Windmöller & Hölscher Printing Technologies
Enercon Interviewed Klaus Kleemann, VP of Sales at W&H North America
Enercon partners with international OEMs to ensure our corona treating solutions fit seamlessly with their latest equipment designs. We’re pleased to share with you some of the latest innovations in printing from W&H.
What options do you have for remote support for your customers?
For over 25 years, W&H has pioneered the use of remote support tools. Our Information & Diagnostic Center (IDC) is available 24 x 7 x 365. This means that when our customers are having any sort of issues with their W&H machinery, they can reach an engineer specialized in their equipment, who can diagnose and help resolve problems. More than 90% of machine issues are solved this way.
Globally, W&H has offered all our customers a service called Visual Assistance, free-of-charge. It is an app which lets a technician view the external working environment of a machine through an operator’s smart phone. This enables W&H field technicians around the world to provide expert support, even in cases where our international customers are unable to receive visitors due to travel restrictions.
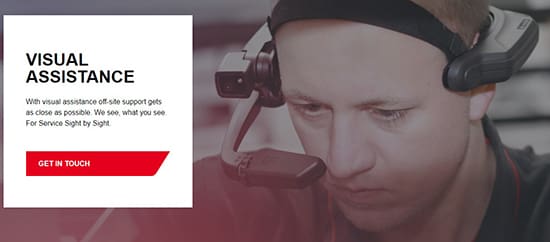
What are some of the latest printing technologies that you have introduced?
Automation for Sleeve Handling
W&H normally showcases new printing technologies at DRUPA. However, with the cancellation of DRUPA 2020, W&H held a successful Virtual Expo in June 2020 and will hold another in 2021 as a platform to introduce new technologies. The company introduced NOVOPORT M and NOVOPORT ADVANCED at the last event.
The NOVOPORT M is a weight-compensated manipulator installed on a motorized lifting platform for semi-automated sleeve changes. The operator determines and controls the movement of the lift and the manipulator. Sleeves and adapters can be inserted easily from the cart into the CI section of the press. NOVOPORT ADVANCED is a fully-automated sleeve handling system that operates with a KUKA robot. The robotic arm automatically retrieves sleeves from a cart and pushes them into the CI section of the press. All the operator has to do is select the correct program and start the process.
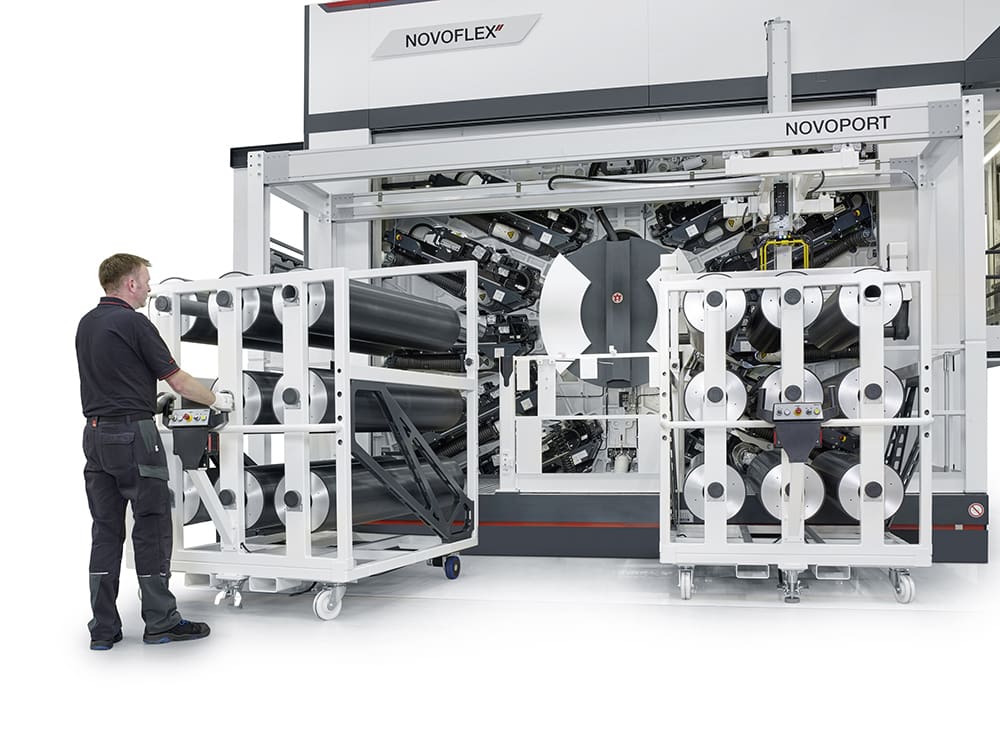
RUBY GO IoT Platform
At K 2019, W&H introduced RUBY GO, a new IoT system platform, and promised “extensions” specific to extrusion, converting and printing. RUBY GO collects, records and displays all production parameters live on the control unit, or on a computer, and has the ability to communicate with third-party equipment. RUBY CHECK was launched during the 2020 Virtual Expo as an extension to help analyze and problem solve, while streamlining production and quality control.
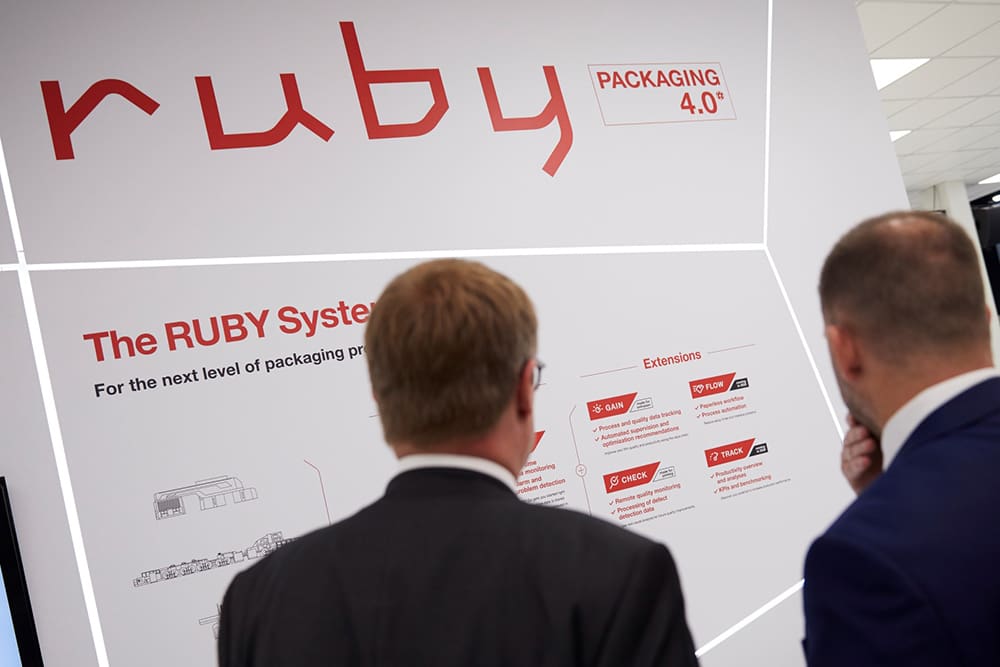
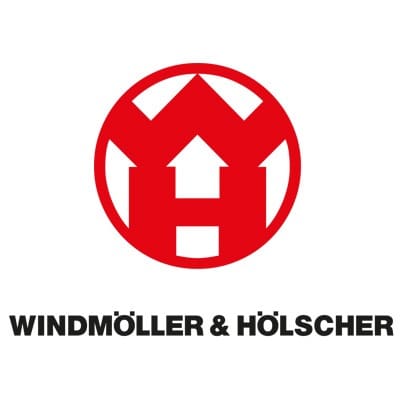