.
4. Reduced Waste
With a corona treater, less scrap is practically guaranteed. Controlling the surface energy of your substrate ensures reliable printing.
Some of you may still not be convinced that the corona treater is anything more than an insurance policy for your solvent press. Others who understand the dynamics of their printing process will recognize otherwise. The old rules of thumb have changed. Those printers who take advantage of tools (such as a corona treater) that place more control in their hands will have the edge over their competition.
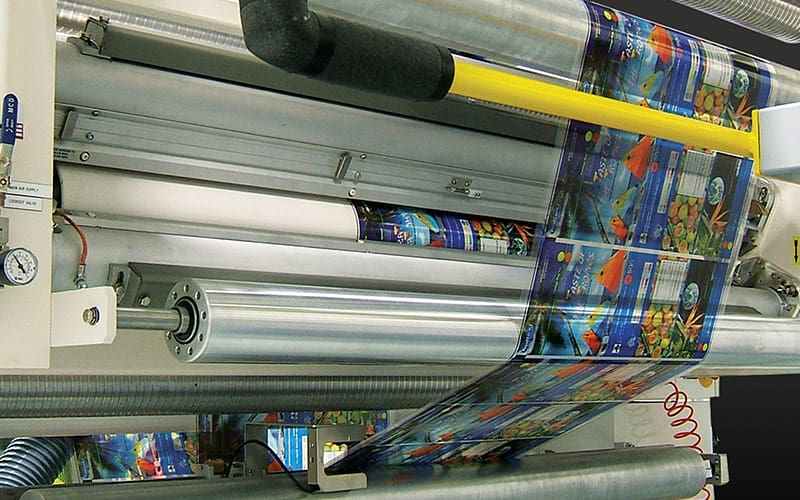